Sintering Process of Tungsten Carbide
- Details
- Category: Tungsten Information
- Published on Friday, 09 February 2018 18:54
The sintering process of tungsten carbide can be divided into four basic stages according to the order of sintering: removal of forming agent and burn-in stage, solid phase sintering stage, liquid phase sintering stage and cooling stage.
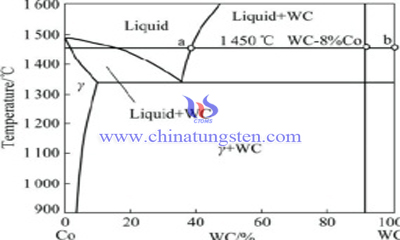
1, Removal of Forming Agent and Burn-In Stage
1.1, The moisture, gas, and residual solvents (residual alcohol in the spray process) absorbed by powder or molding agent in the block are volatilized by the rise of temperature.
1.2, With the increase of temperature, gradually forming agent decomposition or vaporization. The forming agent will increase the carbon content of sintered body, which changes with the variety, quantity and forming agent of different sintering process.
1.3, At the sintering temperature, the hydrogen reduction of cobalt and tungsten oxide if the vacuum debinding and sintering, carbon oxygen reaction is not strong.
1.4, The powder contact stress gradually eliminates, with the increase of temperature and annealing.
1.5, The bonding metal powder begins recovery and recrystallization. As the surface diffusion occurs, compressive strength increased. The block size has a weak contraction, which can be used as plasticizer blank machining processing.
2, Solid State Sintering Stage (800℃-- Eutectic Temperature)
At the temperature before the liquid phase, besides the continuation of the previous stage, the solid reaction and diffusion increased, and the plastic flow increased, and the sintered body contracted obviously.
3, Liquid Sintering Stage (Eutectic Temperature-- Sintering Temperature)
When the sintered body appears liquid phase, the shrinkage is completed quickly. Then the crystalline transition is produced to form the basic structure and structure of the alloy. When the eutectic temperature is reached, the solubility of WC in Co can reach about 10%. Powder particles are closed to each other because of the surface tension of liquid phase, and the pores in the particles are gradually filled with liquid phase. The density of the block increases significantly, and the slab contraction and strength increase.
4, Cooling Stage (Sintering Temperature-- Room Temperature)
As the temperature drops, the liquid phase is solidified. And the shape of the alloy is fixed, forming the final microstructure of the alloy. During this stage, the microstructure and phase composition of the alloy vary with the cooling conditions. This characteristic can be used to heat the cemented carbide in order to improve its physical and mechanical properties.
- Tungsten Carbide Manufacturer & Supplier, Chinatungsten Online: tungsten-carbide.com.cn
- Tungsten News & Prices of China Tungsten Industry Association: www.ctia.com.cn
- Molybdenum News & Price: news.molybdenum.com.cn
- Tel.: 86 592 5129696; Fax: 86 592 5129797; Email: sales@chinatungsten.com