Correlation Test of Steel Bonded Tungsten Carbide Dies
- Details
- Category: Tungsten Information
- Published on Sunday, 13 May 2018 18:00
In the process of hot extrusion of the valve stem, the steel bonded carbide mold appeared ploughing and abrasion, but the furrow was shallow. The abrasive produced by wear will produce ploughing on the surface of the die when extruding. Due to the homogeneous dispersion of hard phase in the die, the ploughing cannot be carried out smoothly.
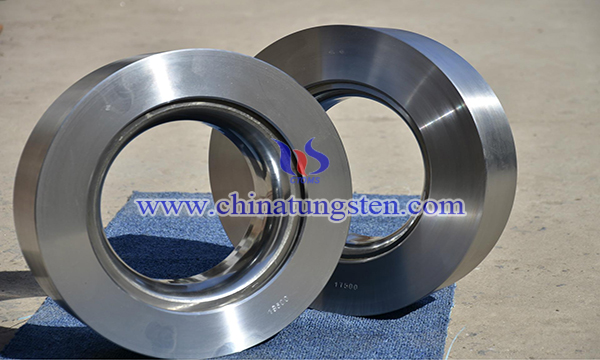
There are less furrow furrows in the die cavity surface of steel bonded tungsten carbide die, and the ploughing wear is less than that of other hot working die steels, which is more than 10 times higher than the ordinary tool steel, thus the economic effect is very significant. Under the lubrication condition of water agent graphite, thermal fatigue cracking and peeling pits are produced in the steel bonded tungsten carbide. When the mold works, its surface is in a state of quenching and acute heat.
Steel bonded tungsten carbide has poor heat and fatigue resistance and it is easy to form thermal fatigue cracks. Then the cracks expand into mesh crackles, causing metal spalling. And the core work is scuffed, resulting in workpiece difficult to be ejection from the concave die. Finally, the die is invalid.
Therefore, thermal fatigue is the main reason for the failure of steel bonded tungsten carbide dies. We can make it have higher thermal hardness, strength and toughness and lower friction factor by changing the composition, content, forging and heat treatment process of steel bonded tungsten carbide. For example, adding TaC into tungsten carbide. When TaC content is high (mass fraction 5% or more), high hardness and low friction factor can be obtained. The D-43 of the United States is an example.
In addition, when the lubricant is applied, the surface of the mold is repeatedly chilling and quench heat, which will accumulate considerable cyclic thermal stress. Finally, it is released in a cold and hot fatigue way, forming a cold and hot fatigue crack.
Through the comparison and analysis of the above experiments, the following conclusions can be drawn:
1, The application of steel bonded tungsten carbide in hot extrusion of valve stem is feasible, and its life expectancy is obviously higher than that of other die steels. It has good prospects for popularization and application.
2, Thermal fatigue causes cracking on the surface of the die and then forms a peeling pit, which is the main reason for the failure of the hot extrusion die for tungsten carbide.
3, Optimizing the chemical composition of steel cemented carbide, improving its matrix structure, improving its strength and toughness, and improving the lubrication condition are the urgent problems to improve the life of hot extrusion die for steel bonded tungsten carbide.
- Tungsten Carbide Manufacturer & Supplier, Chinatungsten Online: tungsten-carbide.com.cn
- Tungsten News & Prices of China Tungsten Industry Association: www.ctia.com.cn
- Molybdenum News & Price: news.molybdenum.com.cn
- Tel.: 86 592 5129696; Fax: 86 592 5129797; Email: sales@chinatungsten.com