Machining Disadvantage
- Details
- Category: Tungsten Information
- Published on Sunday, 26 November 2017 23:25
Tungsten carbide is a typical powder metallurgy product, which has a series of excellent properties. However, after sintering, the alloy has high hardness, brittleness, poor conductivity and difficulty in subsequent processing, which limits its application and development to a certain extent. Machining disadvantages of tungsten carbide machining are mainly as follows: strain sensitive processing, porosity and hard particles.
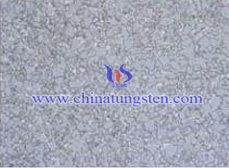
1, Strain Sensitive Processing
Most of the tungsten carbides cannot be formed at once to meet the requirements of the net shape, accuracy and surface roughness of the required parts, and the subsequent processing is often needed. And tungsten carbides are usually sensitive to strain rates and are prone to crack at high strain rates. As a result, the subsequent machining of cemented carbide is extremely difficult.
2, Porosity
Compared with as cast materials, the machinability of tungsten carbide is poor, mainly due to its unique porosity. Porosity leads to micro intermittent cutting and micro fatigue of blade edges. When the tool cuts from the hole to the solid particles, the blade continues to be subjected to small impact. As a result, small cracks are generated on the cutting edge, and these fatigue cracks continue to increase until the cutting edge is slightly collapsed.
The porosity will also reduce the thermal conductivity of the parts, resulting in high temperature on the cutting edge, easy to cause cutting edge deformation and crescent wear at high temperature and high pressure. The porous structure of the material provides a channel for the discharge of the cutting fluid, which is easy to cause hot cracks or deformation.
In addition, the internal porous structure also causes the increase of the surface area, which makes the material easily oxidized and carbonized in the heat treatment. The hardness of these oxides and carbides is usually very high, which is easy to cause the hard point wear of the tool.
3, Rigid Particle
WC particles in tungsten carbide are very hard, while Co phase is relatively soft, which leads to discontinuous cutting and micro fatigue at the cutting edge, resulting in chipping at the tool tip. So, the cutting tools used in cemented carbide wear very quickly, so it is necessary to replace and adjust cutting tools frequently.
- Tungsten Carbide Manufacturer & Supplier, Chinatungsten Online: tungsten-carbide.com.cn
- Tungsten News & Prices of China Tungsten Industry Association: www.ctia.com.cn
- Molybdenum News & Price: news.molybdenum.com.cn
- Tel.: 86 592 5129696; Fax: 86 592 5129797; Email: sales@chinatungsten.com