Two Common Tungsten Carbide Cutting Tool Cracks
- Details
- Category: Tungsten Information
- Published on Wednesday, 12 November 2014 19:10
The reasons for tungsten carbide cutting tool cracks are quite complicated, but can be generally classified into two main categories, which are hot crack and grinding crack.
I. Hot crack
Hot crack is mainly caused by the internal stress generated in the welding and heat treatment of tungsten carbide cutting tool blade. The common factors for welding stress concentration include: low toughness of tungsten carbide itself, poor thermal conductivity, instantaneous stress caused by great temperature difference, mismatching of the thickness ratio between the blade and the blade width, and so on.
II. Grinding crack
Tungsten carbide cutting tools are very sensitive towards thermal stress and thermal deformation. Because its tensile strength is just 1/5~1/8 of its compressive strength and it has uniform hard particle distribution, great grinding force and high cutting temperature, the grinding stress is easily produced. Tungsten titanium has strength lower by about 60% than tungsten-cobalt alloy, and it is brittle with poor thermal conductivity, so it is more sensitive to thermal stress. It unsuitable grinding tools are used or there is too large grinding amount during grinding, large thermal stress will be produced, which will cause grinding cracks or even blade tipping.
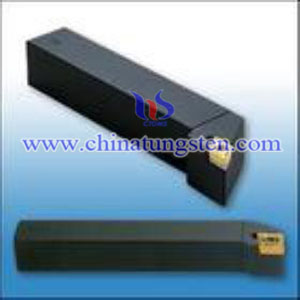
Tungsten Manufacturer & Supplier: Chinatungsten Online - http://www.chinatungsten.com
Tel.: 86 592 5129696; Fax: 86 592 5129797
Email: sales@chinatungsten.com
Tungsten & Molybdenum Information Bank: http://i.chinatungsten.com
Tungsten News & Tungsten Prices, 3G Version: http://3g.chinatungsten.com
Molybdenum News & Molybdenum Price: http://news.molybdenum.com.cn
Tel.: 86 592 5129696; Fax: 86 592 5129797
Email: sales@chinatungsten.com
Tungsten & Molybdenum Information Bank: http://i.chinatungsten.com
Tungsten News & Tungsten Prices, 3G Version: http://3g.chinatungsten.com
Molybdenum News & Molybdenum Price: http://news.molybdenum.com.cn