Nanocomposites Tungsten Carbide Prepared from Ammonium Paratungstate 1/2
- Details
- Category: Tungsten Information
- Published on Thursday, 14 January 2016 17:49
- Written by chunyan
- Hits: 284
Nanocomposites material is using resin, rubber, ceramics and metal as continuous phase, and using nanometer sized metal, semiconductor, rigid particles and other inorganic particle, fiber, carbon nanotube modifier as dispersed phase, through appropriate preparation method of modified agent homogeneity of dispersion in the matrix material to form contains nanosize materials of the composite system, also known as nano materials. Carbon nanotube is a kind of ideal modified material, because the properties of high strength, elastic modulus, specific surface area, electrical conductivity, temperature stability and thermal conductivity, low thermal expansion coefficient and good resistance to acid and alkali it has. A method to prepare nanocomposites of tungsten carbide uniform dispersed carbon nanotube in tungsten to achieve mass and universal production. And the original properties of tungsten can remained and also improved.
Principle: Using the adsorption tungsten of carbon nanotube to restore nanocomposites tungsten carbide from ammonium paratungstate in the gas of hydrogen.
Steps as following:
1. Obtaining modified neutral carbon nanotube
Set carbon nanotube in concentrated nitric acid under 65-75℃, ultrasonic dispersion for 20-40min; then heated to 80 to 95℃ and reflux for 1 to 3 hours, after cooling down to room temperature, diluted in ionized water and filtered until the solution become neutral; drying the neutral particles in vacuum environment of 70-85℃ for 1.5 to 3 hours to modify the neutral carbon nanotube.
Remark: 1g carbon nanotube is obtained in 100 ml of concentrated nitric acid.
APT Supplier: Chinatungsten Online ammonium-paratungstate.com | Tel.: 86 592 5129696; Fax: 86 592 5129797;Email:sales@chinatungsten.com |
Tungsten News&Tungsten Prices, 3G Version: http://3g.chinatungsten.com | Molybdenum News & Molybdenum Price: http://news.molybdenum.com.cn |
Year Of Monkey New Year Celebrating Tungsten Gold-plated Blocks
- Details
- Category: Tungsten Information
- Published on Thursday, 14 January 2016 17:48
- Written by yaqing
- Hits: 272
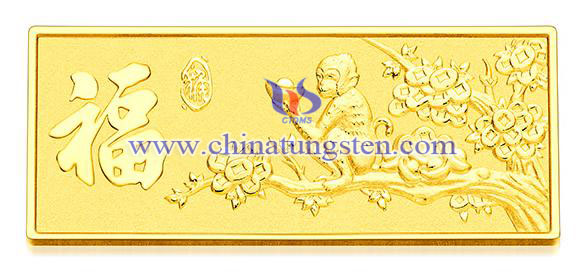
Tungsten Gold Plated Supplier: Chinatungsten Online www.tungsten-alloy.com | Tel.: 86 592 5129696; Fax: 86 592 5129797;Email:sales@chinatungsten.com |
Tungsten News & Prices, 3G Version: http://3g.chinatungsten.com | Molybdenum News & Molybdenum Price: http://news.molybdenum.com.cn |
Molybdenum Sulfide Precipitation Separating Tungsten and Molybdenum from Sodium Tungstate Solution Influence
- Details
- Category: Tungsten Information
- Published on Thursday, 14 January 2016 17:40
- Written by linlu
- Hits: 266
Sodium Tungstate Supplier: Chinatungsten sodium-tungstate.com | Tel.: 86 592 5129696; Fax: 86 592 5129797;Email:sales@chinatungsten.com |
Tungsten News & Prices, 3G Version: http://3g.chinatungsten.com | Molybdenum News & Molybdenum Price: http://news.molybdenum.com.cn |
Tungsten Gold-plated Bars Barrel Plating Production Process
- Details
- Category: Tungsten Information
- Published on Thursday, 14 January 2016 17:41
- Written by yaqing
- Hits: 280
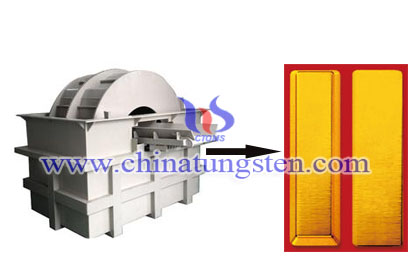
Tungsten Gold Plated Supplier: Chinatungsten Online www.tungsten-alloy.com | Tel.: 86 592 5129696; Fax: 86 592 5129797;Email:sales@chinatungsten.com |
Tungsten News & Prices, 3G Version: http://3g.chinatungsten.com | Molybdenum News & Molybdenum Price: http://news.molybdenum.com.cn |
Molybdenum Sulfide Precipitation Separating Tungsten and Molybdenum from Sodium Tungstate Solution
- Details
- Category: Tungsten Information
- Published on Thursday, 14 January 2016 17:37
- Written by linlu
- Hits: 242
Sodium Tungstate Supplier: Chinatungsten sodium-tungstate.com | Tel.: 86 592 5129696; Fax: 86 592 5129797;Email:sales@chinatungsten.com |
Tungsten News & Prices, 3G Version: http://3g.chinatungsten.com | Molybdenum News & Molybdenum Price: http://news.molybdenum.com.cn |