Sintering of Tungsten Carbide
- Details
- Category: Tungsten Information
- Published on Friday, 09 February 2018 18:46
Sintering is the last process of tungsten carbide production process, which is also the most basic and the most critical process. After sintering, the porous powder compacts turn into products with certain organization and performance. The sintering of tungsten carbide belongs to the powder metallurgy sintering process.
Definition of Sintering
The powder compacts are heated to a certain temperature (sintering temperature) and to maintain a certain time, then cool down, to obtain the required properties of materials, this process is called sintering. In the process of sintering, the bonding between particles is realized by heating by means of atomic migration. When the particles are bonded, the strength of the sintered body increases, and in most cases the density increases.
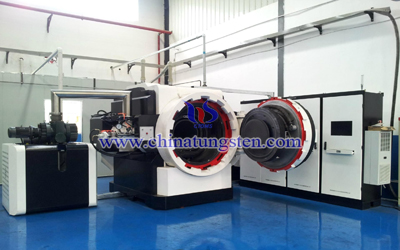
If the sintering conditions are properly controlled, the density of the sintered body and other physical and mechanical properties can be close to or reach the compact material of the same composition. The purpose of sintering is to make the porous powder block into an alloy with a certain structure and properties.
Sintering is often regarded as a heat treatment, i.e., heating the powder or powder blank to a temperature below the melting point of the main components, and then cooling it to room temperature. During this process, there are a series of physical and chemical changes. The aggregates of powder particles become the coalescence of grains, thus obtaining products or materials with physical and mechanical properties.
Tungsten carbide is made up of a variety of carbides and iron elements, such as WC-Co, WC-TiC-TaC-NbC-Co, or TiC-Mo2C-Ni. The typical characteristic of these materials is that it can reach almost 100% theoretical density by liquid phase sintering. After sintering, low residual porosity is the key to successful application of tungsten carbide in metal cutting, oil drilling bit or metal forming die and other high stress working conditions.
- Tungsten Carbide Manufacturer & Supplier, Chinatungsten Online: tungsten-carbide.com.cn
- Tungsten News & Prices of China Tungsten Industry Association: www.ctia.com.cn
- Molybdenum News & Price: news.molybdenum.com.cn
- Tel.: 86 592 5129696; Fax: 86 592 5129797; Email: sales@chinatungsten.com