Repair Process of Tungsten Carbide Drawing Die
- Details
- Category: Tungsten Information
- Published on Sunday, 22 July 2018 20:22
The manufacture of tungsten carbide drawing dies and the repair of old moulds are inseparable from mechanical grinding. Relatively speaking, the grinding process in mold manufacturing is rather complicated, including rough grinding, fine grinding, correct grinding and polishing. If necessary, it should be supplemented by electrolysis reaming.
In production, the consumption of tungsten carbide drawing dies can be divided into rupture and wear. The broken mould can only be scrapped, while the worn die can be repaired and reused. So, the proportion of the broken mould should be reduced as far as possible.
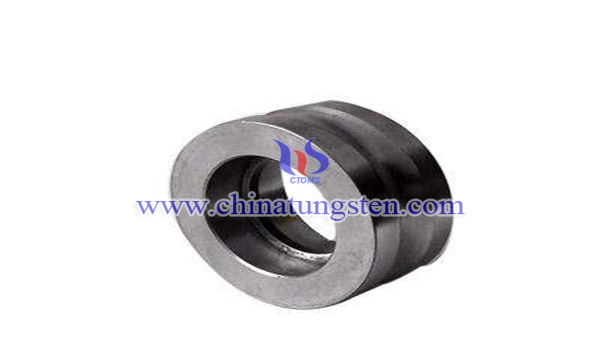
1, Abrasive
Commonly used abrasives are diamond powder, boron carbide, silicon carbide and alumina. In addition to the hardness of the abrasive, there is also an edge. When grinding, the abrasive itself is also worn, and the grinding performance decreases when the corners become round.
Diamond powde is often gray and white with its inclusions. Because natural diamonds are expensive and have less sources, they usually use synthetic diamond powder or cubic boron nitride powder.
Boron carbide(B4C), is a gray black diamond crystal with a metallic luster on the surface, of which the density is 2.48 ~ 2.52t/m3, and the melting point is 2450℃. When the temperature is higher than 2600℃, it will decompose and volatilize. Boron carbide is chemically stable, insoluble in water, and does not react with acids and bases, which has good corrosion resistance. The hardness of boron carbide is second only to diamond. And it has the characteristics of wear resistance and pressure resistance. Its grinding rate is 60% ~ 70% of the diamond, and it is more than 5 times of the high quality green silicon carbide. Boron carbide is the most commonly used abrasive for carbide grinding at present.
Pure silicon carbide is colorless crystal with a density of 3.06 to 3.20t/m3. Common silicon carbide varieties are black carborundum, green silicon carbide and cubic silicon carbide (green). The hardness and brittleness of green silicon carbide are higher than that of black silicon carbide, which is similar to boron carbide, but the price is much cheaper than that of boron carbide. Cubic silicon carbide particles have good integrity and high toughness and can be used for polishing.
The density of alumina (Al2O3) is 3.9~4.1t/m3. Its The crystal is columnar or conical, with different colors due to inclusions. Colorless and transparent is called white jade. It is called "Ruby" with chrome red and transparent. Cobalt blue and transparent is called sapphire. Alumina for abrasives is white corundum, light yellow single crystal corundum, Zong Gangyu, Ge Gangyu (red or purplish red) and zirconium corundum (brown gray). Corundum hardness is slightly higher than that of tungsten carbide, white or light-yellow corundum grinding performance is better, chrome corundum and zirconia corundum are good toughness, more for grinding and polishing.
2, Particle Size of Abrasive
According to the grinding roughness, the abrasive is crushed into different sizes. Powdered Abrasives cannot be directly used, which need to be added to a certain proportion of liquid into a grinding agent. Frequently used liquids include water, mineral oil and vegetable oil. They can evenly distribute the abrasive and absorb it in the mold hole to reduce the splash of abrasive.
- Tungsten Carbide Manufacturer & Supplier, Chinatungsten Online: tungsten-carbide.com.cn
- Tungsten News & Prices of China Tungsten Industry Association: www.ctia.com.cn
- Molybdenum News & Price: news.molybdenum.com.cn
- Tel.: 86 592 5129696; Fax: 86 592 5129797; Email: sales@chinatungsten.com