粉末成形方式
- 詳細
- カテゴリ: 钨业知识
- 2017年4月21日(金曜)09:05に公開
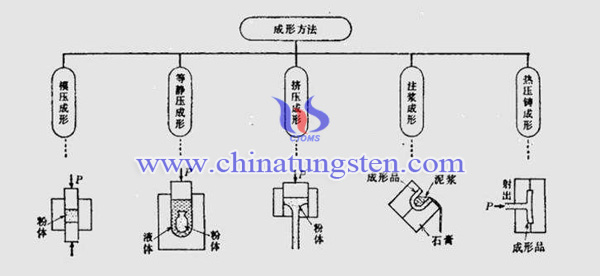
硬质合金供应商:中钨在线科技有限公司 | 产品详情: http://www.tungsten-carbide.com.cn |
电话:0592-5129696 传真:5129797 | 电子邮件:sales@chinatungsten.com |
钨钼文库:http://i.chinatungsten.com | 钨钼图片: http://image.chinatungsten.com |
钨新闻3G版:http://3g.chinatungsten.com | 钼业新闻: http://news.molybdenum.com.cn |


粉末成形过程
- 詳細
- カテゴリ: 钨业知识
- 2017年4月21日(金曜)08:58に公開
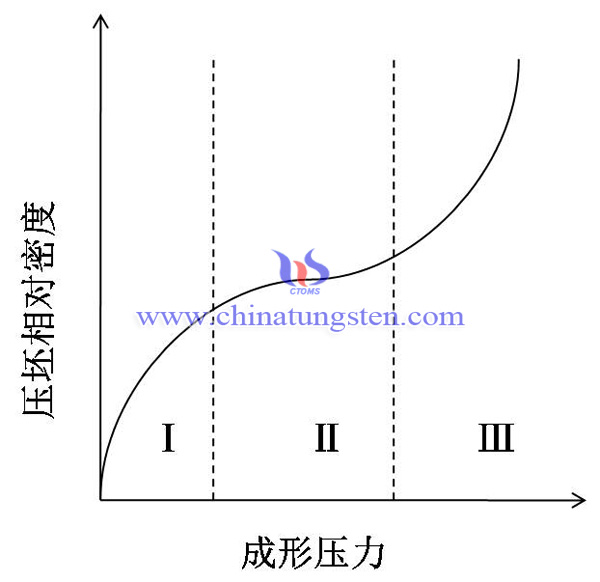
硬质合金供应商:中钨在线科技有限公司 | 产品详情: http://www.tungsten-carbide.com.cn |
电话:0592-5129696 传真:5129797 | 电子邮件:sales@chinatungsten.com |
钨钼文库:http://i.chinatungsten.com | 钨钼图片: http://image.chinatungsten.com |
钨新闻3G版:http://3g.chinatungsten.com | 钼业新闻: http://news.molybdenum.com.cn |


成型剂添加方式
- 詳細
- カテゴリ: 钨业知识
- 2017年4月21日(金曜)08:55に公開
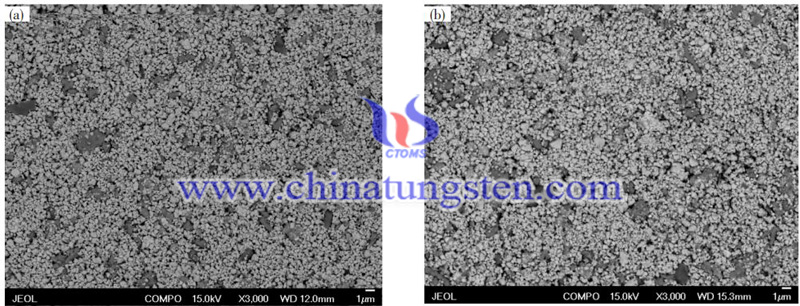
硬质合金供应商:中钨在线科技有限公司 | 产品详情: http://www.tungsten-carbide.com.cn |
电话:0592-5129696 传真:5129797 | 电子邮件:sales@chinatungsten.com |
钨钼文库:http://i.chinatungsten.com | 钨钼图片: http://image.chinatungsten.com |
钨新闻3G版:http://3g.chinatungsten.com | 钼业新闻: http://news.molybdenum.com.cn |


混合料氧含量控制
- 詳細
- カテゴリ: 钨业知识
- 2017年4月20日(木曜)20:36に公開
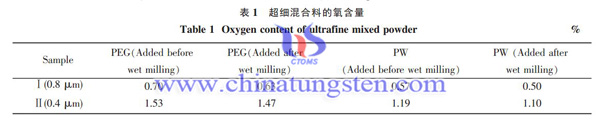
硬质合金供应商:中钨在线科技有限公司 | 产品详情: http://www.tungsten-carbide.com.cn |
电话:0592-5129696 传真:5129797 | 电子邮件:sales@chinatungsten.com |
钨钼文库:http://i.chinatungsten.com | 钨钼图片: http://image.chinatungsten.com |
钨新闻3G版:http://3g.chinatungsten.com | 钼业新闻: http://news.molybdenum.com.cn |


混合料生产中的粒度控制
- 詳細
- カテゴリ: 钨业知识
- 2017年4月20日(木曜)20:34に公開
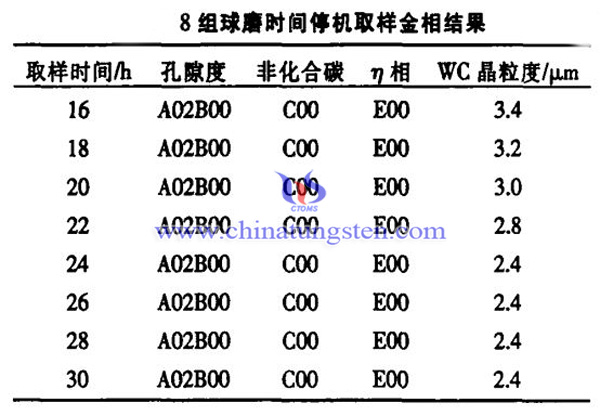
硬质合金供应商:中钨在线科技有限公司 | 产品详情: http://www.tungsten-carbide.com.cn |
电话:0592-5129696 传真:5129797 | 电子邮件:sales@chinatungsten.com |
钨钼文库:http://i.chinatungsten.com | 钨钼图片: http://image.chinatungsten.com |
钨新闻3G版:http://3g.chinatungsten.com | 钼业新闻: http://news.molybdenum.com.cn |


粉末压制侧压力
- 詳細
- カテゴリ: 钨业知识
- 2017年4月20日(木曜)20:22に公開
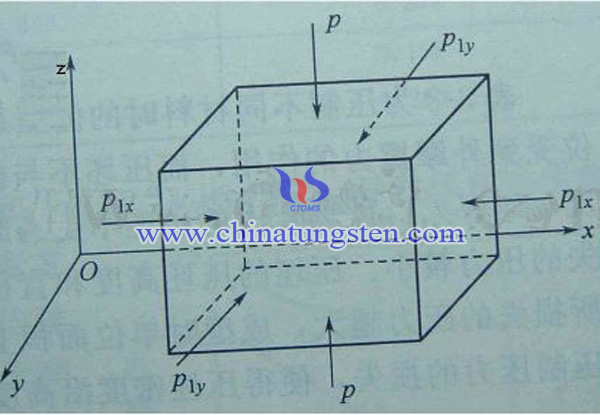
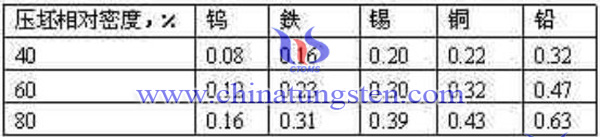
硬质合金供应商:中钨在线科技有限公司 | 产品详情: http://www.tungsten-carbide.com.cn |
电话:0592-5129696 传真:5129797 | 电子邮件:sales@chinatungsten.com |
钨钼文库:http://i.chinatungsten.com | 钨钼图片: http://image.chinatungsten.com |
钨新闻3G版:http://3g.chinatungsten.com | 钼业新闻: http://news.molybdenum.com.cn |


【知钨】高比重钨合金块
- 詳細
- カテゴリ: 钨业知识
- 2017年4月20日(木曜)20:19に公開
更多信息可以访问www.tungsten-alloy.com。
高比重合金供应商:中钨在线科技有限公司
产品详情: http://www.tungsten-alloy.com
电话:0592-5129696 传真:5129797
电子邮件:sales@chinatungsten.com
钨钼文库:http://i.chinatungsten.com
钨钼图片: http://image.chinatungsten.com
钨新闻3G版:http://3g.chinatungsten.com
钼业新闻: http://news.molybdenum.com.cn
【知钨】钨丝
- 詳細
- カテゴリ: 钨业知识
- 2017年4月20日(木曜)20:15に公開
纯钨产品供应商:中钨在线科技有限公司
产品详情: http://www.tungsten.com.cn
电话:0592-5129696 传真:5129797
电子邮件:sales@chinatungsten.com
钨钼文库:http://i.chinatungsten.com
钨钼图片: http://image.chinatungsten.com
钨新闻3G版:http://3g.chinatungsten.com
钼业新闻: http://news.molybdenum.com.cn
压坯密度不均匀性
- 詳細
- カテゴリ: 钨业知识
- 2017年4月20日(木曜)20:14に公開
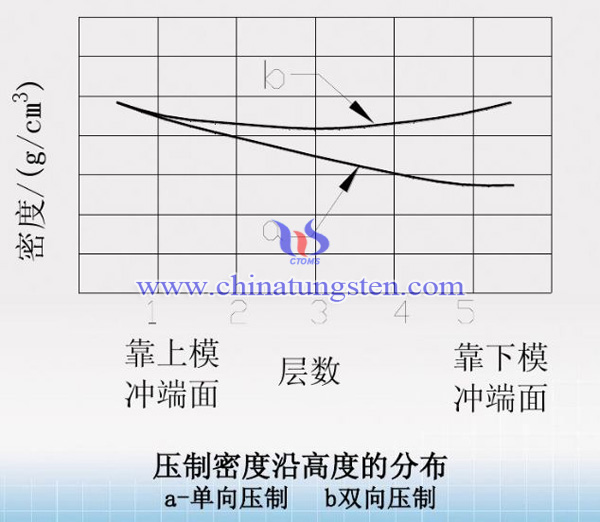
硬质合金供应商:中钨在线科技有限公司 | 产品详情: http://www.tungsten-carbide.com.cn |
电话:0592-5129696 传真:5129797 | 电子邮件:sales@chinatungsten.com |
钨钼文库:http://i.chinatungsten.com | 钨钼图片: http://image.chinatungsten.com |
钨新闻3G版:http://3g.chinatungsten.com | 钼业新闻: http://news.molybdenum.com.cn |


粉末性能对压制质量的影响
- 詳細
- カテゴリ: 钨业知识
- 2017年4月20日(木曜)20:06に公開
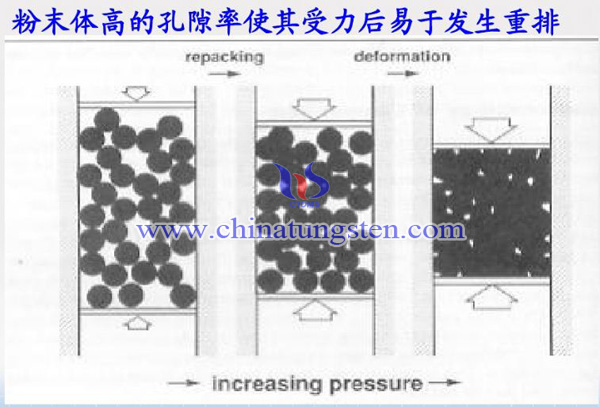