Effect of EDM on Tungsten Carbide Dies
- Details
- Category: Tungsten Information
- Published on Monday, 09 April 2018 17:42
With the continuous improvement of the specialized production degree of electronic, computer, instrument, motor and household appliances, the requirements for the life and precision of the die have become more and more high, making the tungsten carbide becoming more and more popular in the field of mold production. However, the high hardness and high wear resistance of tungsten carbide make it difficult for conventional machining methods to process it.
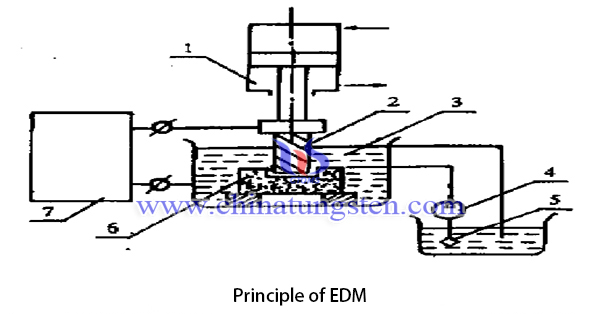
At present, the processing technology of tungsten carbide in mould manufacturing mainly includes wired cutting, diamond grinding and electric discharge machining(EDM). Because the application model of grinding is restricted by the structure, shape and grinding force of the parts, the small holes, narrow grooves and special-shaped mold parts of some hard alloys can only be machined by EDM. It is of practical significance to study the technological characteristics of EDM and improve the machining efficiency of tungsten carbide dies.
The effect of EDM on tungsten carbide dies is that the EDM cavity is subjected to high temperature of up to 10000 ℃ and the cooling effect of liquid medium at the moment of discharge, which will affect the chemical composition and physical mechanical properties of the EDM. In the surface layer, there will be changes in microstructure and grain, as well as carburization (working fluid), impermeable metal (copper tungsten electrode), microcrack, porosity and inclusion loose and so on.
The thickness of the surface influence layer is the largest relation to the pulse discharge energy. So, the wider the pulse width and the larger the current peak, the more intense the influence is. In addition, if the processing stability is not good, such as the medium oil is dirty, the mold is not magnetic (the hard alloy has ferromagnetic material in the hard alloy), flushing the oil road is not smooth or unformed loop (that is, the dirty objects are reciprocating in the processing area), the phenomenon of suspended matter to be discharged at two times in the processing area will occur. Finally, excessive heat propagates into the tungsten carbide, which causes internal stress, and causes defects such as microcracks. The thickness of the impact layer of the EDM can be less than 0.01 mm, and even larger than 0.5mm.
In EDM, the quality of electrodes is also very important. The electrode material should be evenly distributed, the electrode material will be modeled on the mold, and the outer surface should be circular arc to avoid sharp corner discharge. It is advisable to one-time molding when processing a mold, in order to avoid uneven discharge and uneven discharge due to poor repeatability of each electrode. Additionally, in order to keep the light after the electric machining, full polishing can completely eliminate the influence layer of the electric machining and can eliminate the scar mark (fatigue crack is often produced from the place and spread along the intersection of the two surfaces).
From the analysis, it can be seen that the selection of electric pulse, the cleaning of electrolyte and the uniformity of material have a direct influence on the life of the carbide die after EDM. The wider the electric pulse is used, the more the defects produced in the processing die, the lower the service life of the die; the dirtier the electrolyte, the easier to produce the blue arc discharge, which causes the workpiece to burn and produce microcracks and reduce the service life of the parts.
- Tungsten Carbide Manufacturer & Supplier, Chinatungsten Online: tungsten-carbide.com.cn
- Tungsten News & Prices of China Tungsten Industry Association: www.ctia.com.cn
- Molybdenum News & Price: news.molybdenum.com.cn
- Tel.: 86 592 5129696; Fax: 86 592 5129797; Email: sales@chinatungsten.com