Surfacing Heat Protection Material - Tungsten Carbide
- Details
- Category: Tungsten Information
- Published on Thursday, 26 October 2017 20:41
Surfacing is an economical process for surface modification of materials. It is suitable for strengthening or repairing worn parts surface under severe wear conditions.
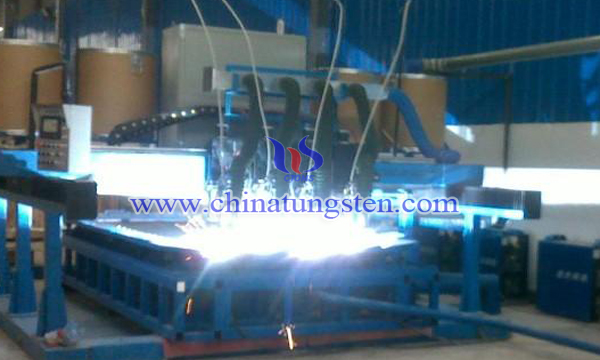
The working principle of surfacing welding is to use the welding method to lay a layer of special performance material on the surface of parts. According to statistics, abrasive wear accounts for nearly half of the economic losses caused by all kinds of wear and tear in the industrial field. Therefore, abrasive wear resistance is one of the most important applications of hardfacing.
Tungsten carbide is one of the main raw materials of hard alloy, tungsten carbide composite alloy with high hardness, high wear resistance, high strength and high positive elastic modulus, in all surfacing alloy, the abrasion resistance of the highest performance, therefore, WC composite alloy becomes a composite surfacing alloy which can not be replaced on the surface of workpiece working under strong abrasive wear and gas particle wear.
There are three types of tungsten carbide for surfacing: one is cast tungsten carbide, the other is composed of WC and W2C eutectic; the other is sintered tungsten carbide with cobalt as binder; In addition, there is a kind of extra coarse grain tungsten carbide, which is made by mixing tungsten particles with carbon black in a special carbonization furnace.
There are more kinds of tungsten carbide composite surfacing materials. The commonly used tubular tungsten carbide electrode with granular casting can be used for oxyacetylene flame surfacing. In this electrode as core, coated with basic low hydrogen type coating can be made for hand arc welding with welding rod. In addition, tungsten carbide can be used to prepare patent cored wire or welding strip for automatic arc surfacing.
The high wear resistance of tungsten carbide composite hardfacing alloy largely depends on tungsten carbide hard phase in alloy material, which is generally used to evaluate the thermal resistance performance of ablative heat insulation coating: The ablation rate was AR, mass ablation rate MAR, adiabatic index IT, ablation performance index API, ablation heat AH. Among them, AR and API are important evaluation parameters, which reflect the ablation resistance and heat insulation performance of the material. The smaller the AR, the larger the API, the higher the ablation resistance of the material, and the better thermal insulation. The parameters such as AR and API have some reference value for the selection of tungsten carbide heat insulation agent.
- Tungsten Carbide Manufacturer & Supplier, Chinatungsten Online: tungsten-carbide.com.cn
- Tungsten News & Prices of China Tungsten Industry Association: www.ctia.com.cn
- Molybdenum News & Price: news.molybdenum.com.cn
- Tel.: 86 592 5129696; Fax: 86 592 5129797; Email: sales@chinatungsten.com