Degreasing Defects of Tungsten Carbide
- Details
- Category: Tungsten Information
- Published on Wednesday, 01 November 2017 22:17
Common degreasing defects include debinding deformation, degreasing crack, bubbling, warping, delamination and decarburization. Bubble, warping and delamination are common defects in thermal debinding process. It is one of the core of cemented carbide production control to formulate corresponding defect prevention and solution measures according to specific defects.
1, Bubble
There are two main causes of bubble:
1.1 the excessive heating rate leads to excessive pressure when the gas escapes.
1.2 impurities introduced into low surface energy will also blow up cemented carbide. The particles with larger size and certain plane have lower surface energy than other components. When heating degreasing, the gas in the body will continuously gather to these particles, forming bubble.
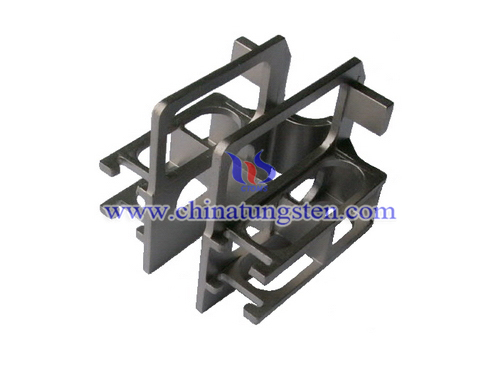
2, Warping
The green is uneven heated, so coefficient of expansion of high temperature area is higher than that of the low temperature region. And the green with powder binder separation, thus, at the same temperature, the swelling pressure of the binder agglomeration is large.
3, Delamination
This defect is a further manifestation of the with filling phenomenon in the injection process. With filling is difficult to find before degreasing, but it appears different degree of delamination after degreasing. If the degree of sandwich is severe, the crack can be seen under scanning electron microscope at low magnification. According to our experiment, the defect of with filling is common, of which the degree is different.
- Tungsten Carbide Manufacturer & Supplier, Chinatungsten Online: tungsten-carbide.com.cn
- Tungsten News & Prices of China Tungsten Industry Association: www.ctia.com.cn
- Molybdenum News & Price: news.molybdenum.com.cn
- Tel.: 86 592 5129696; Fax: 86 592 5129797; Email: sales@chinatungsten.com