Ultra-coarse Tungsten Carbide Powder Patent
- Details
- Category: Tungsten Patents
- Published on Monday, 06 July 2020 17:20
- Written by Fuhao
- Hits: 4199
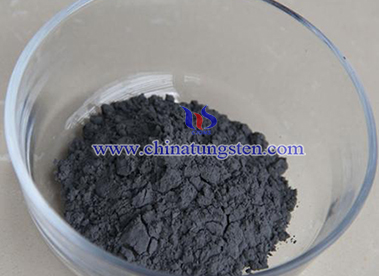
This article is to introduce a patent of the production method of ultra-coarse tungsten carbide powder.
Demand for ultra-coarse tungsten carbide powder and ultra-fine tungsten carbide powder is surging as a result of the development of cemented carbide technology.
Why Use Tungsten Heater Device that Cannot Deform under High-Temperature?
- Details
- Category: Tungsten Patents
- Published on Wednesday, 06 July 2016 16:19
- Written by xuejiao
- Hits: 5309
In hot wire CVD (Chemical Vapor Deposition) system, the energy of a chemical reaction is provided by the tungsten wire, the substrate is also heated to a certain growth temperature by thermal radiation of the tungsten wire, and uniformity of the temperature of the substrate surface would be different due to the shape of the tungsten wire. One of the most important factors of film nucleation and its uniformity growth is the uniformity of substrate surface temperature.
In typical laboratory CVD small and medium systems, the tungsten wire is wound into a solenoid-shaped tungsten heater. This winding method is relatively simple that the outer diameter of each turn is the same. But using a solenoid-shaped tungsten heater, temperature distribution on the surface of the substrate is uneven enough, using a vertical projection line of the substrate surface of solenoid axis as a reference line, if the substrate surface is far away from this line, the temperature would become lower. What’s more, the temperature of the middle of the solenoid itself is higher than the ends, which is one of the reasons for uneven temperature distribution of the substrate surface.
On the one hand, the solenoid-shaped tungsten heater will result in an uneven temperature of the substrate surface. On the other hand, in the CVD growth process, the tungsten wire usually deform under a high temperature, high temperature of the middle part would hang down and bend, led to the evenness of temperature distribution of substrate surface becomes lower, eventually makes it impossible to continue the CVD growth process, it must be replaced a new tungsten wire before continuing. As a result, it will have a certain impact on test results. Because the new tungsten wire can not exactly the same as original tungsten wire under various conditions, which will definitely affect the reliability of comparative test results.
Tungsten Metals Supplier: Chinatungsten Online www.tungsten.com.cn | Tel.: 86 592 5129696; Fax: 86 592 5129797;Email:sales@chinatungsten.com |
Tungsten News & Prices, 3G Version: http://3g.chinatungsten.com | Molybdenum News & Molybdenum Price: http://news.molybdenum.com.cn |
Tungsten Heater for Aluminizing of Car Light
- Details
- Category: Tungsten Patents
- Published on Monday, 04 July 2016 16:27
- Written by xuejiao
- Hits: 5346
In order to solve the problems of poor aluminizing performance effect of automotive lighting, long production cycle, the poor quality of the protective layer. Through the following improvements, it can further enhance the quality of the aluminum layer.
1. The injection molding: put the raw material into a mold and process it into parts.
2. Edging is to remove four sides of parts. After inspection for the exterior, remove the substandard products, blowing qualified products by air gun, and finally put parts into the transporter and transfer them to the aluminum machine, hanging the parts in fixture.
3. Pretreatment, aluminizing, the protective layer: put the part into aluminizing device and the close it for evacuation, when pressure reaches 2.0E-2torr, the two high-pressure aluminum sheet of chamber glow, directional ion flow generated would bombard the surface of the light to disperse gas of the surface and produce a very fine steel pits of the surface of parts in order to increase the adhesion of the aluminum layer and the surface of the part. After the pretreatment, continue to evacuation, when high vacuum reaches 5.0E-5torr, heat tungsten wire to melt and gasify the aluminum ring to aluminizing. The cavity is filled with silicone oil, and high vacuum converses to low vacuum, when pressure reaches 1.5E-2torr, glow generated by two high-pressure aluminum sheets would ionize silicone oil into Si02, then it would cover on the surface of the aluminum layer, in order to increase mechanical strength of aluminum the layer and prevent aluminum layer from being corroded and oxidized by air. The characteristics of aluminum machine evaporated aluminum tungsten heater comprising: tungsten wire is provided with a ring of aluminum with a purity of 99.99%, purity of tungsten wire is 99.99%.
4. Place the finished parts into the transporter and transfer them, and then inspect and pack the article by workers.
Tungsten Metals Supplier: Chinatungsten Online www.tungsten.com.cn | Tel.: 86 592 5129696; Fax: 86 592 5129797;Email:sales@chinatungsten.com |
Tungsten News & Prices, 3G Version: http://3g.chinatungsten.com | Molybdenum News & Molybdenum Price: http://news.molybdenum.com.cn |
Tungsten Heater Device that Cannot Deform under High-Temperature——Tungsten Wire
- Details
- Category: Tungsten Patents
- Published on Wednesday, 06 July 2016 16:16
- Written by xuejiao
- Hits: 5392
In large CVD(Chemical Vapor Deposition) system (diameter of the reaction chamber is longer than50cm), in order to form a large area and uniform film, using a large area and fence Czochralski tungsten wire to eliminate the uneven temperature and deformation problem of heating wire. But during film growth, large-scale CVD system usually have greater power and gas consumption, and when the arrangement of Czochralski tungsten wire, total current through the hot wire will be great, generally at 100 amperes or more. Therefore, it needs high current and high power hot wire heating transformer and a corresponding device for cooling systems. The device is relatively complex, which is not suitable for doing research for an experimental basis.
For the core heating section of tungsten heater, it can be improved by the following measures to solve the above problems.
1. Tungsten wire can be wounded into a flat ring, and it would be molded in a one time with a special material mold.
2. Using the high temperature boron nitride ceramic rod whose melting point is higher than 2400 ℃ to be fixed with tungsten wire.
3. Put and fix the boron nitride ceramic rod on the upper end of the electrode, so that the whole heating tungsten wire can keep parallel with the substrate surface.
4. Before using the new tungsten wire, it should be through the stress treatment.
After the new tungsten has being wounded and fixed, in an normal growth atmosphere, dong the annealing process for a long time at low temperatures to eliminate stress generated in the process of wound and stereotype.
The heating process is: every time the temperature of tungsten wire rises 100 ℃, then heating for 2 hours, until the temperature of tungsten wire reaches the growth temperature.
This is a specific improvement measures for the tungsten wire wound, this kind of tungsten heater device will greatly improve the efficiency of the subsequent coating.
Tungsten Metals Supplier: Chinatungsten Online www.tungsten.com.cn | Tel.: 86 592 5129696; Fax: 86 592 5129797;Email:sales@chinatungsten.com |
Tungsten News & Prices, 3G Version: http://3g.chinatungsten.com | Molybdenum News & Molybdenum Price: http://news.molybdenum.com.cn |
Advantages of Tungsten Heater for Aluminizing of Car Light
- Details
- Category: Tungsten Patents
- Published on Monday, 04 July 2016 16:20
- Written by xuejiao
- Hits: 5240
Car light is an important device for ensuring the driving safety, and it is also one of the most important outer parts. With the innovation of science and technology, and the rapid development of automobile industry, so the automotive lighting requirements are also getting higher and higher. Quality of reflector lamp directly affects the car's lighting effects. Conventional lights are made through molding, most of them use aluminizing method to the make reflector film to increase the reflectivity of the surface of the light. Domestic aluminizing technology includes ion bombardment, aluminizing, put on protective layer. In order to prevent the aluminum layer from oxidation and corrosion, these three aspects are carried out separately. Pretreatment relates to the adhesion of the aluminum layer, which affects the quality of the film, and the thickness of the protective layer and the aluminum layer have a certain influence in the quality of the lights. If the production cycle of aluminum is too long, it will increase the cost of production, and the quality of the protective layer becomes poor. Therefore, to solve this kind of problem is especially important.
This kind of aluminizing process with tungsten heater can make effect of component will be better in aluminizing, reducing the failure rate of aluminizing to some extent. Clean air molecules, water vapor and grease adsorbed on the surface of the base material of the lamp in pretreatment, and roughen the surface of the lamp, which can greatly improving the bonding strength the surface and the aluminum layer. In addition, transfer upper and lower parts by transporter can reduce dust pollution, which can improve the effect of the lights aluminizing. This process not only improves the quality of the protective layer, but also shortens the original production cycle of aluminizing from 26 minutes to 6 minutes, so it has reduced scrap rates and input costs for lights.
Tungsten Metals Supplier: Chinatungsten Online www.tungsten.com.cn | Tel.: 86 592 5129696; Fax: 86 592 5129797;Email:sales@chinatungsten.com |
Tungsten News & Prices, 3G Version: http://3g.chinatungsten.com | Molybdenum News & Molybdenum Price: http://news.molybdenum.com.cn |