Causes of Debinding Cracks
- Details
- Category: Tungsten Information
- Published on Wednesday, 01 November 2017 22:13
Main reasons causing the degreasing crack of tungsten carbide are the segregation of the molding agent (the uneven mixing of the binder), the debinding temperature and the residual internal stress.
1, Segregation of Molding Agent
When the product of component segregation is put into the solvent, with the removal of the molding agent, a large hole will form in the body, which may form a crack source. The forming agent is uniformly coated on the surface of the billet, and the coated particles contact well.
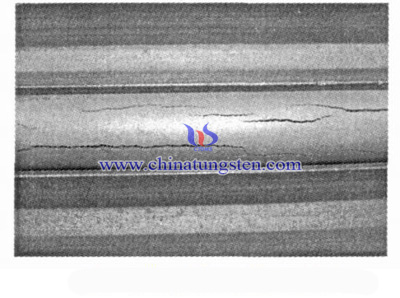
At this time, the forming agent coating forms a connected soft phase. When solvent debinding, the soluble component of the molding agent is gradually removed. A connected degreasing pore is formed, so that the crack source is not easy to be formed, and the cracking phenomenon is avoided.
2, Degreasing Temperature
During degreasing, when the heating speed is too fast, the power of the solvent diffusion to the molding agent will increase and the molecular motion will intensify. As a result, the solvent degreasing in the early stage of diffusion, and the swelling, dissolution rate will be too fast.
At this time, the degreasing channel has not been formed in a short time, a large number of gas expansion, the internal pressure is too large, resulting in cracking of billet. The solution is to reduce the heating rate, step by step insulation, or first solvent degreasing for thermal degreasing to open the diffusion channel.
3. Residual Internal Stress
The residual internal stress in the shot blank is the main factor causing solvent debinding cracking. The reason is that the plastic forming agent component is paraffin wax, of which the characteristic is high sensitivity to temperature and condensing shrinkage rate, shorter time of injection molding after the rapid cooling, the polymer chains in the adhesive force in the frozen state, caused by the rigid internal stress of gold in the blank.
In the solvent debinding process, the free volume of macromolecular chains in solvents increases with the removal of wax. This part of the stored internal stress is released, so that cracks in the cemented carbide billet has already existed (the segregation of forming agent) to expand, resulting in cracking and collapse of hard aggregate. It can be reduced by body annealing.
4. Other Reasons
The loading is too low. When the binder is melted, the powder moves too much under the action of gravity, resulting in cracks. In the thick wall transition, or in varying density place, it is easy to crack. The reason is that the gas escape from the thin wall or place with high density, forming pressure difference caused by crack.
- Tungsten Carbide Manufacturer & Supplier, Chinatungsten Online: tungsten-carbide.com.cn
- Tungsten News & Prices of China Tungsten Industry Association: www.ctia.com.cn
- Molybdenum News & Price: news.molybdenum.com.cn
- Tel.: 86 592 5129696; Fax: 86 592 5129797; Email: sales@chinatungsten.com