WO3-TiO2 Catalysts Obtained From APT for Pyrolysis of Cottonseed Oil Dregs
- Details
- Category: Tungsten Information
- Published on Thursday, 13 May 2021 05:06
Biofuels have emerged as an alternative to replace fossil fuels used for energy, heat, and transport, which account for 80% of total global energy use. The growth in energy demand has intensified the search for alternative sources to replace oil, minimizing the emission of pollutants.
Waste materials rich in triacylglycerols (TAG) and Free Fatty Acids (FFA) are attracting increased attention in the context of green chemistry, because they are inexpensive and assist in waste management and the avoidance of environmental impacts. One such material, cottonseed oil sludge, is a promising alternative source to produce biokerosene. Among other advantages, this material is rich in oil (TAG + FFA) (approximately 65%, by mass).
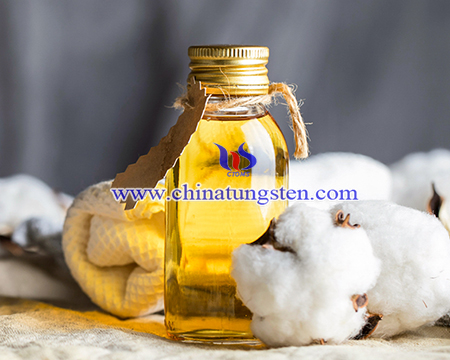
Thus, WO3-TiO2 catalyst (WT = WO3:TiO2 (15:85) was prepared to applied in pyrolysis of cottonseed oil dregs using ammonium paratungstate (APT). The synthesis process of WT catalyst was synthesized by polymeric precursor method as following steps:
The precursors used in the syntheses were ammonium paratungstate as the tungsten source, titanium chloride as the titanium source, the proportion of W or Mo was 15%, relative to the support (TiO2 or ZrO2). Firstly, calculated amounts of APT and distilled water were placed into Becker and stirred at 50–60 °C for 30 min. Secondly, a particular content of titanium chloride solid was then added to the solution and stirred at 70 °C for a period less than 10 min; pH 2 was maintained during the reaction. After complete mixing, the materials were subjected to a heat treatment at 300 °C for 2 h in a muffle furnace. The resulting WT catalyst was triturated and then calcined at 700 °C for 1 h. The catalysts were characterized by X-ray powder diffraction (XRD) and surface area analysis, and nitrogen adsorption isotherms were performed at −196 °C to determine the surface area.
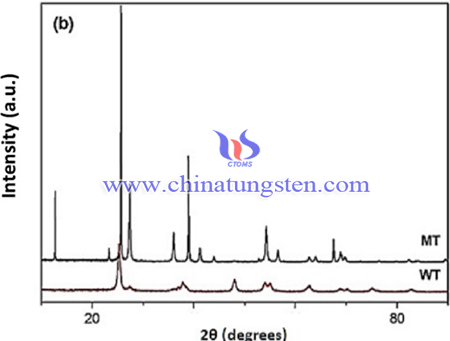
In conclusion, the mass conversion performed in the presence of catalysts at 550 °C resulted in an average yield of around 32%, compared to a value of 19% for a non-catalytic process under a nitrogen atmosphere, with the same values for the yields under a reactive hydrogen atmosphere. A higher reaction temperature led to an increase in hydrocarbon yield. When a reaction temperature of 500 °C was used, the WT catalyst showed the best hydrocarbon performance, while for the tests conducted at a temperature of 550 °C this catalyst gave the lowest yield.
- APT Manufacturer & Supplier, Chinatungsten Online: ammonium-paratungstate.com
- Tungsten News & Prices of China Tungsten Industry Association: www.ctia.com.cn
- Molybdenum News & Price: news.molybdenum.com.cn
- Tel.: 86 592 5129696; Fax: 86 592 5129797; Email: sales@chinatungsten.com