Characteristics of Tungsten-Nickel-Iron Alloy
- Details
- Category: Tungsten Information
- Published on Friday, 04 July 2025 14:53
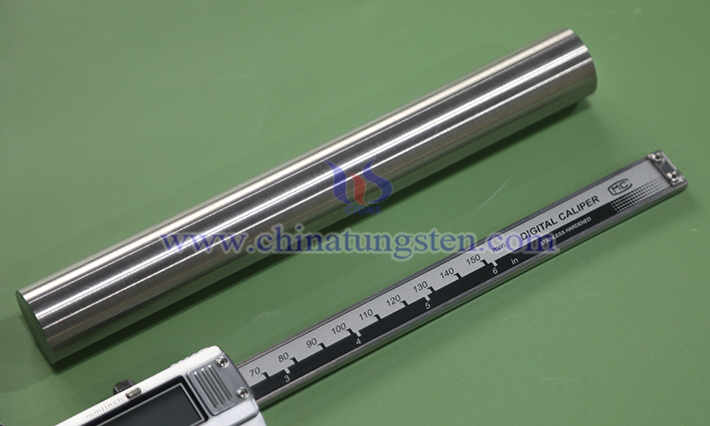
Tungsten-nickel-iron alloy is a high-density alloy with tungsten as the base (typically 80%–98% tungsten content), incorporating nickel, iron, and other elements. It boasts a range of unique physical, chemical, and mechanical properties, finding wide use in aerospace, defense, medical devices, and industrial manufacturing.
Can Chrome Plating on Tungsten Alloy Surfaces Improve Corrosion Resistance?
- Details
- Category: Tungsten Information
- Published on Thursday, 03 July 2025 13:52
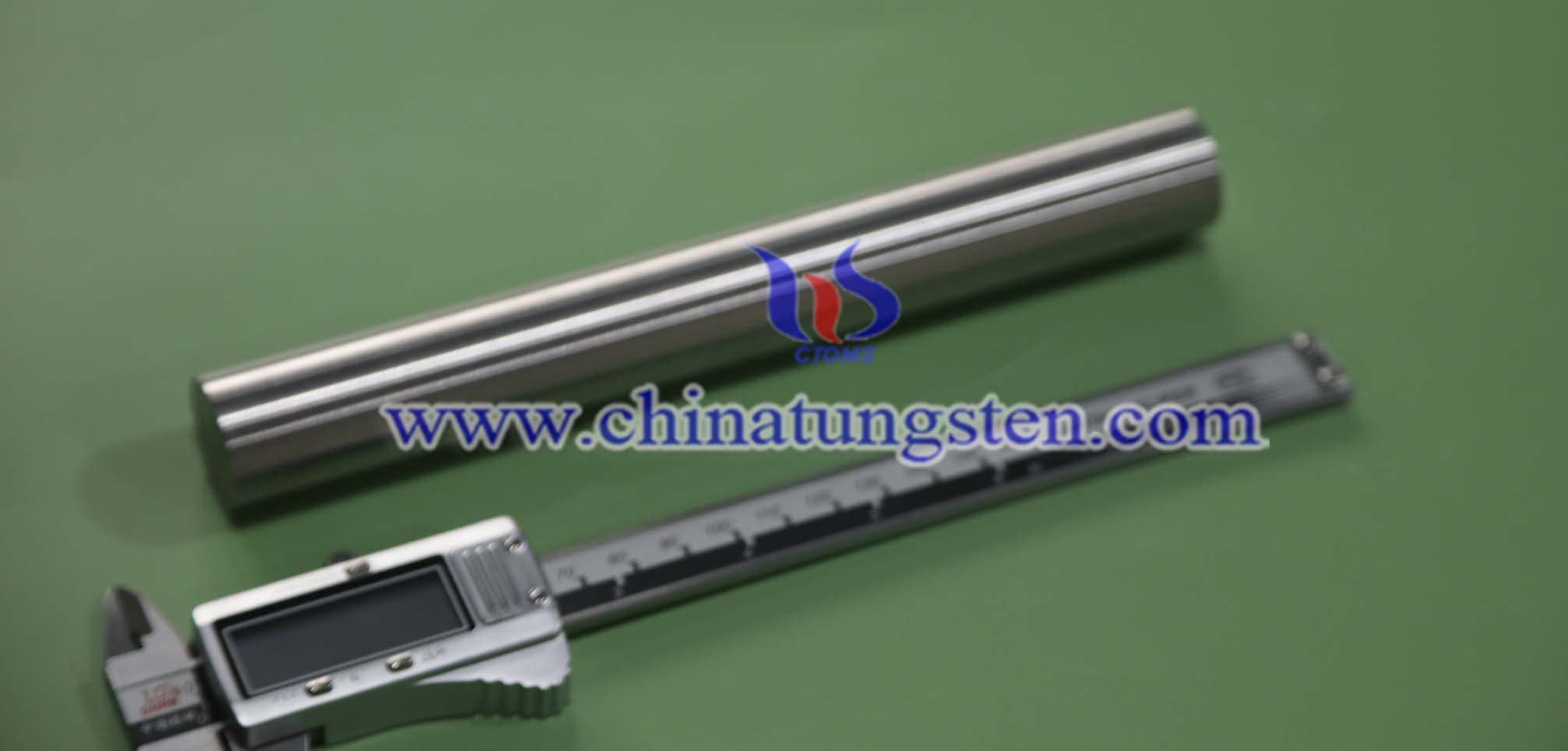
Chrome plating on tungsten alloy surfaces can greatly enhance corrosion resistance. This is a common surface engineering technique used to improve durability and decorative appearance.
1. Basic Principle of Chrome Plating
Chrome plating—primarily referring to hard chrome plating—is an electrochemical process that deposits a dense chromium (Cr) layer on the surface of a metal. This chromium layer features:
- High hardness (HV800~HV1000)
- Excellent wear resistance and low friction coefficient
-
Good chemical stability and oxidation resistance
Applications of Tungsten Alloy Counterweight Blocks in the Automotive Field
- Details
- Category: Tungsten Information
- Published on Thursday, 03 July 2025 11:47
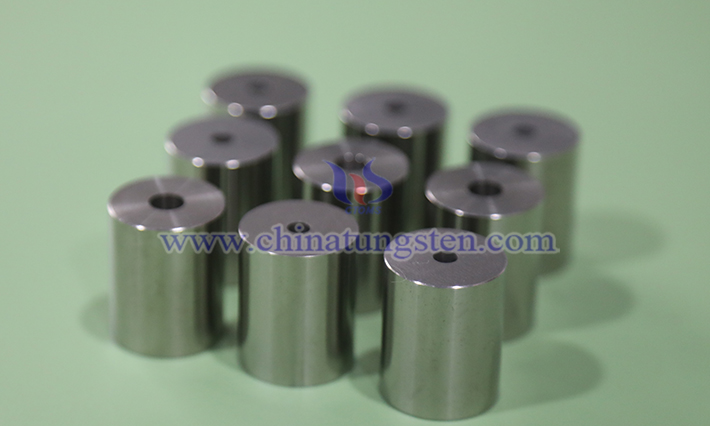
High-density tungsten alloy, a functional material with tungsten as its base (85%–99%) combined with metals like nickel, iron, and copper through powder metallurgy sintering, boasts a density of 16–18.5 g/cm³ along with high strength, wear resistance, and corrosion resistance. In the automotive field, its core advantages as a counterweight block include precise weight adjustment in a small volume, minimizing space usage; strong chemical stability to withstand the high temperatures and humidity of engine compartments; and eco-friendliness, aligning with global automotive industry green standards.
What Is Zinc Tungstate?
- Details
- Category: Tungsten Information
- Published on Thursday, 03 July 2025 11:44
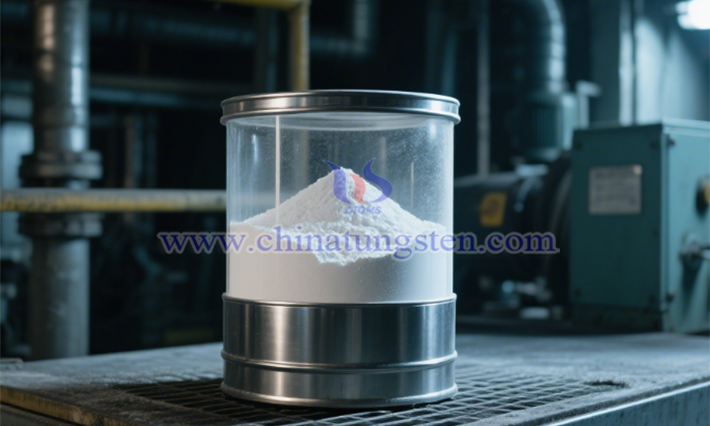
Zinc tungstate (Tungsten Zinc, ZnWO₄), also known as zinc tungsten oxide, belongs to the tungstate family. It is formed by the chemical bonding of palent zinc ions (Zn²⁺) and tungstate ions [(WO₄)²⁻], resulting in a wolframite-type crystal structure. In semiconductor research, its photoelectric properties and catalytic activity offer new possibilities for developing novel optoelectronic devices and environmental purification materials, demonstrating significant application potential in energy and environmental fields.
What Is Potassium Tungstate?
- Details
- Category: Tungsten Information
- Published on Thursday, 03 July 2025 11:41
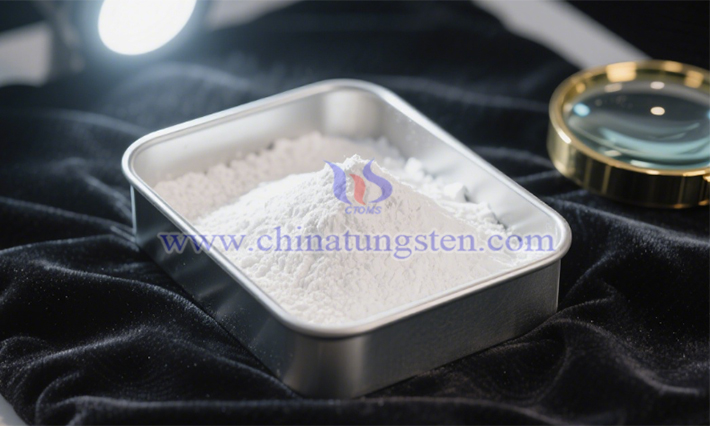
Compared to sodium tungstate, potassium tungstate (K₂WO₄) exhibits distinct solubility and chemical reactivity due to the introduction of K⁺ ions. From its role as an intermediate in metallic tungsten production to its function as an additive in photovoltaic cell electrolytes, this compound leverages an intrinsic logic of "ionic properties-crystal structure-application" to build perse application scenarios in energy, materials, and analytical chemistry.
What Is Calcium Tungstate?
- Details
- Category: Tungsten Information
- Published on Thursday, 03 July 2025 11:37
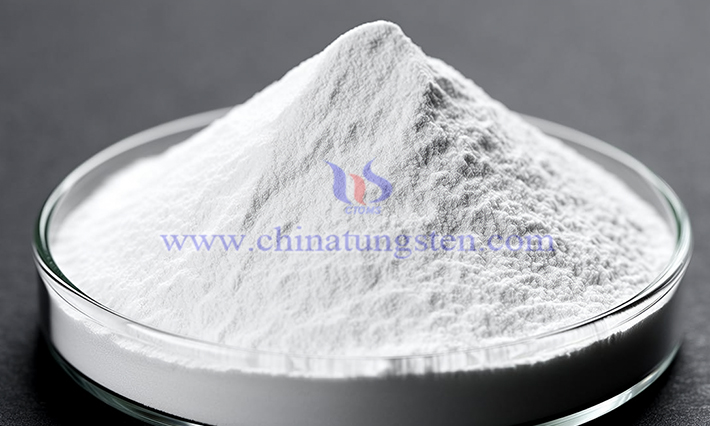
Compared to alkali metal tungstates (e.g., sodium tungstate and potassium tungstate), calcium tungstate (CaWO₄) exhibits markedly different crystal structures and properties due to the incorporation of Ca²⁺, evolving from its industrial designation as "synthetic scheelite" to its core application as a scintillator material.
What Is Magnesium Tungstate?
- Details
- Category: Tungsten Information
- Published on Thursday, 03 July 2025 11:35
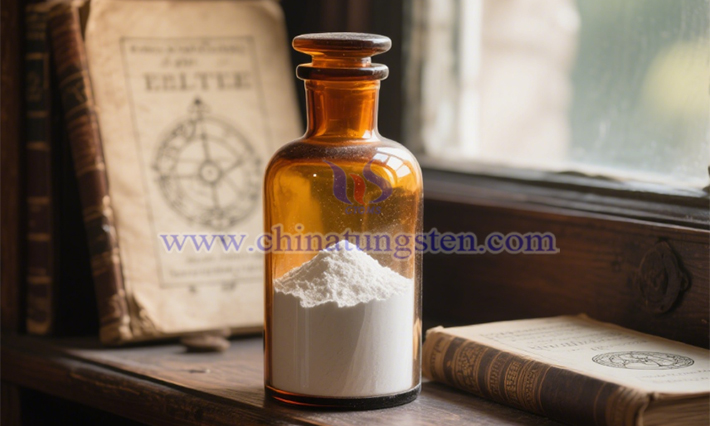
Within the family of inorganic functional materials, magnesium tungstate (MgWO₄) stands out as a representative alkaline earth metal tungstate, leveraging its unique crystal structure and perse properties to deliver significant value in optoelectronic displays, catalytic degradation, and functional ceramics. This compound, formed by magnesium ions (Mg²⁺) and tungstate ions [(WO₄)²⁻], inherits the stability of alkaline earth metals while gaining rich optical and electrical responses from the tungsten-oxygen framework, serving as a bridge between traditional chemistry and emerging optoelectronic technologies.
What Is Ferrous Tungstate?
- Details
- Category: Tungsten Information
- Published on Thursday, 03 July 2025 11:32
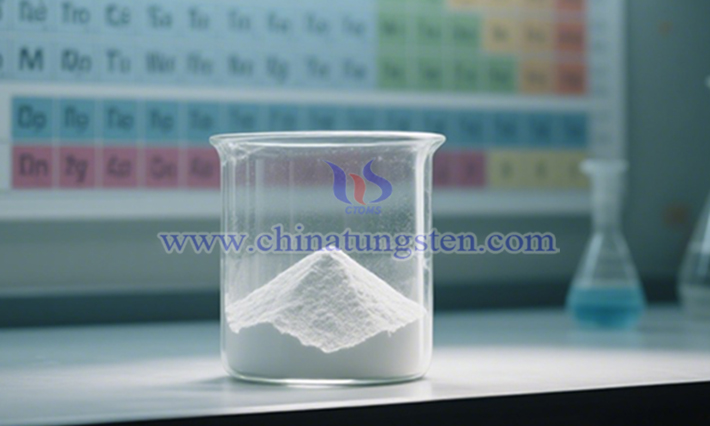
Within the broad field of transition metal compounds, ferrous tungstate (FeWO₄) stands out as a representative example of an iron-group element combined with tungstate, gaining prominence in chemical and materials science research due to its unique physicochemical properties and versatile application potential. This tungstate, formed by Fe²⁺ and (WO₄)²⁻, not only inherits the magnetic commonality of iron-group elements but also exhibits rich functional characteristics due to the introduction of the tungsten-oxygen framework, opening new pathways in catalysis, energy storage, and inorganic material preparation.
Tungsten Wire for Defrosting Glass
- Details
- Category: Tungsten Information
- Published on Wednesday, 02 July 2025 19:03
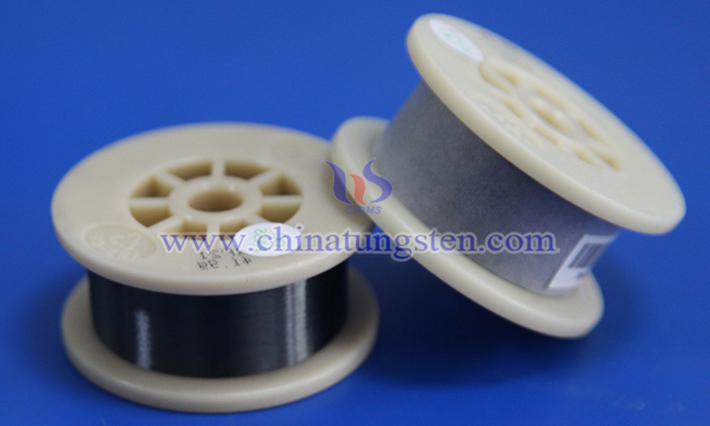
Defrosting glass usually uses tungsten wire as a heating element because tungsten has a high melting point, high temperature resistance and good conductivity, which is suitable for generating uniform heat on the glass surface or in the interlayer to remove frost or ice.
Tungsten Wire for Anti-fog Glass
- Details
- Category: Tungsten Information
- Published on Wednesday, 02 July 2025 19:01
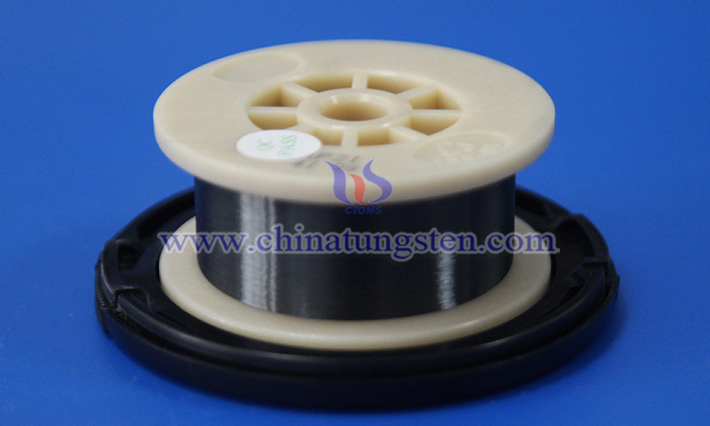
Anti-fog glass usually prevents fog condensation by embedding or coating a conductive material (such as tungsten wire or conductive film) on the glass surface and heating it with electricity. Tungsten wire is often used as a heating element in anti-fog glass systems that require heating, such as car rearview mirrors, bathroom mirrors or refrigerator glass doors, due to its high melting point, high resistivity, high temperature resistance and corrosion resistance.