Injection Molding - Plasticizing Process
- Details
- Category: Tungsten Information
- Published on Friday, 29 September 2017 22:53
Powder metallurgy injection molding process includes feeding, plasticizing, injection, keeping pressure, cooling of parts, demoulding of parts and trimming of parts.
Definition: the polymer powder mixture is converted into a polymer viscous flow state by heating (externally heating, shearing, heating) in a cartridge, which has a certain fluidity and plasticity. The plasticizing process is the preparation process in the early stage of forming, also known as the pre-plastic process. Plasticizing quality and efficiency play an important role in the subsequent injection molding process and the quality of the products.
Requirement: MIM (powder injection molding) control of the plasticizing process is a requirement for the properties of the melt. Melting materials must have the following characteristics:
1, Materials needs to be completely melted. The organic polymer should become a viscous flow melt with fluidity at the temperature above the viscous flow regime.
2, No thermal decomposition occurs in the melt. The temperature cannot be higher than the thermal decomposition temperature of the component.
3, The material is fully mixed, the temperature distribution is uniform and no segregation exists.
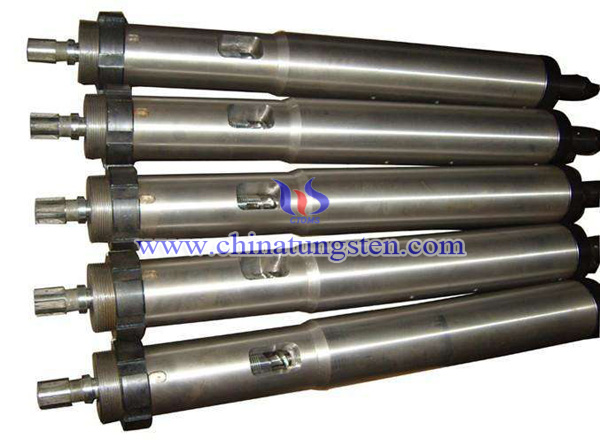
Measurement Index:
1, As important indexes to measure the plasticizing process, the homogeneity of material temperature and the uniformity of melt temperature affect the quality of the product directly. External heating of the barrel will produce a larger temperature gradient in the radial direction of the material. And then the temperature is homogenized by stirring and shearing of the screw.
2, Heating coefficient. It refers to the effective utilization rate of the barrel heating to measure the external heating efficiency. There are two sources of heat in the heating process. The first method is heated by an electric heating element outside the barrel. Materials in the barrel can produce a great temperature gradient in the direction of the cross section and the length of the material. The second method is that the material depends on the rotation of the screw and generates heat by shearing mechanism and friction mechanism (the plunger injection system does not have this process). Quantization as follows:
E=Tt-To/(Tl-To)
Where: E ... heating coefficient, should not be less than 0.8;
Tt... The temperature of the material after plasticization;
To... Initial temperature of Material;
Tl... Barrel temperature.
- Tungsten Carbide Manufacturer & Supplier, Chinatungsten Online: tungsten-carbide.com.cn
- Tungsten News & Prices of China Tungsten Industry Association: www.ctia.com.cn
- Molybdenum News & Price: news.molybdenum.com.cn
- Tel.: 86 592 5129696; Fax: 86 592 5129797; Email: sales@chinatungsten.com