Injection Molding: Binder
- Details
- Category: Tungsten Information
- Published on Monday, 23 October 2017 00:21
The binder for injection molding consists of waxes and other polymers, and a variety of process aids are added.
Wax Selection:
Common waxes include paraffin wax, beeswax, palm wax and short chain polymers similar to paraffin wax. These waxes have lower viscosity, better wettability and low viscosity. than those of other polymers. And the volume of the polymer is smaller than that of other polymers. The relative molecular weight of wax is small and volatile, which is beneficial to degreasing.
Multicomponent Binder:
It is difficult to degrease with single wax. Because the melting temperature is narrow and the thermal debinding is very slow, and solvent degreasing and other degreasing methods should not be adopted. Therefore, in the injection molding process, it is often mixed with other polymers, lubricants and other components to form a multi component binder.
Because the degreasing process of different components is different, one component can be preferentially discharged when degreasing, forming a gas channel first, while the other component plays the role of skeleton support. The ideal binder often contains a main component with volume fraction of 30%-70%.In addition to the common components of wax cooking oil, cellulose acetate, palm oil, camphor and naphthalene, polyvinyl alcohol, water, oleic acid, stearic acid, aluminum stearate, ethanol, peanut oil, Cod Liver Oil, polyvinyl butyral etc..
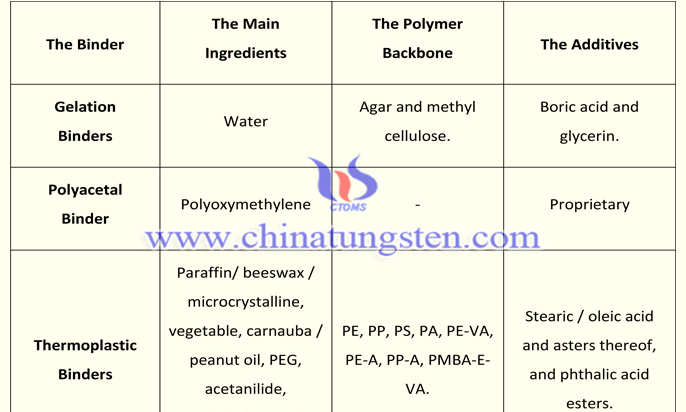
Other Ingredients:
As degreasing behaviors such as wetting, wetting, mold improve powder mixture viscosity, residual stress exist, in the actual production, additives, mould anti sticking agent, complexing agent, plasticizer, solvent, lubricant and reinforcing agent are often used in the process of mixture addition.
- Tungsten Carbide Manufacturer & Supplier, Chinatungsten Online: tungsten-carbide.com.cn
- Tungsten News & Prices of China Tungsten Industry Association: www.ctia.com.cn
- Molybdenum News & Price: news.molybdenum.com.cn
- Tel.: 86 592 5129696; Fax: 86 592 5129797; Email: sales@chinatungsten.com