Tungsten Copper Wire Process
- Details
- Category: Tungsten Information
- Published on Thursday, 19 May 2016 16:48
- Written by xiaobin
- Hits: 264
The basic process of tungsten copper wires is : Mixing → molding or isostatic pressing → infiltration, sintering tungsten copper rod or tungsten copper block → machining. Except conventional infiltration process, there are some popular processes used more, such as high-temperature liquid phase sintering and activated liquid-phase sintering. The principle of infiltration is that porous tungsten skeleton wetted by copper liquid, under the capillary force the copper liquid flows along the W particle gap, filling the pores of porous tungsten skeleton. So tungsten copper materials have higher density, excellent sintering properties and electrical conductivity; High temperature liquid phase sintering since the sintering temperature is high, a long time, will make a lot of volatile copper phase, so that the sintered tungsten copper material density decrease, the performance will be subject to different degrees of impact, it is difficult to obtain a high density, high conductivity tungsten copper alloy material; activated liquid phase sintering improves the relative density, the hardness and tensile strength of tungsten copper by adding small amounts of trace elements (Ni, Fe, Pd, etc.). But on the contrary, the activated elements will dramatically decrease the electrical and thermal conductivity, which is not suitable for the occasions with high requirements of the conductivity.
The technologies to machine tungsten copper rod or block in wires include drawing processing, rolling processing, roller die drawing techniques and rotary forging technology. Drawing processing take advantage of metal plasticity, when working in the external force so that it is forced through the die, the metal cross-sectional area is compressed to obtain the desired cross-sectional shape and size of the processing method. Preparation of tungsten and copper wire by repeatedly hammering and drawing forming, drawing conducted at room temperature, metal products will produce obvious hardening.
But for tungsten copper with lower Cu content, it has poor plasticity, the drawing rate received extremely limited, which is difficult to draw molding; rolling process is to rely on the friction two rotating rollers and the rolling member rolling pulled into the roll gap, it is compressed to produce plastic deformation process. In addition, the rolling process can also refine the grain, improve the organization, can significantly improve the mechanical properties of the metal alloy, suitable for mass production; Roller die drawing process the billet is drawn in a non-grooved drive, freely rotating rollers consisting of, the sliding friction with the material of the die orifice was changed to rolling friction bearing, the stretching process is more effort not only suitable for drawing round wire, shaped wire may be stretched, but not suitable for low plastic material.
Tungsten Copper Supplier: Chinatungsten Online tungsten-copper.com | Tel.: 86 592 5129696; Fax: 86 592 5129797;Email:sales@chinatungsten.com |
Tungsten News & Prices, 3G Version: http://3g.chinatungsten.com | Molybdenum News & Molybdenum Price: http://news.molybdenum.com.cn |
Tungsten Copper Wire Description
- Details
- Category: Tungsten Information
- Published on Thursday, 19 May 2016 16:46
- Written by xiaobin
- Hits: 282
Tungsten copper alloy is a kind of psudoalloy, which consists of the hard phase W and the binder phase Cu two immiscible metals, so it only can be fabricated by PM (Powder Metallurgy). Tungsten copper material has both advantages of tungsten and copper, the high density, high melting point, excellent wear resistance and corrosion resistance of W; the excellent electrical and thermal conductivity, good plasticity of Cu; and at a temperature above the melting point of copper alloy of copper liquefied evaporated to absorb a lot of heat, reducing the surface temperature. So tungsten copper material is also known as heat sink materials.
According to the shapes and applications, tungsten copper products can be specifically divided into tungsten copper rod, tungsten copper block, tungsten copper plate, tungsten copper contact, tungsten copper tube, tungsten copper electrode, tungsten copper heat sink, tungsten copper wire and so on. In the early 1960s, tungsten copper wire and tungsten copper electrode has been used in EDM (Electrical Discharge Machining) and resistance welding because of its high density, high strength, excellent electrical and thermal conductivity and arc ablation resistance. So far, with the developments of relevant technologies and further study of researchers, tungsten copper begin to use in plasma electrode material processing, precision machining, spraying, LED and other electrode fields. But since the special PM structure of tungsten copper, it has been greatly limited used in wire. In order to improve the uniformity, mechanical properties and production cost, it needs to looking for new technologies and processes.
Used in EDM electrodes of tungsten copper wires are supposed to meet the following requirements:
1. On the basis of excellent electrical and thermal conductivity, it also has good resistance to spark erosion;
2. Good structure uniformity and density, in order to ensure the stability of the electrical processing and improve the utilization of electrode material;
3. It has lower machining consumption and dose not affects the quality and the overall efficiency;
4. Easy for molding, machining molds and products according to design requirements to provide a correspondingly shaped profile tungsten copper electrode bars or complex shapes.
Tungsten Copper Supplier: Chinatungsten Online tungsten-copper.com | Tel.: 86 592 5129696; Fax: 86 592 5129797;Email:sales@chinatungsten.com |
Tungsten News & Prices, 3G Version: http://3g.chinatungsten.com | Molybdenum News & Molybdenum Price: http://news.molybdenum.com.cn |
Titanium Based Tungsten Trioxide Denitration Catalyst
- Details
- Category: Tungsten Information
- Published on Thursday, 19 May 2016 16:07
- Written by chunyan
- Hits: 232
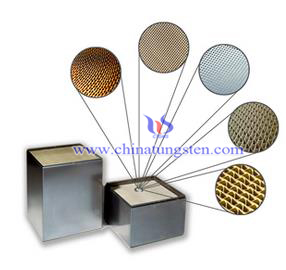
Tungsten Oxide Supplier: Chinatungsten Online www.tungsten-oxide.com | Tel.: 86 592 5129696; Fax: 86 592 5129797;Email:sales@chinatungsten.com |
Tungsten News & Prices, 3G Version: http://3g.chinatungsten.com | Molybdenum News & Molybdenum Price: http://news.molybdenum.com.cn |
Tungsten Trioxide Contained Vehicle Denitration Catalyst without Vanadium
- Details
- Category: Tungsten Information
- Published on Thursday, 19 May 2016 16:09
- Written by chunyan
- Hits: 236
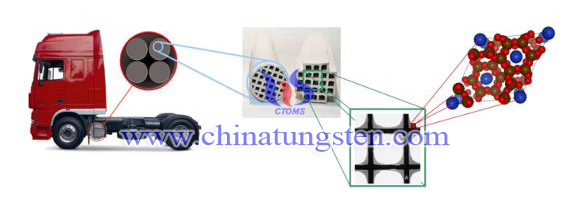
However, when SCR catalyst containing vanadium used for cleaning motor vehicle exhaust, it may lead to toxic vanadium compound going into the air because of the volatility of vanadium under high temperature, thus to cause environmental pollution and personal injury. So, the listed capacity of the car catalyst containing vanadium is low. Therefore, for a long time, researchers and vendors are ongoing committed to provide no vanadium SCR denitration catalyst.
Tungsten Oxide Supplier: Chinatungsten Online www.tungsten-oxide.com | Tel.: 86 592 5129696; Fax: 86 592 5129797;Email:sales@chinatungsten.com |
Tungsten News & Prices, 3G Version: http://3g.chinatungsten.com | Molybdenum News & Molybdenum Price: http://news.molybdenum.com.cn |
Testing Standards of Carbon Sulfur Analyzer and Tungsten Granule——Test Conditions and Test Methods
- Details
- Category: Tungsten Information
- Published on Thursday, 19 May 2016 10:47
- Written by xuejiao
- Hits: 248
Except the technical requirements, testing standards of carbon sulfur analyzer and tungsten granule also include - test conditions, test methods, management of the results of treatment, re-testing period. The relative standard deviation of carbon is lower than 1.0%, sulfur should be lower than 4.0%, the analysis time should less than one minute, the weighing stability of less than 0.002 grams. Environment conditions for testing should meet the standards. The ambient temperature should be controlled between 15 ℃ to 30 ℃, relative humidity must be less than 80%. If it is measured against the amount of 0.0010% to 0.0100% of the carbon and sulfur, the relative humidity should be less than 60%. Power supply is (220 ± 4.4) V, (50 ± 1) Hz, and it should be ensured that the detection environment has no strong vibration, no strong electric, no active gases and without any impede of magnetic fields.
The main test equipments and materials for detection should be in accordance with national standards. Using the approved the steel components by the state metrological administrative department to analyze national primary, secondary reference material. Uncertainty of the determination of carbon and sulfur less than one-third of error of indication, weighing with 1g standard weights. According to visual indication and touch to detect the appearance of instrument. The instrument is required to be preheated on the basis of instructions before detecting. Select carbon content within the range from 0.100% 1.000%, and choose sulfur content within the range from the 0.010% to 0.100%, weighing 0.5 g of sample every time, repeated detecting for 7 times, calculating the standard deviation and relative standard deviation in according with the standard formula calculation method . Weighing with 1 g standard weight, continuously weighing for six times, the difference between the maximum and the minimum is called weighing stability. After the test is completed, certificate of qualification can be sent, if unqualified, pointing out that the failed project. Test cycle usually two years. While moving, repairing or doubting on the measurement results, users can test the instrument.
If the carbon sulfur analyzer used by the company are not included in the mandatory verification of measuring instruments catalog, on the other hand, these instrument are not applied in trade settlement, safety, health, environmental monitoring, there is no need to test it compulsively.
Tungsten Metals Supplier: Chinatungsten Online www.tungsten.com.cn | Tel.: 86 592 5129696; Fax: 86 592 5129797;Email:sales@chinatungsten.com |
Tungsten News & Prices, 3G Version: http://3g.chinatungsten.com | Molybdenum News & Molybdenum Price: http://news.molybdenum.com.cn |