影响三氧化钨光电转换的因素
- 详细资料
- 分类:钨业知识
- 发布于 2015年12月28日 星期一 17:47
- 点击数:1129
氧化钨供应商:中钨在线科技有限公司 | 产品详情: http://www.tungsten-oxide.com |
电话:0592-5129696 传真:5129797 | 电子邮件:sales@chinatungsten.com |
钨钼文库:http://i.chinatungsten.com | 钨钼图片: http://image.chinatungsten.com |
钨新闻3G版:http://3g.chinatungsten.com | 钼业新闻: http://news.molybdenum.com.cn |


石墨烯与氧化钨复合薄膜2/2
- 详细资料
- 分类:钨业知识
- 发布于 2015年12月28日 星期一 17:44
- 点击数:766
氧化钨供应商:中钨在线科技有限公司 | 产品详情: http://www.tungsten-oxide.com |
电话:0592-5129696 传真:5129797 | 电子邮件:sales@chinatungsten.com |
钨钼文库:http://i.chinatungsten.com | 钨钼图片: http://image.chinatungsten.com |
钨新闻3G版:http://3g.chinatungsten.com | 钼业新闻: http://news.molybdenum.com.cn |


石墨烯与氧化钨复合薄膜1/2
- 详细资料
- 分类:钨业知识
- 发布于 2015年12月28日 星期一 17:42
- 点击数:987
氧化钨供应商:中钨在线科技有限公司 | 产品详情: http://www.tungsten-oxide.com |
电话:0592-5129696 传真:5129797 | 电子邮件:sales@chinatungsten.com |
钨钼文库:http://i.chinatungsten.com | 钨钼图片: http://image.chinatungsten.com |
钨新闻3G版:http://3g.chinatungsten.com | 钼业新闻: http://news.molybdenum.com.cn |


仲钨酸铵生产工艺流程的分析 3/3
- 详细资料
- 分类:钨业知识
- 发布于 2015年12月28日 星期一 17:37
- 点击数:1038
仲钨酸按供应商:中钨在线科技有限公司 | 产品详情: ammonium-paratungstate.com |
电话:0592-5129696 传真:5129797 | 电子邮件:sales@chinatungsten.com |
钨钼文库:http://i.chinatungsten.com | 钨钼图片: http://image.chinatungsten.com |
钨新闻3G版:http://3g.chinatungsten.com | 钼业新闻: http://news.molybdenum.com.cn |


仲钨酸铵生产工艺流程的分析 2/3
- 详细资料
- 分类:钨业知识
- 发布于 2015年12月28日 星期一 17:26
- 点击数:1138
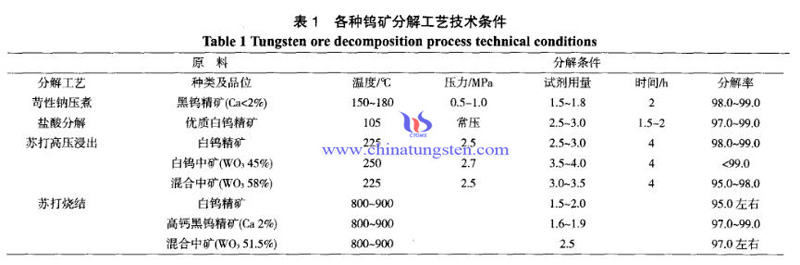
仲钨酸铵生产工艺流程的分析1/3,请见http://news.chinatungsten.com/cn/tungsten-information/81815-ti-10605。
仲钨酸按供应商:中钨在线科技有限公司 | 产品详情: ammonium-paratungstate.com |
电话:0592-5129696 传真:5129797 | 电子邮件:sales@chinatungsten.com |
钨钼文库:http://i.chinatungsten.com | 钨钼图片: http://image.chinatungsten.com |
钨新闻3G版:http://3g.chinatungsten.com | 钼业新闻: http://news.molybdenum.com.cn |


仲钨酸铵生产工艺流程的分析 1/3
- 详细资料
- 分类:钨业知识
- 发布于 2015年12月28日 星期一 17:15
- 点击数:981
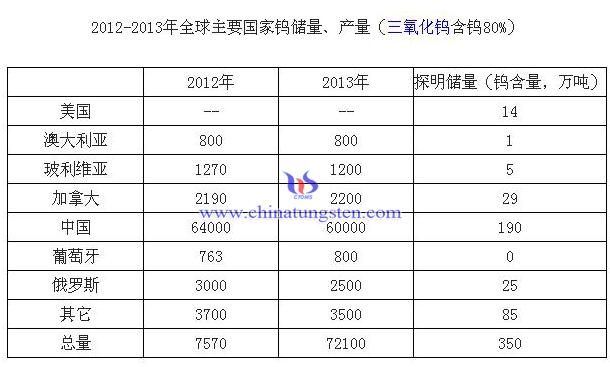
仲钨酸按供应商:中钨在线科技有限公司 | 产品详情: ammonium-paratungstate.com |
电话:0592-5129696 传真:5129797 | 电子邮件:sales@chinatungsten.com |
钨钼文库:http://i.chinatungsten.com | 钨钼图片: http://image.chinatungsten.com |
钨新闻3G版:http://3g.chinatungsten.com | 钼业新闻: http://news.molybdenum.com.cn |


三氧化钨简介3/3
- 详细资料
- 分类:钨业知识
- 发布于 2015年12月28日 星期一 15:44
- 点击数:1289
五.三氧化钨 - 制备
由钨精矿与氢氧化钠或苏打高温熔融、或高温压煮制成钨酸钠溶液,再经离子交换或萃取提纯、蒸发工艺制得仲钨酸铵晶体,再经700℃煅烧制得三氧化钨。如果是以白钨精矿为原料,也可用盐酸分解制成钨酸,,再经氨溶、蒸发工艺制得仲钨酸铵晶体,然后经700℃煅烧制得三氧化钨。也可直接煅烧钨酸制得三氧化钨。其主要反应式如下:
FeWO4+4NaOH→2Na2WO4+Fe(OH)2
MnWO4+4NaOH→2Na2WO4+Mn(OH)2
CaWO4+2HCI=H2WO4+CaCI2
H2WO4+2NH4(OH)=(NH4)2WO4+2H2O
12Na2WO4+14HCl→5Na2O·12WO3+14NaCl+7H2O
5Na2O·12WO3+10NH4Cl→5(NH4)2O·12WO3+10NaCl
5(NH4)2·12WO3+10HCl+7H2O→12H2WO4+10NH4Cl
H2WO4→WO3+H2O
5(NH4)2O-12WO3-6H2O →12WO3+10NH3↑+11H2O
六.三氧化钨 –检验
称取0.5g试样,精确至0.000 2g,置于250mL高型烧杯中加入氨水溶液40mL,盖上表面皿,在低温电炉上加热,使溶液保持近沸腾状态,边加热边搅拌至试样完全溶解,取下冷却至室温后加入盐酸10mL,小心煮沸后置于沸水浴上蒸发浓缩至体积约10mL。用70℃温水将上述溶液稀释至70mL~80mL,在不断搅拌下加入盐酸辛可宁溶液10mL,置于水浴(70℃±5℃)上保温1h,每隔20min搅拌一次,用倾泻法过滤溶液(用11cm定量慢速滤纸),玻璃棒及烧杯壁上附着的沉淀用定量慢速滤纸擦净,沉淀物用盐酸辛可宁洗液洗涤多次,控制滤液和洗液体积为180mL左右。
将沉淀和滤纸移入一已恒重的铂坩埚中,在电炉上小心灰化后置于高温炉(750℃)中灼烧10min,取出,冷却至室温后加入3mL~5mL氢氟酸及数滴硫酸,于沸水浴上蒸至近干后移至电炉上加热,使冒尽白烟,再置于高温炉(750℃)中灼烧30min,取出,置于干燥器内冷却至室温,称重,反复几次直至恒重。
注:用氨水溶解试样时,应尽量避免令溶液剧烈沸腾,减少氨水的挥发。若经长时间溶解后溶液始终显得浑浊或有残渣,应用定量滤纸过滤,然后用温热的氨水[1.5%(m/m)]多次充分洗涤烧杯和滤纸,集齐滤液和洗液继续余下的实验。
结果的表述
三氧化钨含量以质量百分数表示,按公式计算:
X(%)=(m1-m2)÷m0
式中:X—三氧化钨的质量百分含量,%;
m0—坩埚的质量,g;
m1—坩埚和沉淀的质量,g;
m2—试样质量,g;
取两次测定的平均值,结果保留二位小数;
精密度r=0.25%;R=0.42%。
氧化钨供应商:中钨在线科技有限公司 | 产品详情: http://www.tungsten-oxide.com |
电话:0592-5129696 传真:5129797 | 电子邮件:sales@chinatungsten.com |
钨钼文库:http://i.chinatungsten.com | 钨钼图片: http://image.chinatungsten.com |
钨新闻3G版:http://3g.chinatungsten.com | 钼业新闻: http://news.molybdenum.com.cn |


三氧化钨简介2/3
- 详细资料
- 分类:钨业知识
- 发布于 2015年12月28日 星期一 15:27
- 点击数:942
四.三氧化钨 - 使用注意事项
1.健康危害:低毒。对眼睛、皮肤有刺激性。熔炼钨钢工人出现全身无力、发热,麻疹样皮疹、蛋白尿,可能与熔炼时吸入三氧化钨有关。
2.燃爆危险:该品不燃,具刺激性。
3.急救措施
皮肤接触:脱去污染的衣着,用大量流动清水冲洗。
眼睛接触:提起眼睑,用流动清水或生理盐水冲洗。
吸入:迅速脱离现场至空气新鲜处。保持呼吸道通畅。如呼吸困难,给输氧。如呼吸停止,立即进行人工呼吸。
食入:饮足量温水,催吐。
4.消防措施
危险特性:与卤素化合物如五氟化溴、三氟化氯发生剧烈反应。
有害燃烧产物:有害的毒性烟气。
灭火方法:消防人员必须穿全身防火防毒服,在上风向灭火。灭火时尽可能将容器从火场移至空旷处。然后根据着火原因选择适当灭火剂灭火。
泄漏应急处理
5.应急处理:隔离泄漏污染区,限制出入。建议应急处理人员戴防尘口罩,穿一般作业工作服。不要直接接触泄漏物。
6.小量泄漏:避免扬尘,小心扫起,收集于干燥、洁净、有盖的容器中。
7.大量泄漏:收集回收或运至废物处理场所处置。
操作处置与储存
8.操作注意事项:密闭操作,局部排风。防止粉尘释放到车间空气中。操作人员必须经过专门培训,严格遵守操作规程。建议操作人员佩戴自吸过滤式防尘口罩,戴化学安全防护眼镜,穿橡胶耐酸碱服,戴橡胶耐酸碱手套。避免产生粉尘。避免与五氟化溴、三氟化氯接触。配备泄漏应急处理设备。倒空的容器可能残留有害物。
9.储存注意事项:储存于阴凉、通风的库房。远离火种、热源。防止阳光直射。包装密封。应与五氟化溴、三氟化氯分开存放,切忌混储。储区应备有合适的材料收容泄漏物。
氧化钨供应商:中钨在线科技有限公司 | 产品详情: http://www.tungsten-oxide.com |
电话:0592-5129696 传真:5129797 | 电子邮件:sales@chinatungsten.com |
钨钼文库:http://i.chinatungsten.com | 钨钼图片: http://image.chinatungsten.com |
钨新闻3G版:http://3g.chinatungsten.com | 钼业新闻: http://news.molybdenum.com.cn |


三氧化钨简介 1/3
- 详细资料
- 分类:钨业知识
- 发布于 2015年12月28日 星期一 14:56
- 点击数:1666
三氧化钨是一种黄色粉末。不溶于水,溶于碱液,微溶于酸,用于制高熔点合金和硬质合金,制钨丝和防火材料等。可由钨矿与纯碱共熔后加酸而得。三氧化钨的结构取决于温度:它在740°C以上为四方晶系;330-740°C为正交晶系;17-330°C为单斜晶系;-50-17°C为三斜晶系。三氧化钨主要用于煅烧还原生产钨粉和碳化钨粉,进而用于生产硬质合金产品,如刀具和模具的制造。由钨精矿与氢氧化钠或苏打高温熔融、或高温压煮制成钨酸钠溶液,再经离子交换或萃取提纯、蒸发工艺制得仲钨酸铵晶体,再经700℃煅烧制得三氧化钨。
中文名称:三氧化钨
中文别名:钨酸酐;氧化钨(VI)
英文名:Tungsten trioxide
一.三氧化钨 - 理化性质
1. 物理性质
三氧化钨结构式
熔点(℃):1472
相对密度(水=1):7.16
沸点(℃):1837
分子式:WO3
分子量:231.85
溶解性:不溶于水,溶于碱,微溶于酸
2. 化学性质
850℃时显着升华;几乎不与除氢氟酸外的无机酸反应,能缓慢地溶于氨水或浓碱溶液。与氯气加热反应生成氯氧化物,但不能与溴、碘反应。三氧化钨的结构取决于温度:它在740°C以上为四方晶系、330-740°C为正交晶系、17-330°C为单斜晶系、-50-17°C为三斜晶系。单斜的结构最常见,其空间群为P21/n。
二.三氧化钨 - 规格
三.三氧化钨 - 作用与用途
三氧化钨主要用于煅烧还原生产钨粉和碳化钨粉,进而用于生产硬质合金产品,如刀具和模具的制造。同时也可用于制造纯钨制品、钨条、钨丝,钨电极;和用途配重和辐射的屏蔽材料。工业生产中也有少量的用作黄色陶瓷器的着色剂。船舶工业中,钨的氧化钨被用作重要的防腐油漆和涂料材料。
氧化钨供应商:中钨在线科技有限公司 | 产品详情: http://www.tungsten-oxide.com |
电话:0592-5129696 传真:5129797 | 电子邮件:sales@chinatungsten.com |
钨钼文库:http://i.chinatungsten.com | 钨钼图片: http://image.chinatungsten.com |
钨新闻3G版:http://3g.chinatungsten.com | 钼业新闻: http://news.molybdenum.com.cn |


钨合金网球拍配重块Ⅳ
- 详细资料
- 分类:钨业知识
- 发布于 2015年12月28日 星期一 14:34
- 点击数:1089
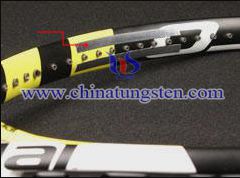
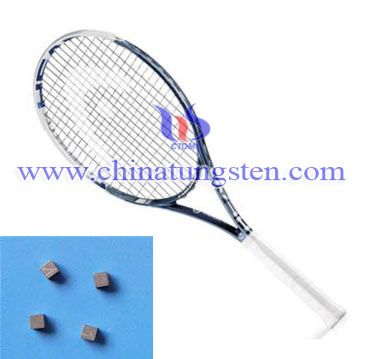
高比重合金供应商:中钨在线科技有限公司 | 产品详情: http://www.tungsten-alloy.com |
电话:0592-5129696 传真:5129797 | 电子邮件:sales@chinatungsten.com |
钨钼文库:http://i.chinatungsten.com | 钨钼图片: http://image.chinatungsten.com |
钨新闻3G版:http://3g.chinatungsten.com | 钼业新闻: http://news.molybdenum.com.cn |

