Hardness Analysis of Tungsten Carbide Die
- Details
- Category: Tungsten Information
- Published on Thursday, 24 May 2018 22:44
Tungsten carbide die for cold heading screw in China is slightly higher in strength and slightly low in hardness, while the similar mould in Germen is on the contrary. High hardness and good wear resistance are another reason for the long service life of German tungsten carbide dies for cold heading screws. The sleeve hardness of the two kinds of moulds is basically similar.
1, Interference
When other conditions are the same, mold with small interference coefficient has small preload. The occurrence of events of the die core out of the die in the Chinese mold may be related to the small interference coefficient or the non-guaranteed machining dimension precision dimensional accuracy. German mould adopts conical cold pressing fit, of which the interference coefficient is 0.85%. Compared with the 1. 3%-1.5% in the European Union, the data used in German mold are low, and the accuracy of mold core and die sleeve matching is relatively high.
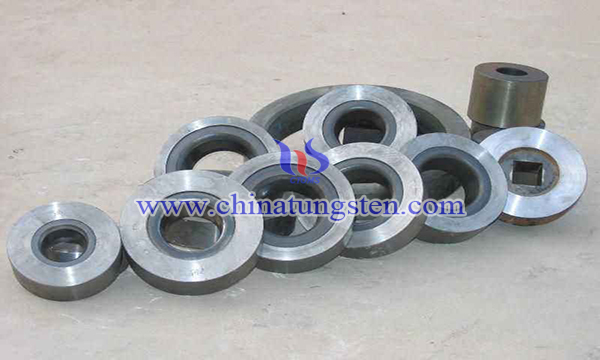
2, Processing Quality of Outer Surface of Core Rod
Grinding quality of external surface of the Chinese mould is poorer than that of German tungsten carbide die. The whole surface roughness of the German mould is in the range of 0. 32-0. 25 um. The roughness of the core surface has an effect on the service life of the die. Poor surface roughness, especially the existence of sunken, hole or micro cracks on the surface, will be the source of stress concentration and fracture, which will cause premature cracking and failure of the mold core. And the roughness of the working surface of the inner core of the mold core has a greater impact on the service life.
3, Way of Mosaic and Conditions After Mosaic
Quality of die inlaid sleeve has great influence on its service life. After the mold is inserted, the inner wall of the die sleeve presents the phenomenon of metal plastic flow and the damage of the inner wall of the mold sleeve. The serious damage indicates that the quality of the insert is poor and the mold core and the die sleeve are not completely pressed together. When the die is working, this part is not subjected to compressive stress and subjected to bending stress or shear stress. Therefore, in the working process, the core is easy to crack, resulting in early failure.
- Tungsten Carbide Manufacturer & Supplier, Chinatungsten Online: tungsten-carbide.com.cn
- Tungsten News & Prices of China Tungsten Industry Association: www.ctia.com.cn
- Molybdenum News & Price: news.molybdenum.com.cn
- Tel.: 86 592 5129696; Fax: 86 592 5129797; Email: sales@chinatungsten.com