Tungsten Trioxide Denitration Catalyst Applies High Temperature Flue Gas Denitration
- Details
- Category: Tungsten Information
- Published on Monday, 13 June 2016 18:31
90% of the NOx in the flue gas exists in the form of NO. The denitration and desulfurization technologies of coke oven flue gas are namely four, which shows as bellows: integration process of sodium carbonate semidry desulfurization + low temperature denitration; coke oven flue gas heating + high temperature catalytic reduction denitration process; SICS Catalytic Oxidation (Organic Catalysis Method) desulfurization and denitrification process; activated carbon desulfurization and denitrification process. Wherein the principle of coke oven flue gas heating + high temperature catalytic reduction denitration process is under the present of tungsten trioxide de-NOx catalyst, the NOx in the flue gas reacts with the injected ammonia to occur the reduction reaction, and finally generate N2 and H2O, to achieve the goal of NOx removal. Generally, the reaction temperature is controlled at among 290~420 ℃.
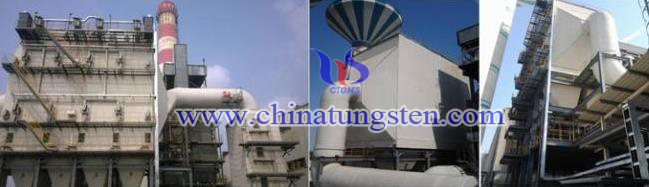
The process that tungsten trioxide denitration catalyst plays a role in coke oven flue gas is as follows:
1. Use the Master original flue exhaust fan from the coke oven flue always leads through the GGH heat exchanger or furnace heated to 320 ℃ (The heating furnace is heated with the coke oven gas.);
2. The heated flue gas enters the SCR reactor, under the effect of tungsten trioxide denitration catalyst the gas will have a selective reduction reaction with the added denitration agent - liquid ammonia, to achieve purpose of efficient denitration;
3. The clean flue gas after denitration enters the GGH (flue gas - flue gas reheater), the clean flue gas comes out from GGH will go through the waste heat boiler for heating cold water to achieve the effect of heat recovery, and finally exhaust to the atmosphere through the chimney.
Generally, in the process of high temperature denitrification of tungsten trioxide denitration catalyst, the optimum reaction temperature is 350°C, the efficiency can reach to 70%, which meets emission standards of 150mg/m3; in addition, its denitration efficiency is quite stable, and has more stable removal ability for low NOx emissions; moreover, the setting up of GGH makes the energy exchange between the cleaned high temperature (350°C) flue gas outlet from the purification SCR and relatively low temperature (180°C) of oven raw tobacco gas coming true, to enhance the original coke oven flue gas temperature, reducing fuel consumption and greatly reduce system power consumption.
Tungsten Oxide Supplier: Chinatungsten Online www.tungsten-oxide.com | Tel.: 86 592 5129696; Fax: 86 592 5129797;Email:sales@chinatungsten.com |
Tungsten News & Prices, 3G Version: http://3g.chinatungsten.com | Molybdenum News & Molybdenum Price: http://news.molybdenum.com.cn |