Influence Factor of Slip Forming
- Details
- Category: Tungsten Information
- Published on Sunday, 26 November 2017 23:22
Powder sedimentation rate, water absorption rate, cast slurry viscosity and stability during slurry forming process are the most important factors which directly affect the quality of the casting. These parameters depend on the solid-liquid ratio, powder slurry pH, adding dispersant, adsorption gas powder etc. It is necessary to strictly control these factors in grouting process to ensure grouting quality.
1, Powder Size
The faster the powder is awarded, the shorter the whole grouting cycle, so the smaller the settling velocity of the powder. Settling velocity of the powder in the suspension can be determined by the Stokes formula, as shown in the following formula. It can be seen from the formula that the settling velocity of powder in liquid is inversely proportional to the square of particle radius, and the fine particle powder is beneficial to shorten the grouting time.
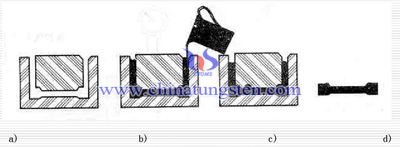
v=KR2(ρp-ρr)g/η(1)
Where:
v- Settling velocity of powder
K- Settlement coefficient
R- Powder particle radius
η- Liquid viscosity
ρp- Powder density
ρr- Slurry density
g- Gravitational acceleration
2, Liquid-Solid Ratio
Liquid-Solid ratio refers to the mass ratio of mother liquor to powder, which mainly affects the speed of settling slurry viscosity of powder. The smaller liquid-solid ratio is, the greater the viscosity of slurry is and the smaller powder sedimentation rate is.
3, pH Value of Slurry
The pH value of slurry affects the viscosity value and the settling velocity of powder particles. And the batter good fluidity can prevent the powder particle aggregation and particle agglomeration, sinking speed is small. These properties for preparing slurry with complex shape, the basal area of small parts is very important.
4, Gas
In the preparation of slurry, a layer of liquid gas prevents the surface of the powder particles adsorbed on the surface wetting. Pouring may cause uneven distribution of bubbles and particles, resulting in the quality reduction of fired billets. Therefore, in addition to slurry gas is an important process in casting process. Usually, there are three ways to remove gas, which are static gas removal, chemical degassing and vacuum degassing.
Static degassing is by mixing the slurry standing for a certain period of time to air due to density difference and continue to escape. Chemical degassing is the addition of degassing agent in mother liquor to promote the removal of gas on the surface of adsorbed powder, such as adding 0.5% octanol to the mother liquor to remove gas. Vacuum degassing method is placed within the vacuum system of slurry, slurry and gas diffusion in this method, the degassing effect is best.
- Tungsten Carbide Manufacturer & Supplier, Chinatungsten Online: tungsten-carbide.com.cn
- Tungsten News & Prices of China Tungsten Industry Association: www.ctia.com.cn
- Molybdenum News & Price: news.molybdenum.com.cn
- Tel.: 86 592 5129696; Fax: 86 592 5129797; Email: sales@chinatungsten.com