Tungsten Trioxide Denitration Catalyst with Dioxin Removable
- Details
- Category: Tungsten Information
- Published on Friday, 13 May 2016 16:54
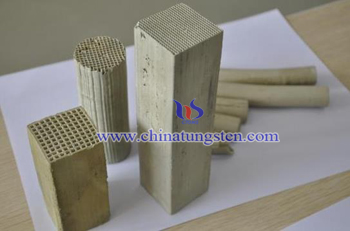
Tungsten Oxide Supplier: Chinatungsten Online www.tungsten-oxide.com | Tel.: 86 592 5129696; Fax: 86 592 5129797;Email:sales@chinatungsten.com |
Tungsten News & Prices, 3G Version: http://3g.chinatungsten.com | Molybdenum News & Molybdenum Price: http://news.molybdenum.com.cn |
Tungsten Trioxide Waste Denitration Catalyst Recovers Metal Oxide
- Details
- Category: Tungsten Information
- Published on Friday, 13 May 2016 16:51
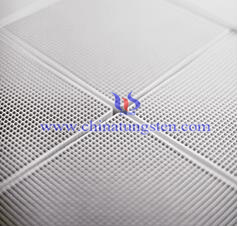
Tungsten Oxide Supplier: Chinatungsten Online www.tungsten-oxide.com | Tel.: 86 592 5129696; Fax: 86 592 5129797;Email:sales@chinatungsten.com |
Tungsten News & Prices, 3G Version: http://3g.chinatungsten.com | Molybdenum News & Molybdenum Price: http://news.molybdenum.com.cn |
Tungsten Carbide Anvil Wear Mechanism (2/2)
- Details
- Category: Tungsten Information
- Published on Friday, 13 May 2016 16:49
Due to the structure of anvil has some complexity, it is difficult to obtain the stress distribution of tungsten carbide anvil under ultra-high pressure by a simple experiment. But it is also a crucial factor to analyze the wear mechanism, stress distribution and the relations of geometric parameters. So the related scholars and researchers use model simulation carbide anvil in the actual work of the forces by finite element analysis theory and related software. Through Finite element analysis model, it is known that acting on the top surface of the hammer cylinder radial preload from an interference fit between the anvil and the preload ring. Preload is essentially the contact pressure, and its main role is to provide lateral support for the anvil to improve stress distribution under actual working conditions.
From the point of view of stress distribution, preload distribution is very uneven, gradually decreasing from the bottom to the top. The stress in the four corners is relatively concentrated, but also the most likely to crack parts, which produces small cracks start from the stress concentration occurs at the micro cracks and gradually increased to the top surface of the anvil extension. These parts are neither covered within the scope of pyrophyllite, nor take advantage of the strengthening force top hammer steel ring, so in most cases they completely rely on their own strength to bear the stress.
Furthermore, tungsten carbide has certain fragility and poor shear resistance. It is normal that tensile stress and shear stress appear simultaneously in the process of anvil working, which will has a sharp increase of internal stress after loading. Especially, when the accumulated fatigue or load is too large, the internal material will yield and at the edge of the anvil surface crack formation under the action of shear stress; the radial shear stress will expand the cracks area and resulting in cemented carbide material in axial compression stress of sliding, eventually leading edge broken or crushed.
In order to reduce the wear and avoid the cracking and crushing of the anvil, the relevant researchers study from two aspects, one is the release of stress, the other is improve the interference fit. And the internal stress includes the stress of grinding and machining process. The anvil just after grinding is better to use after 3 month storing to ensure the release of the internal stress. Some academics have proposed that put the grinded anvil into muffle furnace and heat gradually cooled after 3-7h. However, this process requires high precision of vary parameters controlling, or the micro cracks will expand because of the heating and cooling; Anvil and increase the amount of interference with the steel ring will help improve the strength of the anvil, but it will increase the workload of the steel ring, reducing the strength of the tightening ring, its service life will be greatly shortened.
Tungsten Carbide Supplier: Chinatungsten Online tungsten-carbide.com.cn | Tel.: 86 592 5129696; Fax: 86 592 5129797;Email:sales@chinatungsten.com |
Tungsten News&Tungsten Prices, 3G Version: http://3g.chinatungsten.com | Molybdenum News & Molybdenum Price: http://news.molybdenum.com.cn |
Tungsten Carbide Anvil Wear Mechanism (1/2)
- Details
- Category: Tungsten Information
- Published on Friday, 13 May 2016 16:45
Tungsten carbide anvil consists of hard phase WC and binder phase Co, which has higher density, higher hardness, excellent wear resistance and corrosion resistance. It plays an important role in some super-hard materials machining process, such as synthetic diamond, CBN (Cubic Boron Nitride) and so on. The service life of tungsten carbide anvil will affect synthetic diamond properties and overall machining efficiency directly. In general, there are two kinds of evaluation criteria of tungsten carbide anvil quality, one is the frequency of use, and the other is ten thousand karats consumption.
Actually, tungsten carbide grades used in anvil usually YG6, YG8, YG12, etc. And compared with the powder with medium grain, the fine grain will remarkably improve the hardness, compressive stress, flexural strength, impact toughness and other properties. Sintered tungsten carbide anvil with medium grain service life is about 5,000 times ten thousand karats consumption> 3kg; compared with tungsten carbide anvil with fine grain hardness generally reach more than HRA90.5, bending strength of 3000MPa, the average service life is more than 8,000 times, ten thousand karats consumption <1.5kg.
Domestic synthetic diamond industry mainly is based on hexa-orientation, and six anvil compacts the six face simultaneously. Each anvil is composed by the hammer, steel ring and pad. It works through the steel ring interference fit with the hammer, a steel ring on the anvil to impose certain radial preload in six hydraulic cylinders driven, six tungsten carbide anvils are acting on the high-pressure cavity composed by pyrophyllite hexahedron, which change the graphite inside the cavity into diamond by the catalytic effect under high temperature and pressure. Pyrophyllite is a hydrous aluminum silicate layered structure, in the process of synthesis plays role in pressure transmission, sealing and insulation effect.
Tungsten Carbide Supplier: Chinatungsten Online tungsten-carbide.com.cn | Tel.: 86 592 5129696; Fax: 86 592 5129797;Email:sales@chinatungsten.com |
Tungsten News&Tungsten Prices, 3G Version: http://3g.chinatungsten.com | Molybdenum News & Molybdenum Price: http://news.molybdenum.com.cn |
HORIBA Carbon Sulfur Analyzer and Tungsten Granule
- Details
- Category: Tungsten Information
- Published on Friday, 13 May 2016 11:29
HORIBA brand in Japan was established in January 26, 1953, which is the world's leading provider of analytical techniques and measurement systems. In the past few years, this brand has been committed to protecting the environment, and has made considerable development, making great contributions to safety and health undertakings environmental protection of the whole world. Whether is the basis or the applications of technology, HORIBA upholds the concept to develop technology to the extremes, making efforts into further improvement of the quality and reliability of the carbon sulfur analyzer. Always adhere to the highest standards.
The EMIA series is main product of HORIBA carbon sulfur analyzer, this series instrument use the high frequency induction heating method that has the function of controlling the combustion. In this way, it can analyze metals and other inorganic materials, or analyze coal and other non-metallic materials and organic matter. What’s more, it can choose the most suitable way to heat in accordance with the different samples and application. In addition, the use of dust filters to heat can reduce the adsorption of SO2, so that we can enhance the stability of sulfur analysis results.
Using four non-dispersive infrared detector that are CO, high CO2, low CO2, SO2 infrared detector and it can be increased automatic cleaning mechanism in accordance with users’ requirements, in order to get the detection of carbon and sulfur with a high-precision, high performance, easy operation, and it can directly enter data transmission network. The EMIA series has a powerful data analysis processing capabilities, with the extraction, heating, dynamic display release profile, graphical comparisons and other excellent features, a large number of data processing software offer simple and efficient analytical tools for the production and research. In addition, the use of tungsten granule as a flux, EMIA series HORIBA carbon sulfur analyzer can analyze by changing the heating conditions through the current set at the both ends of the heating plate. This feature can analyze the carbon of surface and carbon inside sample respectively.
In 2003, to commemorate the 50th anniversary of the establishment of Horiba, HORIBA Group established an award for young scientists in the field of analytical science outside the group companies. The award is intended to support for researchers who are dedicated to the analysis and development of measurement innovative technologies.
Tungsten Metals Supplier: Chinatungsten Online www.tungsten.com.cn | Tel.: 86 592 5129696; Fax: 86 592 5129797;Email:sales@chinatungsten.com |
Tungsten News & Prices, 3G Version: http://3g.chinatungsten.com | Molybdenum News & Molybdenum Price: http://news.molybdenum.com.cn |
Behr Labor-Technik Carbon Sulfur Analyzer and Tungsten Granule
- Details
- Category: Tungsten Information
- Published on Friday, 13 May 2016 11:24
In Germany there are a large number of carbon sulfur analyzers that are well-known in the world, such as Eltra, Elementar, and Behr Labor-Technik. As a global leader on the area of chemical element analysis, CHNOS elemental analyzer of Elementar holds more than 95% market share in the world. Behr Labor-Technik carbon sulfur analyzer possesses a high quality and a great reliability that is one of reasons for enjoying great popularity.
Laboratory technique of Behr is now developing into an international brand from a small family workshop, which has experienced 50 years for researching, developing, and marketing production of laboratory equipment. Currently, the centre of gravity of its work is a laboratory equipment of food analysis. Over the years, Behr Labs technology has been leading on this area of German products. According to the standard method of analysis techniques, Behr is carrying out regular testing of food quality everywhere in the world. Behr Labs technology provides for the devices for these detecting, their daily work is safe and easy.
In 1951, Behr Labor-Technik was established in Germany to develop, produce and sale the laboratory equipments, Behr Labor-Technik carbon sulfur analyzer mainly use tungsten granule as the primary flux. The speed of C50HT, S50 and CS50 series of analytical instruments for carbon and sulfur content is fast and their accurate analysis results with a great reliability, including from the content of ppm level to the content of % level. At present, this type of carbon sulfur analysis instruments are also widely applied in iron and steel, non-ferrous metals, alloys, carbides, ceramics, minerals, coal, coke, oil, dust, carbonate catalyst, soils, sediments, plaster, plastic, waste, sand, glass and others.
Analysis principle of Behr carbon sulfur analyzer is to determine the content of carbon dioxide and sulfur dioxide by non-dispersive infrared (NDIR) after the high temperature combustion technology. NDIR is a method which is the basis of the theory of the absorption of the gas. After the infrared emanation released by infrared light source is absorbed by a certain gas which is to be measured, spectral intensity will change that is proportional to the gas concentration therefore, variable quantity of spectral intensity can adversely detect concentration of gas which is to be measured.
Tungsten Metals Supplier: Chinatungsten Online www.tungsten.com.cn | Tel.: 86 592 5129696; Fax: 86 592 5129797;Email:sales@chinatungsten.com |
Tungsten News & Prices, 3G Version: http://3g.chinatungsten.com | Molybdenum News & Molybdenum Price: http://news.molybdenum.com.cn |
Tungsten Alloy Shielding And Radiographic Testing Technology
- Details
- Category: Tungsten Information
- Published on Thursday, 12 May 2016 18:23
Radiographic testing technology is a nondestructive testing method of inspecting materials for hidden flaws by using the ability of radiation (X-ray produced by an accelerator and γ-ray generated by the nuclear decay of radioactive isotopes) to penetrate various materials and the decay characteristic of radiation in materials. Radiographic testing technology can be used to detect the internal defects in metal and non-metallic materials and products, such as weld pores, cracks, porosity, segregation, slag, incomplete penetration and so on. Since the thickness and density of each portion of the detected object varies for the defects, and the radiation attenuation under different density and thickness of materials is different. So when a beam of uniform radiation irradiates the detected object, and if the partial region of the object exists flaws or there are some differences between the structures, the transmitted intensity of radiation would differ in different areas, which can be detected to determine the internal defects and the structural distribution of objects.
The common devices used for radiographic testing include X-ray detector and γ-ray detector. These two detectors use X-rays and γ-ray to detect flaws respectively. The γ ray has a strong penetrating power. When the body suffers from the γ ray exposure, γ-ray can enter into the human body, and interact with the human body cells, thus eroding the complex organic molecules (such as proteins, nucleic acids and enzymes), so that the body's normal chemical process is disturbed, severe may lead to cell death. While X ray can suppress, damage or even kill human cells, resulting in varying degrees of body changes in the physiology, pathology and biochemical aspects. And X-ray can also lead to hair loss, skin burns, sight disorders, leukemia and other issues. Therefore, people should pay attention to the radiation damage while using the radiographic testing technology, and pay attention to take protective measures.
Due to the high density, good corrosion resistance, high radiation absorption capacity and high strength of tungsten alloy, tungsten alloy shielding is the best choice to shield the radiation released from the use of radiographic testing technology. Compared to traditional radiation shielding materials (such as lead and boron carbide), tungsten alloy shielding provides excellent density with small capacity. With the same weight, high-density tungsten alloy shielding can provide the same energy absorption as lead using 1/3 less space. And tungsten alloy shielding is nontoxic, neither pollute the environment, but also will not endanger human health, it is extremely environmentally friendly shielding material.
Tungsten Alloy Supplier: Chinatungsten Online www.tungsten-alloy.com | Tel.: 86 592 5129696; Fax: 86 592 5129797;Email:sales@chinatungsten.com |
Tungsten News & Prices, 3G Version: http://3g.chinatungsten.com | Molybdenum News & Molybdenum Price: http://news.molybdenum.com.cn |
Tungsten Bronzes Preparation by Ball Milled Solid Phase Reaction
- Details
- Category: Tungsten Information
- Published on Thursday, 12 May 2016 17:50
Tungsten Oxide Supplier: Chinatungsten Online www.tungsten-oxide.com | Tel.: 86 592 5129696; Fax: 86 592 5129797;Email:sales@chinatungsten.com |
Tungsten News & Prices, 3G Version: http://3g.chinatungsten.com | Molybdenum News & Molybdenum Price: http://news.molybdenum.com.cn |
Tungsten Copper Contact Tip (2/2)
- Details
- Category: Tungsten Information
- Published on Thursday, 12 May 2016 17:25
Theoretically, the room temperature strength of metal depends on two basic factors: one is binding force of metal atom, the other one is the resistance to dislocation motion. Common by increasing resistance to dislocation movement to improve the strength and work hardening methods are split out strengthened. However, these methods the effect of increasing temperature decreases until it disappears, and some rely precipitates precipitation hardening copper alloy, when raised to a certain temperature, the precipitate into the matrix meet again, so that a sharp decline in the strength of the material. By comparison, tungsten copper material does not has phase change, recrystallization phenomena at high temperature and the physical and chemical properties are stable.
The experiments show that 70W-Cu has higher hardness and better electrical conductivity than beryllium cobalt copper, and its softening temperature is twice more than beryllium cobalt copper, so as for flash butt welding electrode wear or require a higher arc welding contact tip applies quite well. There is a comparison between tungsten copper contact tip and brass contact tip:
From the table we can see that the contact tip compared to tungsten copper contact tip brass longer life, better welding performance, which can effectively improve the overall efficiency. In addition, in the process of vertical welding, when the thickness of the weldment 22-28mm, wire diameter φ2.4mm, 2.8mm the pore size of the contact tip, tungsten copper contact tip and chromium copper contact tip after welding has a great difference in wear. Tungsten copper welding contact tip at 20m, the circular aperture can remain unchanged, ensure the continue welding; The chromium copper welding contact tip about 2m, circular conductive mouth to occur due to poor abrasion resistance unilateral eccentric, expand the aperture and are unable to continue welding. Overall, tungsten copper contact tip has higher hardness, better thermosetting, wear resistance, excellent arc ablation resistance, anti-adhesion, which is a kind of contact tip materials with a broad application prospect.
Tungsten Copper Supplier: Chinatungsten Online tungsten-copper.com | Tel.: 86 592 5129696; Fax: 86 592 5129797;Email:sales@chinatungsten.com |
Tungsten News & Prices, 3G Version: http://3g.chinatungsten.com | Molybdenum News & Molybdenum Price: http://news.molybdenum.com.cn |
Tungsten Copper Contact Tip (1/2)
- Details
- Category: Tungsten Information
- Published on Thursday, 12 May 2016 17:23
Tungsten copper contact tip is a kind of welding consumables and it is generally located in the end of welding torch, which play a role in delivering welding wire. According to the hole shape, it can be divided into round, square, ellipse, triangle and so on. Common used materials for contact tips include pure copper, brass, beryllium copper, chromium zirconium copper, beryllium cobalt copper, etc.
In the resistance welding process, not only requires the contact tip has good electrical conductivity, but also required at high temperatures still has high strength, wear resistance and corrosion resistance to electrical properties. In practical, the contact tips use pure copper and beryllium copper, which have poor wear resistance and during welding process will easily spatter adhesion. It cause clogging of the tip or the wire and the contact tip bonding, which make the contact tip failure. Furthermore, replacing contact tip frequently will affect the welding performance and decrease the overall efficiency. Compared with pure copper, chromium zirconium copper and beryllium cobalt copper has higher hardness and better wear resistance at room temperature. But it has fewer sources, relatively complex process and higher cost.
Tungsten copper has both advantages of W and Cu, which not only has higher hardness, but also has excellent wear resistance, galvanic corrosion and higher softening temperature. Whether as the electrical resistance welding electrode with special requirements for the stress or as the contact tip used in arc welding, tungsten copper material has a great advantage, which is an important role of the electrical processing and welding occasion. Tungsten copper contact tip is sintered by tungsten and copper composite powder and the tungsten skeleton uniformly distributed in the copper matrix. When the temperature exceeds the melting point of copper, tungsten skeleton liquid copper can stick as a huddle and constitute a good conductor of heat passage, so tungsten skeleton area overheating does not occur in the process.
Tungsten Copper Supplier: Chinatungsten Online tungsten-copper.com | Tel.: 86 592 5129696; Fax: 86 592 5129797;Email:sales@chinatungsten.com |
Tungsten News & Prices, 3G Version: http://3g.chinatungsten.com | Molybdenum News & Molybdenum Price: http://news.molybdenum.com.cn |