Tungsten Oxide Insulating Glass Makes Eco-friendly Society
- Details
- Category: Tungsten Information
- Published on Friday, 21 September 2018 19:36
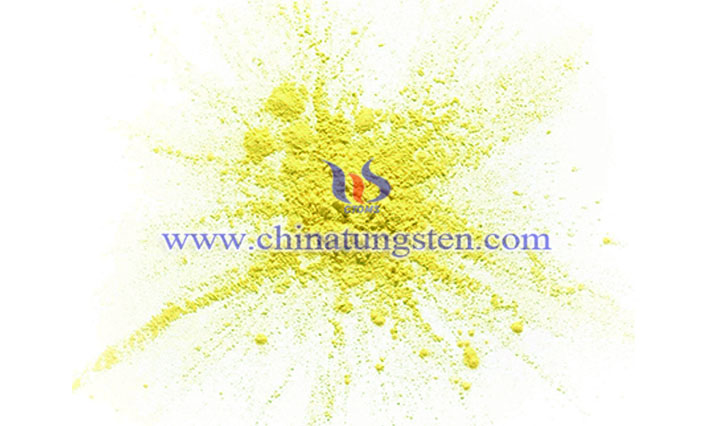
Tungsten oxide insulating glass is a new type of eco-friendly building material. During the glass producing process, a proper proportion of rare metal oxide tungsten trioxide is added to make the glass have better thermal insulation performance, and barrier the ultraviolet rays and infrared ray from the sun. In Europe and America, it has become the industry standards to use the thermal insulating glass in the architecture project. The increasingly energy crisis has got the Chinese government attention, and the government cast the proposal to build eco-friendly society through using the eco-friendly and energy-saving materials in the different industries.
Mo Crucible and Assembling Mold
- Details
- Category: Tungsten Information
- Published on Monday, 17 September 2018 20:13

In order to save the cost, the production of Mo crucible mainly uses the assembling mold with the method of powder metallurgy.
The feature of Mo crucible is that the part is composed of wall cylinder and the hypo-cone.
The ratio of height to thickness of the wall cylinder is close to 8. It is easy to generate the cracks on the surface during the manual pressing. Therefore, we use the assembling molds and adopt the method of powder metallurgy to solve this problem. Due to the friction between powders and between powder and molds, the pressure loss occurs during the pressing. We adopt the double-direction pressing in order to increase the density of hypo-cone and ensure the uniformity of green compact density. After finishing the first pressing, the die cushion will be removed and the second pressing starts. In order to facilitate the demolding of the hypo-cone of the Mo crucible from the base, the base is composed of three vertically and equitably separated block (include the die block, the upper die punch and the wall cylinder of the Mo crucible).
The advantages of using the assembling molds are listed as below:
1.0 The use of assembling mold for pressing can help control the density of various parts of Mo crucible, and ensure that the density of parts of the parts are consistent.Therefore, it improves the performance of the process.
2.0 The adoption of double-direction pressing compensates for the low density caused by the pressure loss and increases the density of every part.
3.0 The base of assembling mold is composed of three parts which can solve the problem that the hypo-cone part is not easily demolded. The application of assembling mold is one of the effective ways to produce the Mo crucible. The promotion of this method can show the feature of powder metallurgy production and accelerate the development of powder metallurgy industry.
- TZM Manufacturer & Supplier, Chinatungsten Online: titanium-zirconium-molybdenum.com
- Tungsten News & Prices of China Tungsten Industry Association: www.ctia.com.cn
- Molybdenum News & Price: news.molybdenum.com.cn
- Tel.: 86 592 5129696; Fax: 86 592 5129797; Email: sales@chinatungsten.com
Iridium Tube Function- Production of Tungsten Iridium Stream Mouth
- Details
- Category: Tungsten Information
- Published on Monday, 17 September 2018 20:07

Iridium is the element in Ⅷseries. The Iridium is the main product of Iridium which is characterized by high melting point, boiling point, hardness, density, elastic modulus and corrosion resistance and low Poisson’s ratio. One of its main application is to combine with tungsten in order to produce tungsten iridium stream mouth.
The iridium tube owns the following properties:
1.0 High corrosion resistance
2.0 High erosion resistance of silicate at elevated temperature
3.0 High erosion resistance of the melting reagent
4.0 Good plasticity at over 1600 centigrade
5.0 High elastic modulus, low Poisson’s ratio and low plasticity at low temperature
6.0 High melting point, boiling point, hardness and density
7.0 Good ductility, electrical conductivity and heat conductivity
Tungsten iridium stream mouth is the combination of tungsten basal body and the iridium tube. Its properties (such as the wear resistance, hardness, strength and so on) got a further improvement so that guarantees the uniformity of products. It is these properties that make it an indispensable component in today's high-tech crystal industry. The density of the tube is not less than 21.00g/cm3, and the purity of iridium is not less than that of SM-Ir99.95 iridium powder in the GB/T 1422. The degree of curvature is not more than 5mm/m, and its internal and external surfaces are smooth without the defects, such as burr, crack and so on.
The stream mouth is widely applied the metallurgy of rare earth metals, the heater of the induction furnace, the smelting of the silex and so on.
- TZM Manufacturer & Supplier, Chinatungsten Online: titanium-zirconium-molybdenum.com
- Tungsten News & Prices of China Tungsten Industry Association: www.ctia.com.cn
- Molybdenum News & Price: news.molybdenum.com.cn
- Tel.: 86 592 5129696; Fax: 86 592 5129797; Email: sales@chinatungsten.com
Type of Hot Runner Nozzle System
- Details
- Category: Tungsten Information
- Published on Monday, 17 September 2018 20:03

Hot runner applied to the injection mold during the production of the TZM alloy is the assembly of heating components that put the melting plastic into the cavity.
Generally, the hot runner systems can be divided into single-headed hot runner system, multi-headed hot runner system and valve-regulated hot runner system. The single-headed hot runner system includes one nozzle, the nozzle head, temperature controller and so on.
Single-headed hot runner system:
The structure of its injection molds is relatively simple. During the production of TZM alloy, the molten plastic is poured into the nozzle connecting plate from the nozzle to the nozzle head and then injected into the mold cavity. It is necessary to control the sizes (d, D, L) and adjust the thickness of the nozzle connecting plate so that the fixing plate of fixed mold can press the end of the nozzle connecting plate to control the axial displacement. The same purpose can be achieved by directly using the nozzle of the injection machine against the end of the nozzle connecting plate.
Multi-headed hot runner system:
The structure of its injection molds is relatively complicated. During the production of TZM alloy, the molten plastic is poured into the nozzle connecting plate from the nozzle to the nozzle head and then injected into the mold cavity. The nozzles and fixed mold plates have matching requirements for radial dimension D1 and axial dimensional limit requirements. The nozzle head and the fixed mold insert have a matching requirement for radial dimension d to ensure that the molten plastic does not overflow to the non-cavity part, and the hardness of the fixed mold insert is required to be hardened by about 50HRC.
Valve-regulated hot runner system:
Compared with other normal hot runner systems, the plastic mold structure of this system is the most complicated because it has an additional valve needle transmission device which controls the opening and closing movement of the valve needle. The transmission device is equivalent to a hydraulic cylinder, which is connected with the mold by the hydraulic device of the injection machine to form a hydraulic circuit. As a result, it realizes the opening and closing movement of the valve needle and controls the molten plastic injection into the cavity.
- TZM Manufacturer & Supplier, Chinatungsten Online: titanium-zirconium-molybdenum.com
- Tungsten News & Prices of China Tungsten Industry Association: www.ctia.com.cn
- Molybdenum News & Price: news.molybdenum.com.cn
- Tel.: 86 592 5129696; Fax: 86 592 5129797; Email: sales@chinatungsten.com
Czochralski Method and Crystal Growth Furnace
- Details
- Category: Tungsten Information
- Published on Monday, 17 September 2018 19:58

Czochralski method is abbreviated as CZ method. This method is mainly used to pull crystals from the solution. In the crystal growth furnace, molybdenum crucible is mainly used as a carrier. In 1964, this method was first applied to the growth of sapphire single crystals, successfully growing the sapphire crystals with higher quality.
The steps of Czochralski method are listed as below:
1.0 To heat the raw material to the melting point. Owing to difference in temperature, it forms the super-cooling. Therefore, the melt then begins to solidify on the surface of the seed crystal and grow the single crystals which own the same crystal structure with the seed crystal. Meanwhile, the seed crystal is pulled up at a slow speed, and the molten metal gradually solidifies on the solidification interface of the seed crystal, thereby forming an axisym metric single crystal ingot.
By controlling the speed of pulling, it grows the crystal neck, head, body and tail.
2.0 When the crystal neck has been formed, the speed of pulling needs to slow down in order to make the diameter of crystal increase to the needed length. This step is the growth of crystal head.
3.0 When the diameter of crystal increases to the needed length, the pulling speed should be uniform. The diameter of the crystal at this step is fixed. This is the part of crystal body.
4.0 After the growth of crystal body, the crystal ingot should be removed from the molten metal. At this time, the pulling speed begins to accelerate. The diameter of the ingot will decrease until the ingot turns into a point and is separated from the molten metal. This step is the growth of tail. The purpose is to prevent from generating the thermal stress during the quick separation between the ingot and the melt. The thermal stress which is generated during the separation will leads to the defects of the ingot, such as dislocation, slip line and so on.
It is convenient for us to observe the growth of crystal if we adopt CZ method. The crystal grows on the liquid surface without the influence of Mo crucible. In addition, this method can decrease of the stress of crystals and make people use the seed crystal orientation more conveniently. It helps grow crystals with higher quality at a faster rate.
- TZM Manufacturer & Supplier, Chinatungsten Online: titanium-zirconium-molybdenum.com
- Tungsten News & Prices of China Tungsten Industry Association: www.ctia.com.cn
- Molybdenum News & Price: news.molybdenum.com.cn
- Tel.: 86 592 5129696; Fax: 86 592 5129797; Email: sales@chinatungsten.com
Stamping of Mo Crucible
- Details
- Category: Tungsten Information
- Published on Monday, 17 September 2018 19:53
.jpg)
The previous of Mo crucible is made by the turning and processing of the bar. Most of the metals become chips.The utilization of materials is extremely low, and the cost is high.
The adoption of the thick molybdenum plate stamping method makes it possible to produce the Mo crucible of which diameter is 66mm and the height is 48mm. The feasibility of this method is based on the special properties and state of the Mo plate.
This method includes two stamping procedures. Therefore, specially designed molds of which material is P6M5 steel are produced for this method. These molds can be stamped by heating to the operating temperature. The first stamping coefficient is 0.64 and the second one is 0.85. After the first stamping, the external diameter of blanks is 78mm, and the external diameter after the second stamping is 66mm. The radius of the bottom is 25mm and the radius of the side wall is 20 mm.
In order to relax the stress inf the Mo blank, it is important to select the effective lubricant material. After trying out the graphite as the material of lubricant, we found that it is most effective when the heating is not more than 500 °C. The problem is that it is difficult to clean the parts after the stamping.
The solution to this problem is that we can use the glycerol as the lubricant at the first stamping and use colloidal graphite at the second stamping. It can not only solve the problem of cleaning, but also obtain the Mo crucible without cracks.
When we produce the crucible, the thick molybdenum plate stamping method is adopted which can reduce the scrap loss of Mo by two-thirds of the scrap loss caused by the cutting. As a result, it improves the utilization of the material. With the development of the technology, we have produced the Mo crucible of which diameter is 84mm and the height is 65mm by this stamping method.
- TZM Manufacturer & Supplier, Chinatungsten Online: titanium-zirconium-molybdenum.com
- Tungsten News & Prices of China Tungsten Industry Association: www.ctia.com.cn
- Molybdenum News & Price: news.molybdenum.com.cn
- Tel.: 86 592 5129696; Fax: 86 592 5129797; Email: sales@chinatungsten.com
Design Procedure of TZM Hot Runner Nozzle
- Details
- Category: Tungsten Information
- Published on Monday, 17 September 2018 18:49

TZM (Titanium-Zirconium-Molybdenum Alloy) hot runner system generally includes nozzle, manifold, thermal chamber, accessories and so on. There are two kinds of nozzle: open hazzle and valve nozzle. The design procedure of TZM hot runner nozzle includes eight following steps:
1.0 The position of feed inlet is determined according to the plastic part structure and operation requirements. The feed inlet can be placed at every position of the plastic part if the structure of the plastic part allows and the nozzle and nozzle head in the fixed insert are not intervened by the structure.
2.0 To determine the form of nozzle in the hot runner system. The key factors of selecting nozzle form are the materials of plastic parts and the operation properties of products. The batches of plastic parts production and the production cost of molds are the important factor of selecting the nozzle form.
3.0 To determine the cavity of plastic part according to the production batches and the tonnage of the injection devices.
4.0 To decide the number of nozzles according to the determined position of feel inlet and the cavity of the mold.
5.0 The radial size of nozzle depends on the weight of mold and the number of nozzles.
6.0 The size of mold structure can be determined by the structure of plastic parts. An then the size of standard nozzle should be selected according to the fixed insert and the thickness of fixed template.
7.0 hot manifold retaining plate
The shape of the hot retaining plate is determined according to the shape of the hot manifold. The lead groove is arranged on the plate, and a sufficient cooling water loop is designed near the hot runner plate, the nozzle, and the nozzle head.
8.0 To complete the design of the plastic molds of the hot runner system.
The finished TZM hot runner nozzle system must consider the degree of cooperation between the hot runner system and the plastic mold, that is the design of the hot half.
- TZM Manufacturer & Supplier, Chinatungsten Online: titanium-zirconium-molybdenum.com
- Tungsten News & Prices of China Tungsten Industry Association: www.ctia.com.cn
- Molybdenum News & Price: news.molybdenum.com.cn
- Tel.: 86 592 5129696; Fax: 86 592 5129797; Email: sales@chinatungsten.com
Tungsten Carbide Cobalt Chromium Spraying for Valves of Petroleum Pipeline
- Details
- Category: Tungsten Information
- Published on Sunday, 16 September 2018 00:07
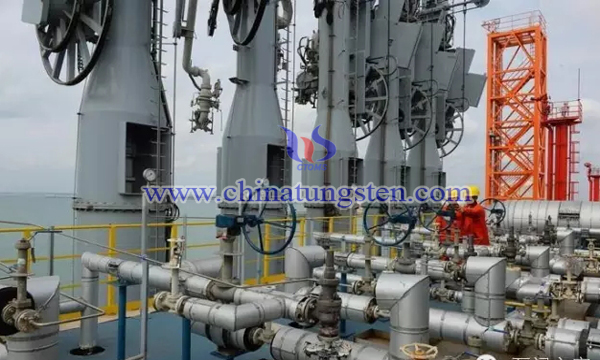
As a wear-resistant and corrosion-resistant coating, thermal sprayed WC-Co-Cr coating has been widely used in aerospace, metallurgy, machinery and other fields because of its high hardness and good toughness.
High Purity Tungsten Powder Hydrogen Reduction Details
- Details
- Category: Tungsten Information
- Published on Saturday, 15 September 2018 23:57
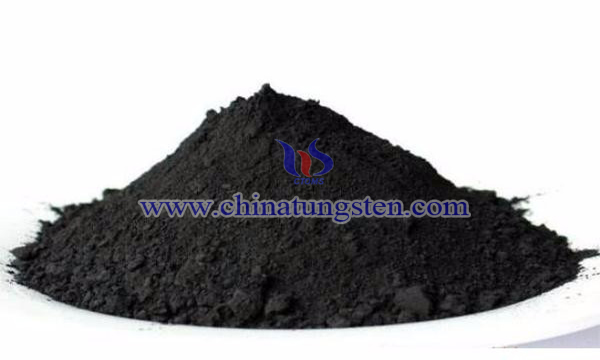
High purity tungsten above 5N has high resistance to electron migration, high-temperature stability and the formation of stable silicides. It is widely used in gate circuit electrode materials of large-scale integrated circuits. At present, there are two key points in the preparation of high purity tungsten powder by hydrogen reduction method: one is the improvement of smelting and purification technology, and the purity of raw materials meets the requirements of corresponding purity; the other is the cleanliness of the preparation process of tungsten powder, so as to reduce the pollution of impurities in the production process.
Strategy for Separation and Recycle of Silver Tungsten Waste
- Details
- Category: Tungsten Information
- Published on Saturday, 15 September 2018 23:43
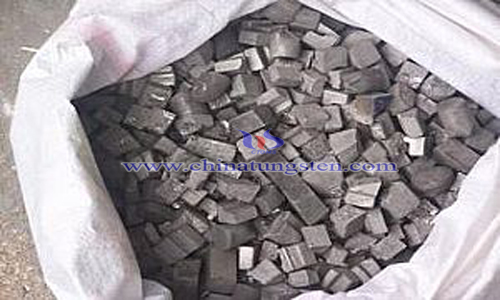
Silver-tungsten materials are generally used in low-voltage plastic case circuit breakers, universal circuit breakers and protective switches, as moving contacts. Silver-tungsten materials are usually fabricated by infiltration process in powder metallurgy, such as the steps of making AgW50 materials: (1) silver and tungsten powder are mixed into AgW70 powder according to 3:7; (2) pressing AgW70 porous skeleton; (3) adding silver plate to obtain dense AgW50 materials by high temperature infiltration, and the silver content of waste materials produced in the production process is generally between 20-50%. Separation and recycling are needed.