Tungsten Powder and W-Cu Composite Powder
- Details
- Category: Tungsten Information
- Published on Thursday, 23 June 2016 17:59
Tungsten-copper (W-Cu) pseudoalloys are used in the manufacture of electrical contact materials and electrodes, thermal management devices such as heat sinks and spreaders, and conductive inks and pastes for ceramic metallization. The basic methods for the fabrication of articles composed of W-Cu pseudoalloys include: infiltration of a porous tungsten skeleton with liquid copper, hot pressing of blends of tungsten and copper powders, and various techniques incorporating liquid phase sintering, repressing, explosive pressing, and the like. Complex shapes may be made by injection molding W-Cu composite powders. It is desirable to be able to manufacture articles made from W-Cu pseudoalloys at or near the theoretical density of the pseudoalloy. Besides having improved mechanical properties, the higher density pseudoalloys have higher thermal conductivities which are critical for the application of W-Cu pseudoalloys as heat sink materials for the electronics industry.
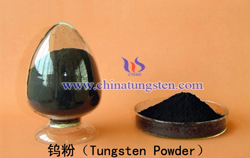
The components in the W-Cu system exhibit only a very small intersolubility. Thus, the integral densification of W-Cu pseudoalloys occurs above 1083°C in the presence of liquid copper. The compressive capillary pressure generated by the forming and spreading of liquid copper, the lubrication of tungsten particles by liquid copper and the minute solubility of tungsten in copper above 1200°C combine to cause the relative movement of tungsten particles during sintering and thereby make possible the displacement of tungsten particles. Local densification and rearrangement of the tungsten framework causes an inhomogenous distribution of W and Cu phases in the sintered article and copper bleedout, i.e. the loss of copper from the sintered article. This leads to the degradation of the thermal/mechanical properties of the sintered article.
Prior art methods directed to improving the homogeneity of W-Cu composite powders by coating tungsten particles with copper have not been successful as these copper-coated powders still exhibit a high tendency towards copper bleedout during the consolidation of the composite powder into fabricated shapes.
Thus, it would be advantageous to eliminate copper bleedout from occurring during the liquid-phase sintering of W-Cu pseudoalloys while providing a homogeneous distribution of W and Cu phases in the sintered article.
It is an object of the invention to obviate the disadvantages of the prior art.
It is another object of the invention to produce a W-Cu composite powder which can be used to make W-Cu pseudoalloys having high electrical and thermal conductivities.
It is a further object of the invention to produce a W-Cu composite powder which may be pressed and sintered to near theoretical density without copper bleedout.
It is still a further object of the invention to produce a W-Cu composite powder which may be used to make sintered articles having a high degree of dimensional control.
In accordance with one object the of invention, there is provided a tungsten-copper composite powder comprising individual particles having a tungsten phase and a copper phase wherein the tungsten phase substantially encapsulates the copper phase.
In accordance with another object of the invention, there is provided a W-Cu composite oxide powder comprising individual particles having a copper tungstate phase and tungsten trioxide phase wherein the tungsten trioxide phase exists primarily at the surface of the individual particles.
In accordance with a further object of the invention, there is provided a method for forming a homogeneous W-Cu pseudoalloy comprising pressing a tungsten-coated copper composite powder to form a compact and sintering the compact.
In accordance with a still further object of the invention, there is provided a W-Cu pseudoalloy having a microstructural cross-section having tungsten areas and copper areas, the tungsten areas being less than about 5 µm in size and the copper areas being less than about 10 µm in size.
Several factors influence the solid-state (below 1083°C - the melting point of copper) and liquid-phase (above the melting point of copper) sintering behavior of submicron W-Cu powder systems. Compacted refractory metal powders undergo considerable microstructural changes and shrinkage during solid-state sintering (in the absence of liquid phase). Submicron particle size powders effectively recrystallize and sinter at temperatures (T) which are much lower than the melting temperatures (Tm) of refractory metals (T ≅ 0.3 Tm). The initial sintering temperature for submicron (0.09-0.16 µm) tungsten powder is in the range of 900-1000°C. The spreading of copper and the formation of a monolayer copper coating on tungsten particles occurs in the temperature range of 1000-1083°C. By lowering the activation energy for tungsten diffusion, monolayer copper coatings activate the solid-state sintering of tungsten. Therefore, a number of complementary conditions are met for bonding submicron tungsten particles into a rigid tungsten framework within the composite powder compact during solid-state sintering (950-1080°C). High fineness and homogeneity of the starting composite powders are expected to enhance the sintering of a structurally homogeneous tungsten framework. Such framework should, in turn, aid in making a homogeneous pseudoalloy.
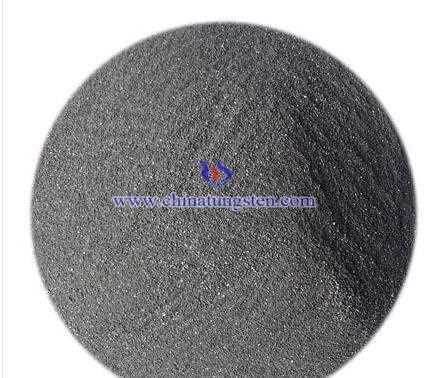
Tungsten Powder Supplier: Chinatungsten Online tungsten-powder.com | Tel.: 86 592 5129696; Fax: 86 592 5129797;Email:sales@chinatungsten.com |
Tungsten News & Prices, 3G Version: http://3g.chinatungsten.com | Molybdenum News & Molybdenum Price: http://news.molybdenum.com.cn |