Welding Tungsten Boat
- Details
- Category: Tungsten Information
- Published on Thursday, 12 May 2016 10:43
- Written by xuejiao
- Hits: 287
Welding tungsten boat is also known as heating wolfram boat. Welding is connected directly to connecting position of the two metals together by the melting at high temperature. Heating and pressing five pieces of tungsten plates at a high temperature so that the connection can be melted together, cooling it after welding, forming the final shape of the boat. Welding of pure wolfram is generally divided into two processes: melting welding and brazing. During the melting welding, molten liquid of two workpieces will mix together under interaction of temperature field and gravity but without any pressure. Until the temperature decreases, the melted portion will condense, two workpieces will be firmly welded together to complete the welding. Brazing use metal material which has a lower melting point than the base material as the brazing filler metal, Heating the weldment and brazing filler metal to make its melting point higher than the melting point of brazing filler metal and lower than the melting temperature of the base material, using liquid brazing filler metal to wet the base metal, filling gap of joint and connect the base material. While welding, the joint of the wolfram plates is called soldering seam. Both sides of it would influenced by heating during soldering and organization and performance would change, this area is known as the heat affected zone.
Soldering is a fabrication or sculptural process that joins materials, usually metals or thermoplastics, by causing fusion, which is distinct from lower temperature metal-joining techniques such as brazing and soldering, which do not melt the base metal. In order to improve the quality of soldering wolfram boat, users can use argon, carbon dioxide and other gases to avoid atmosphere so that it can protect the arc and rate of furnace hearth while welding. Finally, a boat shape is formed by welding.
Its size is relatively large, so it can be used for large-scale evaporation device or a large number of material evaporation. Compared to riveting tungsten boat, soldering W-boat can save material of 10% -20%, and it doesn’t need to scribing, drilling, assembling, and other complex processes. Since welding tungsten boat is made of two or more plates, which cannot be made on one time, so the preparation time will be longer.
Tungsten Metals Supplier: Chinatungsten Online www.tungsten.com.cn | Tel.: 86 592 5129696; Fax: 86 592 5129797;Email:sales@chinatungsten.com |
Tungsten News & Prices, 3G Version: http://3g.chinatungsten.com | Molybdenum News & Molybdenum Price: http://news.molybdenum.com.cn |
Sintering Tungsten Boat
- Details
- Category: Tungsten Information
- Published on Thursday, 12 May 2016 10:40
- Written by xuejiao
- Hits: 245
Sintering wolfram boat is to firing anhydrous wolframic acid to produce tungsten powder, which is an important carrier for making it. Or loading ammonium paratungstate (APT) in firing W-boat to make wolfram powder, the APT is white crystal, which include schistose and acicular, it is applied in the manufacturing process of tungsten metal powder by anhydrous wolframic acid or blue tungsten oxide.
Sintering tungsten boat is mainly used in the production of tungsten powder. Burning ammonium paratungstate into yellow tungsten oxide or blue tungsten oxide, and then make wolfram powder in hydrogen. During the manufacturing process, tungsten oxide should be placed in a W-boat and then put in the reduction furnace. After recycling the hydrogen, remove the carrier. Fritting is divided into three stages, namely the low temperature burn-in step, the medium temperature firing step and keeping warm in a high temperature. In the low-temperature burn-in step is mainly to volatilize the gas and moisture content which is adsorbed in wolfram boat. Anhydrous wolframic acid is a raw material of wolfram powder.
Process for preparing tungsten powder can be divided into two stages. The first procedure is that the anhydrous wolframic acid is reduced to tungsten dioxide at a temperature of 500 ℃ -700 ℃. The second procedure is that tungsten dioxide is reverted to the wolfram powder under the temperature of 700 ℃ -900 ℃. Purity, particle size, size distribution and other properties of the reduction of W-powder, which primarily rely on the reduction process. When you restore a wolfram powder in a tube furnace, temperature of reduction, charging capacity of tungsten oxide of W-boat, moving speed of W-boat, the flow rate of hydrogen and moisture content of hydrogen content are the main factors to influence the speed of reduction. Particle size of wolfram powder will become thicken as the temperature rises.
While firing, sintering tungsten boat can remove a portion of the harmful impurities, such as sulfur, potassium, sodium and others. This type of W-boat reduces the adverse effects of harmful ingredients (water, oxygen, nitrogen) of the product under vacuum fritting. It is in favor of eliminating the adsorbed gas and the residual gas of the pores which can promote post- fritting shrinkage. However, due to the high temperature, fritting stove would emit large amounts of waste heat.
Tungsten Metals Supplier: Chinatungsten Online www.tungsten.com.cn | Tel.: 86 592 5129696; Fax: 86 592 5129797;Email:sales@chinatungsten.com |
Tungsten News & Prices, 3G Version: http://3g.chinatungsten.com | Molybdenum News & Molybdenum Price: http://news.molybdenum.com.cn |
WO3 Hydrodesulfurization Catalyst - Regeneration Flue Gas Treatment 2/2
- Details
- Category: Tungsten Information
- Published on Wednesday, 11 May 2016 18:05
- Written by chunyan
- Hits: 240
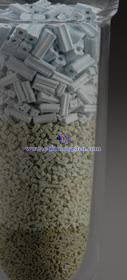
Tungsten Oxide Supplier: Chinatungsten Online www.tungsten-oxide.com | Tel.: 86 592 5129696; Fax: 86 592 5129797;Email:sales@chinatungsten.com |
Tungsten News & Prices, 3G Version: http://3g.chinatungsten.com | Molybdenum News & Molybdenum Price: http://news.molybdenum.com.cn |
Tungsten Alloy Shielding Used For Radiation Technology
- Details
- Category: Tungsten Information
- Published on Wednesday, 11 May 2016 18:08
- Written by minghui
- Hits: 264
With the development and application of nuclear technology, radiation technology shows great potential in the medical, radiation processing, power generation, food security, industrial testing and other aspects. Radiation technology is a subject that is closely linked to the fields of high polymer materials, environmental science, biotechnology and medicine. It main uses radiation (such as gamma rays, X-rays, neutrons, etc.) emitted by radiation source to interact with matter to produce activated atoms and activated molecules which will react with matter both in both in physically and chemically, thereby improving the quality and performance of materials or leading to the degradation, polymerization and crosslinking modification of substances and preparation of new substances. The characteristics of radiation technology include high added value, low energy consumption and wide application, radiation technology is widely used in the modification of semiconductor and polymer, food preservation, and radiation sterilization of medical supplies and the like. Radiation technology can be categorized as radiation crosslinking, radiation curing, radiation vulcanization, radiation degradation, radiation grafted.
Radiation technology has brought radiological hazards while bringing the great facility to people. The largest long-term health risk of radiation is cancer. Radiation can destroy the mechanism in vivo which can prevent cancer, so that greatly increases the risk of cancer. Radiation can also enter the body through a variety of ways, causing internal radiation damage, leading to fatigue, dizziness, insomnia, skin redness, ulceration, bleeding, hair loss, leukemia, vomiting, diarrhea and other symptoms. In addition, radiation will increase aberration rate and hereditary disease incidence, to affect the health of future generations. Exposure to radiation will lead to genetic changes, once the DNA in reproductive cells are damaged, the new generation will inherit the altered gene of mother, thus increasing the risks of defects in the offspring. It is understood that the fetal embryos and fetuses are more sensitive to radiation, exposure to radiation before embryo implantation can increase the late fetal mortality rate; while in the case of exposure to radiation during organogenesis, the increased rates are elevated rate of fetal malformations and neonatal mortality.
Tungsten alloy shielding is widely used to absorb and shield radiation generated by the use of radiation technology. Experts have found that the radiation shielding capability of a material is closely related to its density, higher density means better shielding capability to shield and absorb the radiation. Since the tungsten alloy has a higher density compared with other radiation shielding materials (such as lead), tungsten alloy shielding exhibits better radiation shielding capability. Tungsten alloy shielding has high density also means that under the same shielding ability, tungsten alloy shielding is smaller and thinner.
Tungsten Alloy Supplier: Chinatungsten Online www.tungsten-alloy.com | Tel.: 86 592 5129696; Fax: 86 592 5129797;Email:sales@chinatungsten.com |
Tungsten News & Prices, 3G Version: http://3g.chinatungsten.com | Molybdenum News & Molybdenum Price: http://news.molybdenum.com.cn |
WO3 Hydrodesulfurization Catalyst - Regeneration Flue Gas Treatment 1/2
- Details
- Category: Tungsten Information
- Published on Wednesday, 11 May 2016 18:02
- Written by chunyan
- Hits: 214
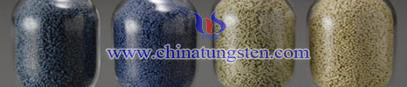
Tungsten Oxide Supplier: Chinatungsten Online www.tungsten-oxide.com | Tel.: 86 592 5129696; Fax: 86 592 5129797;Email:sales@chinatungsten.com |
Tungsten News & Prices, 3G Version: http://3g.chinatungsten.com | Molybdenum News & Molybdenum Price: http://news.molybdenum.com.cn |