Powder Injection Molding Process
- Details
- Category: Tungsten Information
- Published on Thursday, 21 September 2017 23:03
Powder injection molding materials is actually a high filling thermoplastics, the basic principle of which is the same as that of thermoplastic injection molding. Usually, the barrel temperature, mold temperature and injection pressure are higher in injection molding.
The injection molding process includes feeding, heating, plasticization, mold closing, injection molding, pressure maintaining, cool molding, die opening and parts removal. Among them, heating, plasticizing, pressure injection and cool molding are three basic steps in the injection process. Forming temperature, injection pressure (including injection speed) and forming cycle (including injection, holding pressure, curing time) are called “three major technological conditions of injection molding process"
Motor programs for injection molding in various injection molding machines may not be the same, but the basic process is the same. Take screw type injection molding machine as an example. Its pre plastic process is as followed. The material is fed from the hopper, and the material moves along the screw as the screw rotates, and the material is gradually compacted as the screw moves.
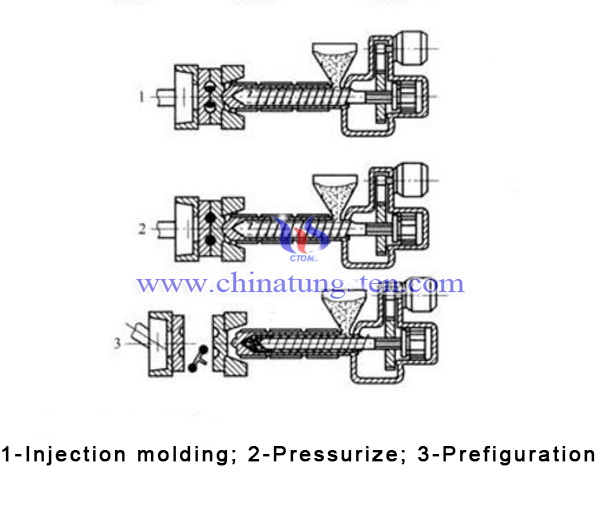
With the heating of the heating device outside the barrel and the screw shearing, the material is in a viscous state. When the material pressure at the head of the screw is large enough to overcome the resistance (back pressure), the screw then begins to move back, making what is called measurement. At the same time, the front barrel and screw head material gradually increased, when reaching the required injection quantity (i.e. screw back to a certain position), metering device hit the limit switch, the screw stops rotating and retreat.
Then, the pressure oil in the mould cylinder pushes the die closing mechanism and moves the template to close the die. The injection seat is moved forward, and the injection oil cylinder is filled with the pressure oil, so that the piston of the oil cylinder drives the screw rod to inject the material into the cavity according to the required pressure and speed.
When the material is filled with the mold cavity, the screw still holds a certain amount of pressure on the material, that is to say, to maintain the pressure to prevent the flow of material in the cavity, and to the mold cavity to add the cooling and shrinkage of the material needed. The tungsten material in the mold is cooled and shaped to obtain a certain size accuracy and surface roughness. When the mold is completely cooled, the mold opens and the part is pulled out under the action of the ejection mechanism so as to complete an injection molding process.
- Tungsten Carbide Manufacturer & Supplier, Chinatungsten Online: tungsten-carbide.com.cn
- Tungsten News & Prices of China Tungsten Industry Association: www.ctia.com.cn
- Molybdenum News & Price: news.molybdenum.com.cn
- Tel.: 86 592 5129696; Fax: 86 592 5129797; Email: sales@chinatungsten.com