Dynamic Magnetic Compaction
- Details
- Category: Tungsten Information
- Published on Friday, 22 December 2017 21:40
Dynamic Magnetic Compaction(DMC)is a new near net forming technology developed by the United States in 1995, which has been developed by 3 research units with a cost of 8500,000 dollars. The product made by dynamic magnetic compaction has high density and excellent mechanical properties. So, the technology can be applied to the compaction of various powders.
At the same time, because the pressing process is fast, it can ensure that the microstructure of materials does not change, which helps to improve the material properties. Therefore, it has a good development space in the field of tungsten carbide.
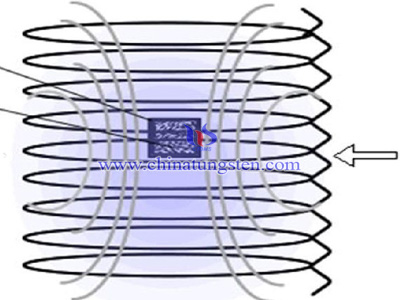
Principle of Dynamic Magnetic Compaction
Tungsten carbide powder is loaded into a conductive metal container placed in the center of the electromagnetic induction coil. When the pulse current is introduced into the induction coil, a magnetic field is formed in the coil.
Induced current inside the conductive metal container induces the interaction between the induced current and the applied magnetic field, and generates a high-voltage magnetic field in the radial direction to compress the metal container in the radial direction, so that the powder can be pressed in two dimensions. The whole process of suppression is very rapid, which is less than 1ms.
Application Advantages of Dynamic Magnetic Compaction
For refractory metal carbide powders containing WC and TiC, they can achieve higher density by dynamic magnetic compaction than other forming methods, thereby reducing sintering shrinkage and alloy porosity. In addition, the rapid dynamic magnetic compaction process can help to keep the ultrastructure of the material constant and improve the performance of the tungsten carbide.
- Tungsten Carbide Manufacturer & Supplier, Chinatungsten Online: tungsten-carbide.com.cn
- Tungsten News & Prices of China Tungsten Industry Association: www.ctia.com.cn
- Molybdenum News & Price: news.molybdenum.com.cn
- Tel.: 86 592 5129696; Fax: 86 592 5129797; Email: sales@chinatungsten.com