Injection Molding: Degreasing Defect
- Details
- Category: Tungsten Information
- Published on Monday, 23 October 2017 00:12
In the injection molding process, comprehensive adoption of solvent degreasing and thermal debinding process can greatly shorten the degreasing time and improve the production efficiency. Degreasing defects (deformation, cracks, etc.) often occurs during degreasing process of injection molding, affecting the quality of degreasing.
Defects in the degreased blank can be divided into 2 types: one is caused by the injection defects, and the other is caused by improper control of the degreasing process parameters.
1, Deterioration of degreasing process caused by injection defects
1.1 Deterioration caused by surface flowing veins. After solvent degreasing, the sample was removed from the solution. The internal pressure of the solid body increases with the rapid evaporation of a large amount of solvent in the degreased billet. It is easy to crack in the weak parts of the body, especially in the weak position of the surface flowing pattern and the gate.
1.2 Deterioration of injection blank with filling. When the solvent is skimmed, the surface of the injection blank decreases and the strength of the layer decreases gradually. When the strength drops to the internal stress equilibrium, the condensation layer will crack along the axial direction of the injection billet under the action of internal stress. The solvent debinding defects caused by injection defects can be eliminated by adjusting the injection process parameters.
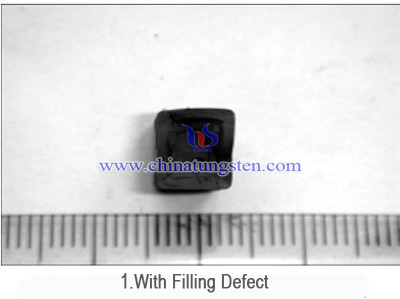
2, Improper control of the degreasing process parameters
2.1 High temperature. The high temperature during degreasing results in the diffusion and permeation rate of degreasing solvent, and the degreasing rate is too high. With the increase of the expansion effect, the foaming, deformation and crack of the cemented carbide blank are produced.
2.2 Low temperature. At low temperature, the diffusion rate of the low melting point component is too low. The activation energy of molecular diffusion with lower molecular weight is smaller, and it is easier to diffuse into the solid. When the swelling effect of the solvent molecules with lower molecular weight in the high melting point component cannot be compensated by the removal of the high melting point component, the body will crack at the initial stage of solvent debinding.
- Tungsten Carbide Manufacturer & Supplier, Chinatungsten Online: tungsten-carbide.com.cn
- Tungsten News & Prices of China Tungsten Industry Association: www.ctia.com.cn
- Molybdenum News & Price: news.molybdenum.com.cn
- Tel.: 86 592 5129696; Fax: 86 592 5129797; Email: sales@chinatungsten.com