Effect of Binder System on Solvent Debinding
- Details
- Category: Tungsten Information
- Published on Wednesday, 01 November 2017 22:22
Injection molding has the advantages of high utilization ratio, good surface finish and low production cost. It is especially suitable for mass production of hard alloy parts with small size and complex shape.
Debinding process is one of the most important and difficult steps in the injection molding process. Improper control will lead to defects such as debinding, deformation and composition fluctuation, which will affect the properties of the final cemented carbide products.
Thermal debinding and solvent debinding are the most commonly used in the debinding process of cemented carbide injection molding. Solvent degreasing is generally regarded as the first step and the most important step in the two-step degreasing process. The quality of solvent degreasing directly affects the quality of cemented carbide products.
Solvent debinding binder system, degreasing temperature, degreasing time, sample thickness and shape are the most important process components. Because the composition of different binder systems has the most obvious and direct influence on the degreasing rate, the influence of the composition of the binder system on the degreasing rate is very important.
The figures of degreasing rate change of 2 paraffin based groups (1#, 2#) and 1 kinds of oil-based (3#) are shown below.
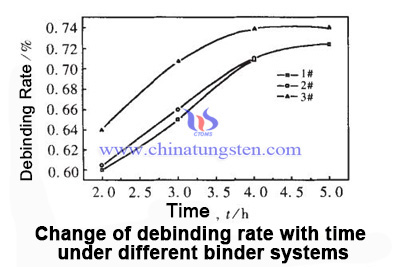
With the increase of degreasing time, the removal rate of binders in the binder based cemented carbide (PW) cemented carbide injection blanks increased. The removal rate and final debinding rate of different binders of paraffin base (PW) were not significantly different.
1, For paraffin with larger molecular weight, the lower molecular weight heptane solvent diffuses into the polymer with higher molecular weight, such as PW. Chain strength of the polymer is weakened, and the chains are dissolved. Then the swelling effect occurs, and the dissolution occurs again. As a result, the dissolution rate is slow.
2, The degreasing rate of oil based (mainly based on vegetable oil and mineral oil-based) binder was faster than that of the former, and the final debinding rate was higher than that of paraffin based (PW) binder. Oil based binders can be easily dissolved by solvent, and the degreasing time is short, thus showing better solvent debinding characteristics.
In addition, the oil based binder has better flowability than wax, and can relax the internal stress during injection molding to avoid the generation of micro cracks. Organic liquids containing oil based small molecules have good solubility with n-heptane, they are easier to be removed from the injection blank into the solvent, and do not produce swelling effect, showing a better solvent than PW.
- Tungsten Carbide Manufacturer & Supplier, Chinatungsten Online: tungsten-carbide.com.cn
- Tungsten News & Prices of China Tungsten Industry Association: www.ctia.com.cn
- Molybdenum News & Price: news.molybdenum.com.cn
- Tel.: 86 592 5129696; Fax: 86 592 5129797; Email: sales@chinatungsten.com