Tungsten Carbide / Graphene Self-lubricating and Wear-resistant Coating
- Details
- Category: Tungsten Information
- Published on Monday, 03 September 2018 22:40
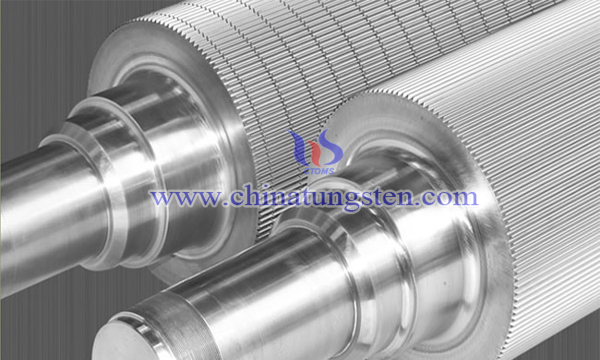
Tungsten carbide spraying powder is the basis of preparing tungsten carbide wear-resistant coatings by thermal spraying. To prepare tungsten carbide wear-resistant coatings with self-lubricating properties, self-lubricating additives must be added to tungsten carbide spraying powder. At present, self-lubricating additives mainly include soft metals (Au, Ag, etc.), fluoride (LiF2, CaF2, etc.) and so on. Disulfides (MoS2, WS2, etc.) and metal oxides (Zr2O3, Cr2O3, etc.) have been extensively studied as lubricating phases for coatings.
Nickel Cobalt Molybdenum Tungsten Hydrodesulfurization Catalyst
- Details
- Category: Tungsten Information
- Published on Monday, 03 September 2018 22:32
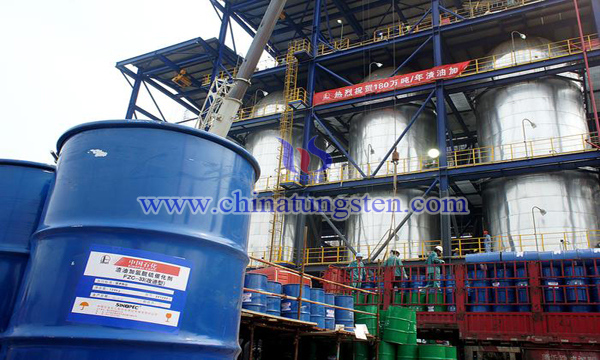
At present, hydrofining catalysts are usually prepared by introducing active metal components from solution or suspension into the carrier through impregnation, and then by drying and calcination. Among them, nickel cobalt molybdenum tungsten sulfide is a highly active hydrodesulfurization catalyst.
Decomposition Process of Wolframite in Mixed Symbiosis Ore
- Details
- Category: Tungsten Information
- Published on Monday, 03 September 2018 22:21
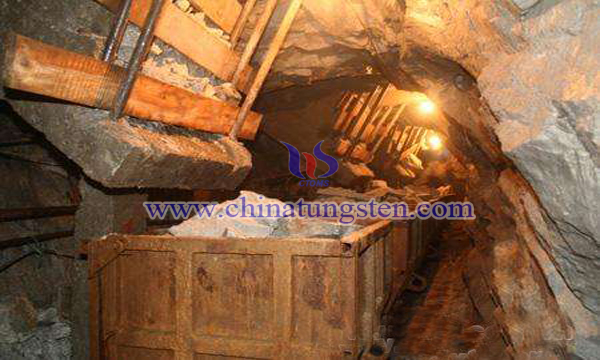
In many scheelite deposits in China, scheelite is not only associated with scheelite, but also with wolframite. For example, Xingluokeng, Fujian Province, is a super-large wolframite-scheelite deposit, with tungsten reserves of about 300,000 tons, and scheelite and wolframite reserves accounting for half of each.
Recovery of Fluorite from Scheelite Flotation
- Details
- Category: Tungsten Information
- Published on Monday, 03 September 2018 22:09
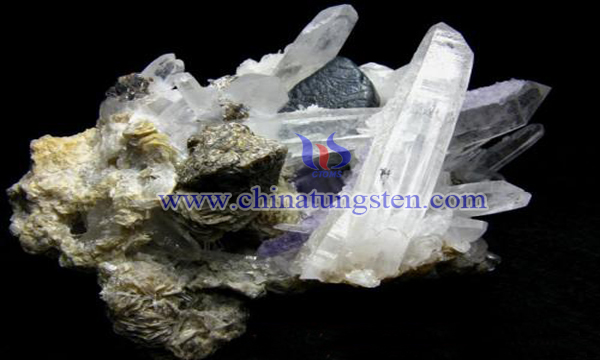
Fluorite is the most important mineral in fluoride. It has unique physical and chemical properties and wide uses. It plays an important role in industrial development. Like tungsten, fluorite reserves, mining and exports in China rank first in the world.
Ultrafine Tungsten Powder Preparation from ART Self Reduced Tungstate
- Details
- Category: Tungsten Information
- Published on Sunday, 19 August 2018 23:21
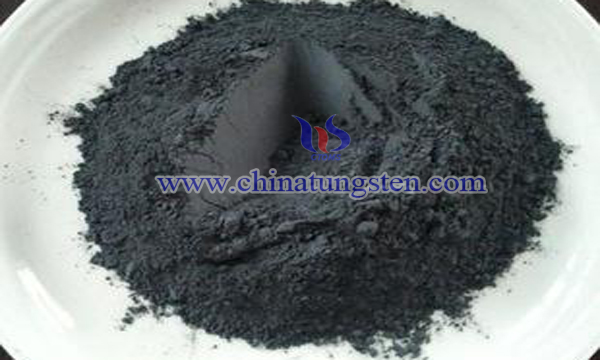
At present, in the production of tungsten powder, most of the tungstate thermal decomposition of blue tungsten oxide, blue tungsten oxide hydrogen reduction process to tungsten powder. The conventional process generally uses ammonium paratungstate as the initial raw material, but it is difficult to obtain ultrafine tungsten powder with average particle size of less than 1 micron by hydrogen reduction.
Leaching Process of High Calcium Wolframite Concentrate
- Details
- Category: Tungsten Information
- Published on Sunday, 19 August 2018 23:12
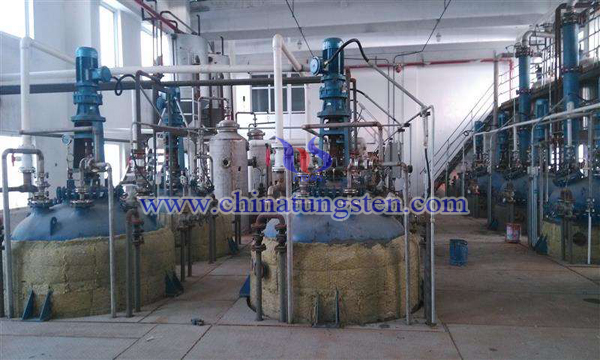
China has abundant tungsten resources, and reserves and concentrate output rank first in the world. However, the tungsten concentrates produced in several important tungsten mines belong to high calcium wolframite concentrates. At the same time, a considerable amount of refractory tungsten slime containing calcium is produced in each tungsten concentrator. There is no suitable treatment method at present.
Supported Phosphotungstic Acid Catalyst Preparation
- Details
- Category: Tungsten Information
- Published on Sunday, 19 August 2018 23:00
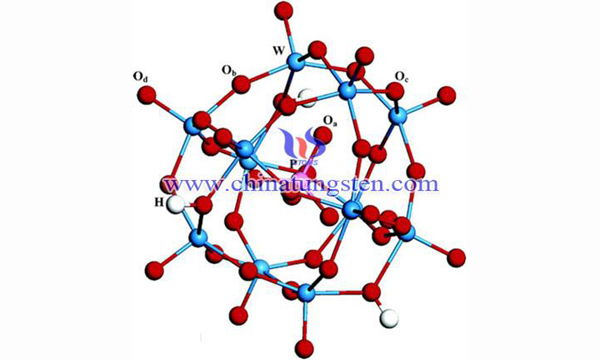
Carboxylic esters are a kind of basic organic chemical raw materials. They are widely used in perfumes, flavors, plasticizers, solvents, resins, coatings, cosmetics, pharmaceuticals, surfactants and organic synthetic intermediates. They have broad market demand at home and abroad.
Tungstic Manganese Calcium / Mesoporous Tungsten Trioxide Composite Catalyst
- Details
- Category: Tungsten Information
- Published on Sunday, 19 August 2018 22:52
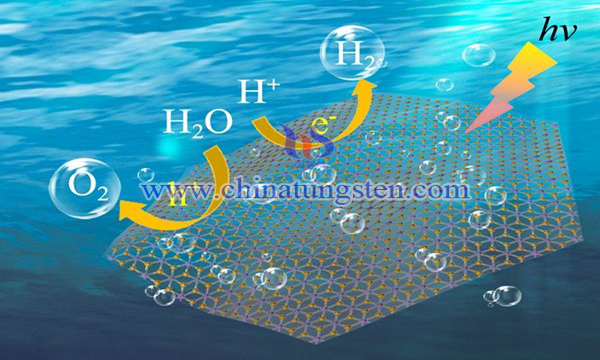
Hydrogen is a kind of clean energy with high calorific value, friendly environment and convenient transportation. The combustion product is water, which does not cause any harm to the environment. The earth is rich in water, easy to get and cheap. Sunlight is an ideal way to convert solar energy into chemical energy.
Tungstate Nanomaterials Preparation by Low Temperature Hydrothermal Method
- Details
- Category: Tungsten Information
- Published on Sunday, 19 August 2018 22:44
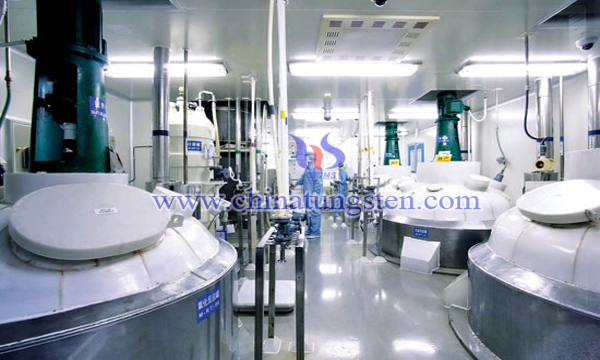
Tungstate nanomaterials have been widely used in many fields, such as optics, electricity, magnetism, conductor/superconductor, catalysis, biology and so on. The synthesis methods of transition metal tungstate materials mainly include sol-gel method, copolymer-assisted synthesis method, inverted micelle soft template method, wet chemical method and solution synthesis method.
Composition of Tungsten Carbide Mining Button
- Details
- Category: Tungsten Information
- Published on Wednesday, 15 August 2018 09:38
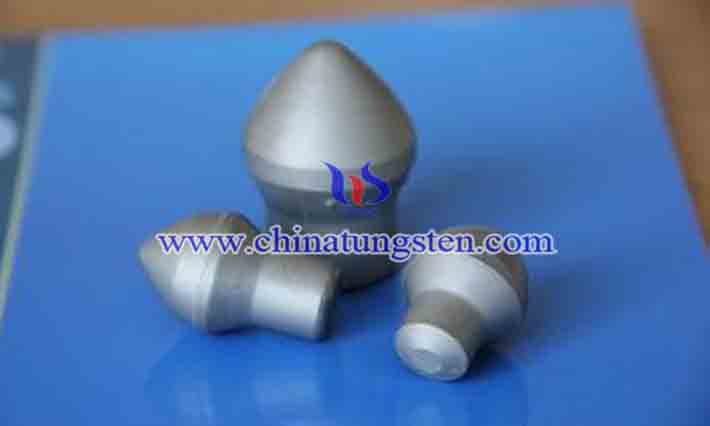