Mixing Process in Injection Molding
- Details
- Category: Tungsten Information
- Published on Thursday, 21 September 2017 22:56
Mixing is the process of adequately mixing the raw powder and binder at a certain device and temperature to make them homogenized and meet the requirements of the injection. The nature of the feed determines the performance of the final injection into the product, so this process of mixing becomes very important, which involves factors and methods of adding binder and powder, mixing temperature, mixing device characteristics and many other factors.
An important index to evaluate the quality of mixing process is the uniformity and consistency of the obtained feed.The mixing process of metal powder injection is completed under the combined action of thermal effect and shearing force. In order to avoid the decomposition of binders or the separation of powder and binder due to the low viscosity, And the magnitude of shear forces vary according to the mode of mixing. The commonly used mixing devices are double screws extrude, Z impeller mixer, single screw extrude, plunger extrude, double planetary mixers, double cam mixers and so on, which are suitable for the preparation of mixtures of viscosity in the range of 1-1000Pa. S.
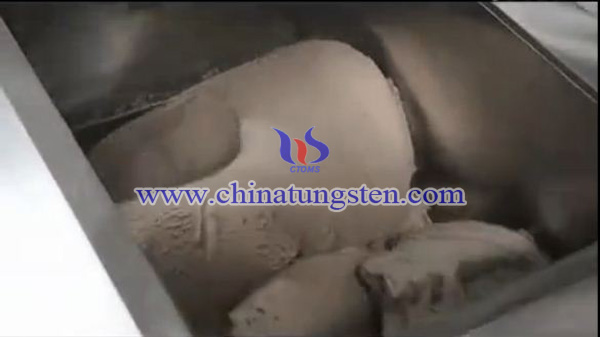
For cemented carbide injection molding, the forming binder system is usually composed of multiple components. To prevent the gasification or decomposition in the mixing, the high melting component is added at the very beginning, then the low melting point component is added, and finally the powder which is shaped is added. Meanwhile, the formed powders are added in batches to reduce the phenomenon of rapid torque increase in cooling, and to protect the mixing equipment.
The mixing process should be strictly controlled. When the mixing temperature is too low and the feed viscosity is too large, abrasions between the feed and the mixer will be taken. With the foreign body, feeding will lead to pores in the green compacts. The high shear force resulting from the high speed of the mixer will lead to wear and lead to impurities. When the speed is too low, sufficient shear force cannot be generated to smash the alloy powder aggregate.
- Tungsten Carbide Manufacturer & Supplier, Chinatungsten Online: tungsten-carbide.com.cn
- Tungsten News & Prices of China Tungsten Industry Association: www.ctia.com.cn
- Molybdenum News & Price: news.molybdenum.com.cn
- Tel.: 86 592 5129696; Fax: 86 592 5129797; Email: sales@chinatungsten.com