Injection Molding Process Parameter - Backpressure
- Details
- Category: Tungsten Information
- Published on Sunday, 24 September 2017 22:34
According to the running state of the screw, the pressure in the material is divided into three kinds in the injection molding process, which include plasticizing pressure, injection pressure and dwell pressure.
These pressure and the actuation duration will play a decisive role in the forming quality of material. Among them, backpressure directly influences the plasticizing quality and forming efficiency of the melt.
1, Definition
In the process of melting and plasticizing of the powder mixture, the melt moves to the front of the cylinder (metering chamber). As the melt increases, a pressure is gradually formed to push the screw backward. In order to prevent the screw from retreating too fast and to ensure uniform compaction of the melt, it is necessary to provide an opposite direction of pressure on the screw. Preventing the screw from retreating, this kind of pressure is called plasticizing pressure, also known as backpressure.
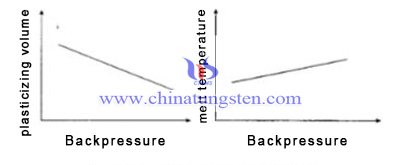
2, Determination and Implementation
The control of backpressure is achieved by adjusting the oil return valve of the injection cylinder to maintain a certain amount of pressure on the cylinder. And the selection of backpressure mainly depends on the type, temperature and actual plasticizing effect of the melt. Usually, backpressure is between 6-20MPa.
3, Function
(1) Compacting melt, increasing density;
(2) Extruding material to reduce internal bubbles and increase uniformity;
(3) Promoting the full plasticization of the melt, improving the mixing uniformity, enhancing the humidity of the melt, improving the flowability of the melt filling process, and improving the surface quality of the melt.
4, Hazards of Abnormal Backpressure
When the pressure is high: the melt pressure will be large, temperature will be high, melt viscosity will decrease, plasticizing efficiency will reduce, the screw back velocity will be slow, the plastic feed time will be long, and the cycle time will be increased, and finally lead to the decrease of efficiency; nozzle prone to tape casting, products appear cold spots; mechanical wear increased.
When the back pressure is low and the screw back fast, the melt will not be compacted and the internal air will not be sufficiently discharged.
- Tungsten Carbide Manufacturer & Supplier, Chinatungsten Online: tungsten-carbide.com.cn
- Tungsten News & Prices of China Tungsten Industry Association: www.ctia.com.cn
- Molybdenum News & Price: news.molybdenum.com.cn
- Tel.: 86 592 5129696; Fax: 86 592 5129797; Email: sales@chinatungsten.com