Injection Molding: Selection of Degreasing Catalyst
- Details
- Category: Tungsten Information
- Published on Sunday, 22 October 2017 01:22
Because of the advantages of reaction mechanism, the rate of metal catalytic debinding is much larger than that of traditional degreasing technology.
Catalytic Rate
The catalytic reaction only in the gas - adhesive interface, which gradually develops to the internal external. This debinding mechanism does not produce cracks and voids, and a high debinding rate can be obtained. Moving rate of the binder interface to the interior is 2-4mm/h, which is much larger than that of the traditional one.
And the debinding rate of injection molding blank based on general binder is 0.2mm/h, which is 10~20 times higher than that of traditional debinding process. The effect of binder composition, catalytic gas flow rate, debinding time and debinding temperature on catalytic debinding rate was positively correlated.
Selection of Degreasing Catalyst
In the degreasing process, high speed inert gas (nitrogen, argon, helium and their mixture) can be introduced into the degreasing furnace to accelerate the diffusion of small molecules and regulate the degreasing rate. The degreasing rate can be controlled by controlling the concentration of the catalyst.
Moreover, with the decrease of the inert gas flow rate, the catalyst concentration in the degreasing zone increases, and the overall debinding rate increases as well. Therefore, the flow rate of inert gas should be controlled within a moderate range.
For most ceramic injection molding (CIM) powder materials, nitric acid is a suitable catalyst, as nitric acid has strong oxidizing property and strong gasification tendency. Under normal degreasing conditions, nitric acid vapor will not deposit in the capillary hole of ceramic parts after removing organic carrier, and will not corrode the furnace structure.
Oxalic acid can overcome the disadvantage of nitric acid, such as Y2O3 (sintered Si3N4 and SiC additives) and so on, and become another widely used catalyst. Oxalic acid is a volatile organic acid, at room temperature is solid, at 100℃ turns to gas, more than 187 degrees of decomposition into CO, CO2 and H2O. Therefore, using oxalic acid as catalyst, the treatment of waste gas after catalytic reaction is relatively simple.
When nitric acid was used as catalyst, the removal rate was 0.7 - 1.5mmh-1, and the rate of debinding was in the order of Si3N4 >ZrO2 >SiC. When the oxalic acid was used as catalyst, the degreasing rate was 0.9 - 1.5mmh-1, and the order of debinding was ZrO2 >SiC>Si3N4. It can be seen that there are great differences in the catalytic action of different catalysts. The degreasing effects of two kinds of catalysts are shown in Figure 1 and figure 2.
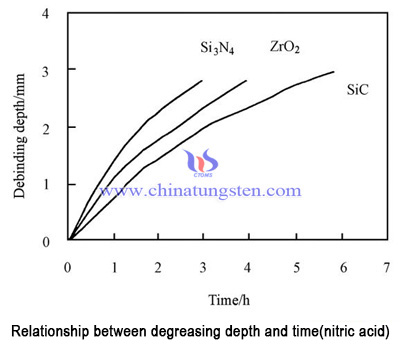
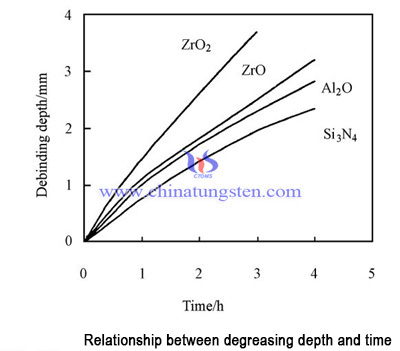
- Tungsten Carbide Manufacturer & Supplier, Chinatungsten Online: tungsten-carbide.com.cn
- Tungsten News & Prices of China Tungsten Industry Association: www.ctia.com.cn
- Molybdenum News & Price: news.molybdenum.com.cn
- Tel.: 86 592 5129696; Fax: 86 592 5129797; Email: sales@chinatungsten.com