Tungsten Carbide Dies for Cold Heading
- Details
- Category: Tungsten Information
- Published on Friday, 06 July 2018 16:54
Tungsten carbide dies used in production of threaded fasteners has longer service life than any other dies for carbon tool steel and high carbon high alloy steel. Therefore, it has been widely applied in the production of cold screws such as screws under small specifications of MS. Compared with foreign tungsten carbide dies, there is a clear gap between Chinese and foreign dies. For example: tungsten carbide dies for semicircular head screws or countersunk cross groove screws, the life of Japanese die can reach 700 to 9 million pieces, while die life in China is 200 to 3 million pieces, and the quality is not stable.
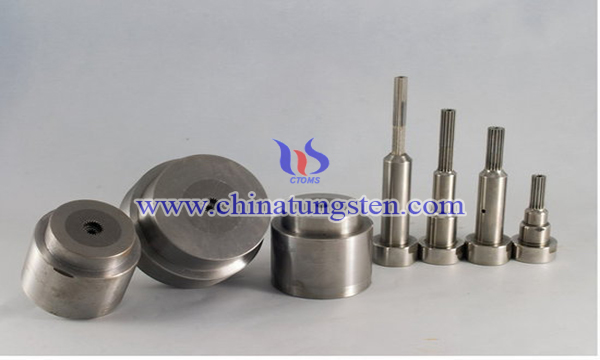
In contrast, there are many differences. The inner hole of the mold sleeve and the outer core of the mold core are all cylindrical in the Chinese manufacturers. The bottom of the mold core and the bottom of the inner hole of the mold sleeve are all flat, of which the structure is simple and easy to process. When the cold setting is used, because of the undirected angle, it is easily pressed and distorted. And the inner hole surface of the mold sleeve is squeezed, even the mold core will produce micro crack and crack, so that the quality of the press insert is difficult to be stable.
The contact parts of the inner hole and mold core of the mold sleeve designed by the Japanese manufacturer adopt the structure of double taper and biconcave, of which the shape is complex, and the processing is difficult. However, the guiding angle is conducive to ensuring the quality of the Press inlay. What’s more, the bottom of the mold core is in contact with the bottom of the inner hole of the mold sleeve, and uses a double convex surface structure, which is beneficial to the central part of the maximum force.
In terms of die hardness, Chinese manufacturers choose YG20C, Cr12MoV, Cr12, while Japanese manufacturers choose YG15. The former is slightly higher in strength and slightly lower in hardness. The latter is the opposite. Because of its high hardness and good wear resistance, this is another reason for the long service life of Japanese dies.
Under the same conditions, when the interference coefficient is small (large), the preload force is small. The failure phenomenon of the mold core out of the mold produced by the Chinese manufacturers may be related to the smaller interference coefficient or the unqualified size. Japanese manufacturers adopt conical cold pressing fit, of which the interference coefficient is 0.85%. Compared with the 1.3%~1.5% used in Russia, it is relatively low. The quality of the surface grinding and polishing of the mould core of the Chinese manufacturers is poor. Surface grinding and throwing quality of the Japanese manufacturers is better, the whole surface roughness is Ra0.32~Ra0.16um, even Ra0.08um.
The roughness of the outer surface of the mold core has an effect on the life of the die. Poor surface roughness, especially the existence of a concave, hole or crack on the surface, will be the point of origin of pressure concentration and fracture, which will cause premature cracking and failure of the core.
- Tungsten Carbide Manufacturer & Supplier, Chinatungsten Online: tungsten-carbide.com.cn
- Tungsten News & Prices of China Tungsten Industry Association: www.ctia.com.cn
- Molybdenum News & Price: news.molybdenum.com.cn
- Tel.: 86 592 5129696; Fax: 86 592 5129797; Email: sales@chinatungsten.com