Injection Molding Process
- Details
- Category: Tungsten Information
- Published on Friday, 06 October 2017 22:21
The cemented carbide injection molding process consists of the following steps: mixing, injection molding, derosination, sintering and subsequent processing. Any of these steps, if there is no control in place, there may be product defects, or even scrapped.
Cemented carbide powder is generally irregular, multi angle, fine particle size, large friction between the powders, low packing density, and large hardness of the powder, it is not prone to extrusion deformation. The proper mixture ratio and impurities in the raw material will have a great influence on the final properties of the products.
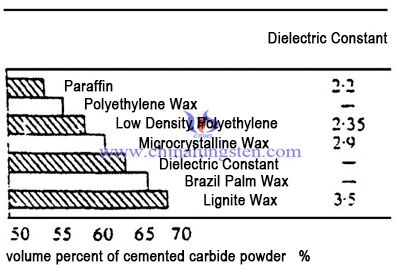
1, Composition Control
Cemented carbide powder is not easy to extrusion deformation. To maintain proper flowability and facilitate the injection molding process, the loading rate of the powder should be relatively low (i.e., the proportion of polymer in the mixture is relatively large).
Lower loading rate will lead to long degreasing time and difficult control of carbon content. On the other hand, it also brings great shrinkage coefficient, which leads to difficulty in controlling the size of sintered products. This needs to be weighed against the selection of loading rates.
Usually, low viscosity binders or appropriate amounts of surfactants such as stearic acid are used for improving flowability and wettability. Injection molding of cemented carbide is usually based on a thermoplastic binder system.
The organic binder consists of thermoplastic polymers (such as polyethylene, polypropylene, polystyrene, etc.) and waxes, resins and surfactants. Common compositions of cemented carbide powder are as follows.
2, Purity Control
If the powder is impure, such as sulfur, phosphorus, silicon and other elements, these materials will form pores and become defects during sintering. The oxygen content of cemented carbide powder cannot be too high, otherwise the product degreasing and sintering process occurs decarburization, producing η phase and reducing the mechanical properties of products.
After degreasing, the residual polymer binder will introduce carbon into the sintering process. Therefore, when choosing binders, we should select binders which have little ash and can be completely degreased.
- Tungsten Carbide Manufacturer & Supplier, Chinatungsten Online: tungsten-carbide.com.cn
- Tungsten News & Prices of China Tungsten Industry Association: www.ctia.com.cn
- Molybdenum News & Price: news.molybdenum.com.cn
- Tel.: 86 592 5129696; Fax: 86 592 5129797; Email: sales@chinatungsten.com