Injection Molding Process Parameter - Packing Pressure
- Details
- Category: Tungsten Information
- Published on Sunday, 24 September 2017 22:38
In the injection molding process, the packing procedure may be the most important stage that affects the final product performance. After thermal expansion, polymer melts will shrink when cool, inevitably leading to uneven distribution of density and stress inside the product.
As a result, it is important to select the proper packing pressure to ensure the performance and quality of the product. The packing procedure is a non-isothermal and compressible complex stage.
Definition: after the molten material fills the mold cavity, the static pressure applied by the screw (or plunger) to the melt in the mold is called the packing pressure.
Function: When its molten is cooling / curing contraction, a pressure is continued to melt into the filling space to reduce or avoid the generation of dents. At the same time, the material has a certain pressure on the melt compaction, so that the material can cling to the die wall to obtain accurate shape.
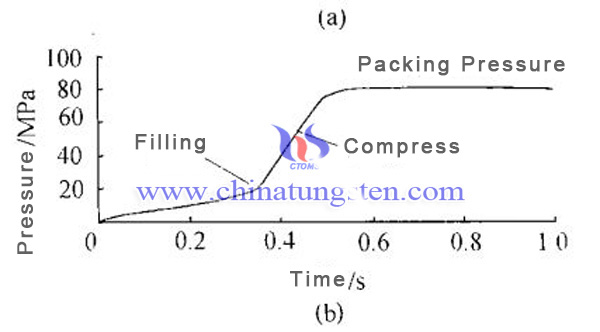
Selection and determination: packing pressure shall not exceed the setting pressure of the extrusion section, otherwise it may cause trimmings. Multistage packing pressure is decreased at each period, while the ideal drop is a linear descent to meet the actual needs of gradual contraction.
Packing pressure can be adjusted according to need. When the packing pressure is high, more melt materials will enter the mold cavity and the resulting plastic parts will have the characteristics of high density, small shrinkage and good mechanical properties. However, when the pressure is too high, the larger residual stress will lead to the overflow of the material, decreasing the strength and even cause difficulties in mold unloading. Low packing pressure is easy to cause the uncompact products and the poor forming effect.
- Tungsten Carbide Manufacturer & Supplier, Chinatungsten Online: tungsten-carbide.com.cn
- Tungsten News & Prices of China Tungsten Industry Association: www.ctia.com.cn
- Molybdenum News & Price: news.molybdenum.com.cn
- Tel.: 86 592 5129696; Fax: 86 592 5129797; Email: sales@chinatungsten.com