Low-temperature Sintering Tungsten-nickel-antimony Heavy Alloy
- Details
- Category: Tungsten Information
- Published on Thursday, 01 September 2022 09:55
Tungsten heavy alloys (WHA) are two-phase alloys that contain various compositions, microstructures, and performance tradeoffs. These alloys typically contain 88-97% by weight tungsten grains and nickel-iron, nickel-manganese, nickel-copper, and nickel-cobalt matrices. Due to their high density of 17 to 19 g/cm3, these alloys are frequently used in inertial applications including golf club weights, self- winding watch weights, aircraft wing weights, cellular telephone vibrators, munitions, and oilfield rejuvenation projectiles. Other applications include X-ray and radiation shields, and plasma and nuclear protection devices.
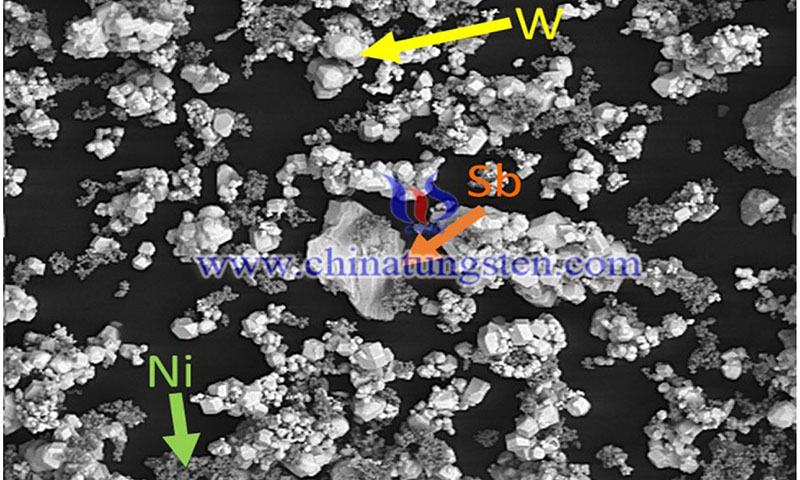
(Picture source: Pahlevani, A / International Journal of Refractory Metals and Hard Materials)
Heavy tungsten alloys are usually made by liquid phase sintering (LPS). However, extremely high sintering temperatures are required because tungsten has a very high melting point of 3422 °C. The sintering temperature depends on the tungsten content in the mixture and is between 1500 and 1530 °C. In order to manufacture high-density tungsten alloys at low temperatures, a lot of research has been done. Lowering the melting temperature of the matrix may be a feasible strategy to achieve this goal. Nickel (Ni) and antimony (Sb) exhibit a eutectic phase at 1098 °C. Given the eutectic temperature and slow reaction of nickel/antimony, this alloy can be used as a matrix phase for low sintering temperature tungsten alloys. The production process of the first production of tungsten-nickel-antimony alloy with low-temperature sintering is as follows.
Tungsten-nickel-antimony alloys were prepared using 99.9% pure W, Ni and Sb elemental powders. Design quantities of powder were weighed according to their chemical composition of 90W-7.6Ni-2.4Sb, 90W-6.8Ni-3.2Sb, and 90W-6Ni-4Sb. Then they were mixed accordingly with tungsten carbide balls for 60 min at 100 rpm in a high-energy planetary mill. Ball to powder ratio (BPR) is 10:1. The weighed powder was then poured into a cylindrical polymer mold with an inner diameter of 16.5 mm and a height of 173 mm. Next, the mold containing the powder was compacted by cold isostatic pressing at 300 MPa for 60 s. The compacted samples were then kept at 900 °C for 45 min in a pure hydrogen atmosphere to reduce oxides. The heating rate to reach the sintering temperature was 10°C/min. The samples were then sintered at 1,100, 1,200, 1,300 and 1,400 °C for 60 minutes according to the sintering cycle. They were then cooled to room temperature at 5 °C/min.
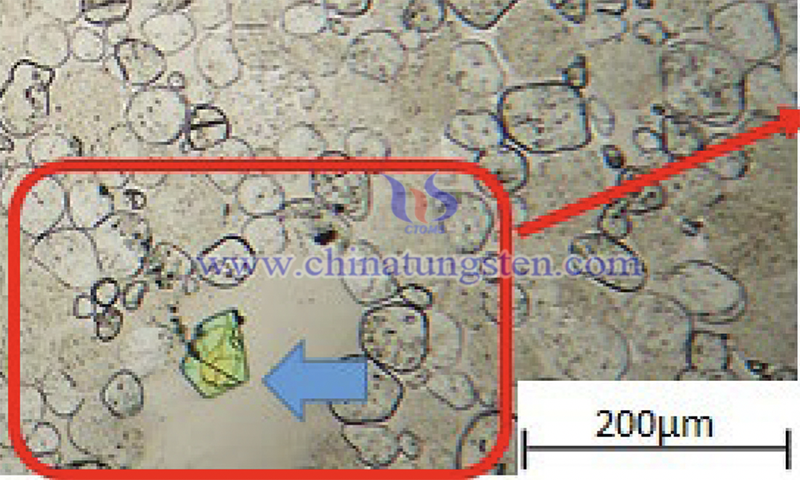
(Picture source: Pahlevani, A / International Journal of Refractory Metals and Hard Materials)
In summary, tungsten-nickel-antimony alloy was successfully produced in a relatively low-sintering temperature ranged from 1200 - 1300°C. The relative densities of the alloys are above 99%. The 90 W-6.8Ni-3.2Sb alloy was sintered at 1300 °C to reach the maximum relative density (99.51%). The particle size of tungsten in this alloy is approximately 27.8 µm. With the increase of antimony content, the particle size and relative density of tungsten first increased and then decreased. The density, hardness and compressive yield strength of the W-Ni-Sb alloy are comparable to those of the conventional W-Ni-Fe alloy, while the sintering temperature is lower.
Article Source: Pahlevani, A., Semnani, H. M., & Abdoos, H. New low-temperature sintering tungsten-nickel-antimony alloy: Microstructure evolution and mechanical properties. International Journal of Refractory Metals and Hard Materials, 108 (2022).
- Tungsten Alloy Manufacturer & Supplier, Chinatungsten Online: www.tungsten-alloy.com
- Tungsten News & Prices of China Tungsten Industry Association: www.ctia.com.cn
- Molybdenum News & Price: news.molybdenum.com.cn
- Tel.: 86 592 5129696; Fax: 86 592 5129797; Email: sales@chinatungsten.com