Siphon Degreasing Process
- Details
- Category: Tungsten Information
- Published on Monday, 06 November 2017 22:43
Siphon degreasing in extrusion injection molding is a new degreasing process. Because of its fast degreasing speed and free from the influence of debinding atmosphere, it has become a hot spot in the research of tungsten carbide degreasing process.
Because of its own defects, such as easy to absorb material and easy to remove, it is seldom used at present. Two step degreasing process with siphon degreasing and thermal degreasing is generally adopted. Debinding is the most time-consuming and difficult to control step in cemented carbide injection molding.
In the debinding process, the forming blank is prone to macro or micro defects, so degreasing process is very important to ensure the quality of cemented carbide products. Siphon degreasing process generally use solid paraffin and low molecular weight (PW) as the matrix binder system, green on the siphon material, slow heating organic matter and let melting material suction siphon.
1, Influence of Siphon Temperature on Debinding Rate
The siphon temperature is an important factor affecting the degreasing rate of the siphon, which is determined by the binder system used, and the effect of temperature on the removal rate of PW is shown in the following picture.
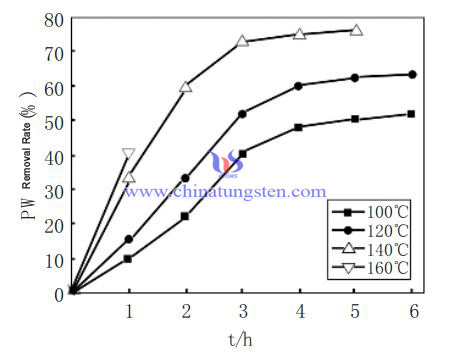
As time goes on, the PW removal rate curve first increases significantly, then tends to be gentle. The higher the temperature is, the higher the debinding rate is, but the deformation of the formed blank is serious at high temperature. When the temperature is too high, the softening of the polymer caused the skeleton, and the deformation of the formed blank under the action of deadweight.
2, Influence of Siphon Time on Removal Rate of PW
At different temperatures, with the extension of time, the removal rate of PW showed a rapid increase at the beginning, and then slowly increased, and finally tended to be gentle. The higher the temperature, the final degreasing rate will increase. After that, the removal rate of PW increases with the increase of siphon time.
3, Influence of Siphon Degreasing on Thermal Debinding
Without debinding, the formed billet needs longer degreasing time during thermal debinding. Part PW siphonage debinding has been removed, the blank inside has initially formed a small hole, which escape for the subsequent heat debinding process of the gas in the provided path and effectively avoid the defects.
For the direct thermal debinding, when the heating rate is too fast, the gas produced by evaporation and decomposition of PW cannot escape as soon as possible. When the pressure exceeds the strength of the blank will be generated when the bubble and crack.
- Tungsten Carbide Manufacturer & Supplier, Chinatungsten Online: tungsten-carbide.com.cn
- Tungsten News & Prices of China Tungsten Industry Association: www.ctia.com.cn
- Molybdenum News & Price: news.molybdenum.com.cn
- Tel.: 86 592 5129696; Fax: 86 592 5129797; Email: sales@chinatungsten.com