The Solvent Extraction Separation of Tungsten in The Form of APT from High Mo-Containing Solution
- Details
- Category: Tungsten Information
- Published on Thursday, 08 July 2021 05:35
With the continuous and heavy consumption of high-class tungsten resources, the content of Mo in the available resources is higher and higher in recent years. Therefore, it is urgent to develop a suitable process for the separation of Mo from tungstate solutions containing high content of Mo. In recent years, a novel solvent extraction process using H2O2 as complex agent for separating Mo and W from tungstate solution containing high content of Mo was developed. And the new process provided obvious advantages including deep removal of Mo, high recovery of W, high added value of Mo product, low cost, clean and environmentally friendly. A new solvent extraction separation method of W has successfully conducted in the form of APT from high Mo-containing solution.

The separation method of tungsten is as following steps: The pH of the ammonium tungstate solution was adjusted to about 3.5 by bipolar membrane electrodialysis, and then a certain amount of H2O2 was added into the solution. The solution of tungstate peroxide and molybdate peroxide was used as the feed for extraction. The pH value of feed was adjusted by H2SO4 or NH3·H2O solution. The dosage of H2O2 was measured according to the mole ratio of H2O2 to W and Mo, which is. The feed was placed in a thermostat at 15 °C for a certain time before extraction.
The continuous running test of the solvent extraction separation of Mo and W by H2O2-complexation with TRPO/TBP was carried out in the mixer settler. Fig. 2 shows the top view of the mixer settler. The mixer settler with traditional structure was used for extraction. The size of each mixing chamber is 15 cm long × 5 cm wide × 12 cm high and the false bottom is 4 cm high. The size of each settling chamber is 35 cm long × 5 cm wide × 11 cm high. Each of the settling chambers is 7 times the length of the mixing chamber. The total volume of each mixer settler is 2.2 L.
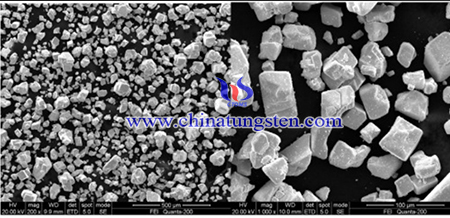
The reaction rate and phase separation speed of the stripping system were slower than in extraction system. Thus, the mixer-settlers with multi-mixing chambers were used in the stripping process to increase the contact time of two phases. The volume of the settling chamber was increased to lengthen the phase separation time. The size of each mixing chamber is 5 cm long × 5 cm wide × 12 cm high and the false bottom is 4 cm high. The size of each settling chamber is 15 cm long × 5 cm wide × 12 cm high.
The inlet flow rate of the aqueous and the organic solution was controlled by a constant flow rate peristaltic pump. The equilibrium pH value was adjusted by adding H2SO4 or NH3·H2O and determined by KE1103 pH meter on-line. The running time was counted after the running became stable.
The APT product was prepared from the raffinate with NH3·H2O addition by evaporating crystallization. The tests were carried out by stirring and heating the raffinate with NH3·H2O addition in a beaker immersed in an electro thermostatic water bath under a certain temperature for a specified time. The crystallization slurry was removed from the water bath for solid–liquid separation without cooling. The APT crystallization was washed by a little deionized water and then dried in a thermostat under 80 °C.
The concentrations of Mo and WO3 were determined by colorimetry using potassium thiocyanate and ammonium thiocyanate, respectively. In sample pretreatment, the solid samples were melted with sodium carbonate (Na2CO3) and sodium peroxide (Na2O2) under 700 °C for 7 min, and then dissolved and volumed by deionized water.
In conclusion, a new solvent extraction separation method of W has successfully conducted in the form of APT from high Mo-containing solution. The results indicated that the measures could effectively improve the Mo/W separation effect and phase separation of the extraction and stripping system. The system was very stable and the separation property was good.
- APT Manufacturer & Supplier, Chinatungsten Online: ammonium-paratungstate.com
- Tungsten News & Prices of China Tungsten Industry Association: www.ctia.com.cn
- Molybdenum News & Price: news.molybdenum.com.cn
- Tel.: 86 592 5129696; Fax: 86 592 5129797; Email: sales@chinatungsten.com