Tungsten Trioxide Electric Property
- Details
- Category: Tungsten Information
- Published on Monday, 22 February 2016 16:12
- Written by qiongyao
- Hits: 268
When current flows through a conductor, the conductor may have a fever, this heat generated by the current, called electric, or it can be understood as electric power is generated by the heat, the phenomenon of electrical energy becomes into internal energy. The use of electric principle can be made into various electric heaters, such as electric irons, electric stove, electric irons, electric ovens, water heaters, electric hatch boxes.
Electric material is a new energy material which has relatively traditional energy with small size, no noise, no pollution, long life and other characteristics. Thermoelectric materials can be used as electricity and thermal energy conversion intermediary material. The material will appear the temperature difference, and this electric conversion is reversible. Conventional thermoelectric materials have high ZT value (figure of merit, the higher the coefficient, the higher thermoelectric conversion efficiency), and the preparation of a mature technology, it has been widely used in thermoelectric power generation and refrigeration device. Some researchers are finding new thermoelectric materials, although these materials have a higher ZT value, it is the most toxic and precious metal alloys division, the use of these materials will increase in the environment.
Tungsten trioxide (WO3) as important high-tech materials in the electrochromic, the light catalytic degradation, the gas detection and other areas has a wide range of potential applications. WO3 is an n-type thermoelectric material at the same time. Currently, the status quo is thermoelectric materials research with P-type thermoelectric material, but it is necessary for the production of thermoelectric devices p-type matches with n-type. Early, studies have shown that WO3 doped thermoelectric performance, which has been improved. If we find a important dopant and it will be the best process parameters for WO3 thermoelectric properties, it is possible to WO3 used in thermoelectric materials.
Tungsten Oxide Supplier: Chinatungsten Online www.tungsten-oxide.com | Tel.: 86 592 5129696; Fax: 86 592 5129797;Email:sales@chinatungsten.com |
Tungsten News & Prices, 3G Version: http://3g.chinatungsten.com | Molybdenum News & Molybdenum Price: http://news.molybdenum.com.cn |
Sapphire Single Crystal Growing Tungsten Crucible Thermal Stress Analysis
- Details
- Category: Tungsten Information
- Published on Friday, 19 February 2016 17:15
- Written by yiping
- Hits: 280
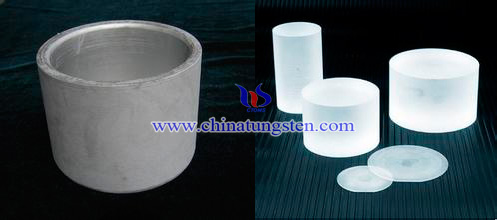
Tungsten Supplier: Chinatungsten Online www.chinatungsten.com | Tel.: 86 592 5129696; Fax: 86 592 5129797;Email:sales@chinatungsten.com |
Tungsten News & Prices, 3G Version: http://3g.chinatungsten.com | Molybdenum News & Molybdenum Price: http://news.molybdenum.com.cn |
Cleaning SCR Denitration Catalyst on Production Process
- Details
- Category: Tungsten Information
- Published on Friday, 19 February 2016 16:41
- Written by chunyan
- Hits: 276
The activity of SCR denitration catalyst in-service will decrease by being abraded from flue gas, deposited from solid material, poisoned from alkali metal. And then after 2 or 3 years the catalyst would lose activity and end its life. Cleaning the SCR denitration catalyst is becoming very necessary because it costs high, and belongs to consumables. At the same time, the waste catalyst is difficult to handle because of the toxicity which will cause secondary pollution to the environment easily. We push a method for cleaning SCR denitration catalyst on the production process, steps as following:
1. Configure the cleaning solution
Stirring with a machine to mix oxalic acid solution, dispersing agent MF, ammonium metavanadate and ammonium paratungstate for more than 10 minutes for generating cleaning solution. Among them, the mass concentration that MF is 0.1-1wt%, ammonium metavanadate is l-3wt%, and ammonium paratungstate controlled at 5-15wt%. The pH value of the oxalic acid solution supposed to be 5-7;
2. Blowing and cleaning the surface of SCR denitration catalyst by a sonic soot-blower for 15s, and then cleaning the surface and pore of catalyst for 1min in certain circumstances;
3. Washing the SCR denitration catalyst for 5mins, and collect the waste liquid at the same time;
4. Washing the SCR denitration catalyst with cleaning solution for 10-20mins, also the waste liquid should be collected;
5. Dry the catalyst through a hot air drying device for 2-4 hours, thus finish the progress of cleaning SCR denitration catalysts.
APT Supplier: Chinatungsten Online ammonium-paratungstate.com | Tel.: 86 592 5129696; Fax: 86 592 5129797;Email:sales@chinatungsten.com |
Tungsten News&Tungsten Prices, 3G Version: http://3g.chinatungsten.com | Molybdenum News & Molybdenum Price: http://news.molybdenum.com.cn |
Preparing Composite Powder Tio2-Wo3-Sio2 Used as Catalyst Carrier
- Details
- Category: Tungsten Information
- Published on Friday, 19 February 2016 16:45
- Written by chunyan
- Hits: 275
Anatase nanometer TiO2 is mainly used as activity carrier for denitration catalyst. Because of TiO2 composites with WO3 in TiO2-WO3-SiO2 powder, the structure and surface properties have been changed. Also it causes WO3 distributing more uniform, thus improve the processing performance which is advantageous to mixing, extruding, drying process, thus ensure rate of finished products. We propose a method for preparing composite powder TiO2-WO3-SiO2, and the specific steps as follows:
1. Beating and dispersing the raw material H2TiO3, and then adjust the concentration of titanium dioxide slurry;
2. Add ammonium paratungstate and white carbon black into the slurry;
3. Add ammonia to adjust pH to 5.5~8.5 for improving combination with WO3 and the calcination properties of metatitanic acid;
4. Filtrating and dehydrating the slurry to get massive cake, in which mass fraction of TiO2is controlled in 40%~55%;
5. Crushing massive cake mechanical, then drying it at 200~380℃ for 2.5 hours, and then calcined 380~680℃ for 4.5 hours;
6. Crushing to generate the required composite powder TiO2-WO3-SiO2.
The method descripts above has the following advantages:
1) Low manufacturing cost, simple process;
2) The products obtained are not only with long service life and high surface area, surface chemical activity, good processing performance, but also have the advantages of high mechanical strength and resistance to erosion.
APT Supplier: Chinatungsten Online ammonium-paratungstate.com | Tel.: 86 592 5129696; Fax: 86 592 5129797;Email:sales@chinatungsten.com |
Tungsten News&Tungsten Prices, 3G Version: http://3g.chinatungsten.com | Molybdenum News & Molybdenum Price: http://news.molybdenum.com.cn |
Tungsten Carbide Ball Grinding Methods (2/2)
- Details
- Category: Tungsten Information
- Published on Friday, 19 February 2016 16:27
- Written by xiaobin
- Hits: 263
Tungsten carbide ball double V-slot grinding can ensure that the rotation angle of the ball will change with sphericity, but it requires that the grinding tray V-slot up and down has higher properalignment and shape error and assembly error institutions needed to be effectively controlled, otherwise the blank ball can not roll along the groove smoothly. The relevant domestic scholars have done a lot of this research and developed a conical grinding method in which the abrasive disk is tapered, which makes carbide ball blank has a large corner across from the milling process (usually up to 45 ° left and right), to obtain a full rotation, enhanced rotary slide ball blank, improving overall processing efficiency. The following is a schematic view of the three grinding work mode, you can clearly see different from the design of the grinding tray:
Besides these three kinds of conventional grinding methods, Related researchers and academics abroad in order to achieve high-speed grinding ceramic balls have also proposed a flexible and high material removal rate of magnetic fluid polishing. Its basic principle is to use magnetic fluid mixing abrasive particles as an abrasive, when the magnetic fluid is given a certain magnetic field, the magnetic fluid will produce upward thrust, by the corresponding floating disc ceramic balls implement processing load. It remarkably improve the efficiency of precision ceramic ball and its roundness error less than 0.14μm, surface roughness reaches 0.01μm, material removal rate reaches 12μm / min, which is more than 40 times that of conventional grinding method.
However, this method due to the complex structure, inconvenient operation, and the magnetic fluid itself heightening price, after the magnetic fluid and particles worn when machining, material removal will be affected to some extent, it is also the emergence of a non-magnetic fluid polishing (water and glycerol mixture) instead of magnetic fluid and resin bonded diamond grinding wheel instead of embedding the abrasive grinding tray. Although the processing efficiency and processing efficiency and non-abrasive magnetic fluid magnetic fluid grinding pretty, its precision can not be fully guaranteed, both of structure of them are relatively complex, which is not suitable for large-volume production of high-precision machining of tungsten carbide ball.
Tungsten Carbide Supplier: Chinatungsten Online tungsten-carbide.com.cn | Tel.: 86 592 5129696; Fax: 86 592 5129797;Email:sales@chinatungsten.com |
Tungsten News&Tungsten Prices, 3G Version: http://3g.chinatungsten.com | Molybdenum News & Molybdenum Price: http://news.molybdenum.com.cn |