Effect of Heating Rate on Sintering Shrinkage
- Details
- Category: Tungsten Information
- Published on Sunday, 25 February 2018 18:17
Sintering shrinkage of tungsten carbide is a very prominent change during the sintering process. As the amount of shrinkage is directly related to the properties of the alloy, size and other key indicators, it is necessary to strictly control the amount of shrinkage. The shrinkage of tungsten carbide is mainly in the two processes of solid phase sintering and liquid phase sintering.
Heating rate will have a significant effect on the sinter shrinkage of the tungsten carbide.
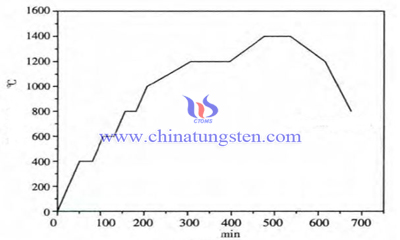
Stage of Sintering Shrinkage
According to the sintering theory, the shrinkage of tungsten carbide is mainly in the two processes of solid phase sintering and liquid phase sintering. And the contraction can be divided into three stages. The first phase mainly occurs in the solid phase sintering process, which is mainly caused by the surface diffusion and volume diffusion between solid particles. The second phase mainly occurs when the eutectic temperature is near, and the contraction is mainly caused by the formation of liquid phase and the mechanism of particle rearrangement.
Because the sintering temperature is close to the eutectic temperature, the plastic flow, the rearrangement of the particles and the sharp contraction of the volume of the body will occur. After the emergence of the liquid phase, the third stage is mainly caused by the mechanism of dissolving and re precipitation.
At the normal heating rate (several degrees per minute), the shrinkage process of the sintered body produces normal contraction according to the three contraction stages mentioned above. However, if the heating rate is too fast, the maximum contraction velocity will move to a higher temperature range and even move to the sintering body to produce the liquid phase temperature.
Excessive sintering speed leads to insufficient diffusion process in the first stage. Vacancy diffuses from the inner pore to the surface of the particle and the vacancy diffuses from the small pore to the large pore. Excess vacancy on the edge of the cervix is not enough to spread to the grain boundary. The result is that the spacing of the particles is shortened and the amount of the contraction is small.
High sintering speed causes the second stage of the gas hole to be too late to discharge, because the discharge channel of the gas is closed after the liquid phase appears in advance. The high sintering speed makes the chemical difference in different regions (saturation concentration difference) decreased rapidly, dissolution reprecipitation process lack of driving force, resulting in dissolution reprecipitation process is not sufficient, which hinders the spheroidization of particles - Dense - rearrangement process, shrinkage affected. In summary, the excessive heating rate is unfavorable to a fully dense tungsten carbide sintering body.
- Tungsten Carbide Manufacturer & Supplier, Chinatungsten Online: tungsten-carbide.com.cn
- Tungsten News & Prices of China Tungsten Industry Association: www.ctia.com.cn
- Molybdenum News & Price: news.molybdenum.com.cn
- Tel.: 86 592 5129696; Fax: 86 592 5129797; Email: sales@chinatungsten.com