弹性后效对压坯的损害机制
- 詳細
- カテゴリ: 钨业知识
- 2017年4月17日(月曜)19:24に公開
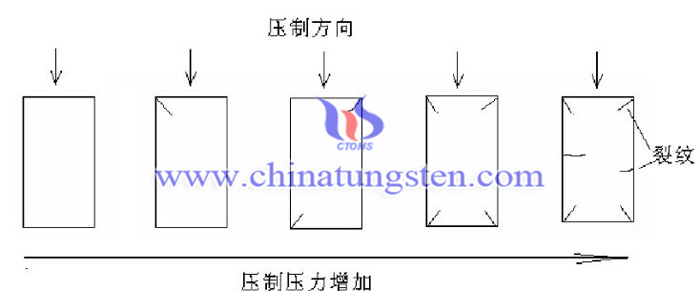
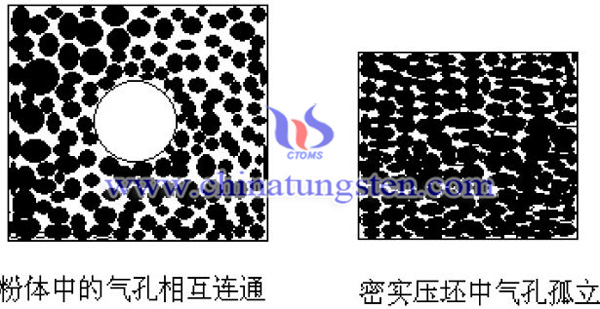
硬质合金供应商:中钨在线科技有限公司 | 产品详情: http://www.tungsten-carbide.com.cn |
电话:0592-5129696 传真:5129797 | 电子邮件:sales@chinatungsten.com |
钨钼文库:http://i.chinatungsten.com | 钨钼图片: http://image.chinatungsten.com |
钨新闻3G版:http://3g.chinatungsten.com | 钼业新闻: http://news.molybdenum.com.cn |


压制弹性后效
- 詳細
- カテゴリ: 钨业知识
- 2017年4月17日(月曜)19:20に公開
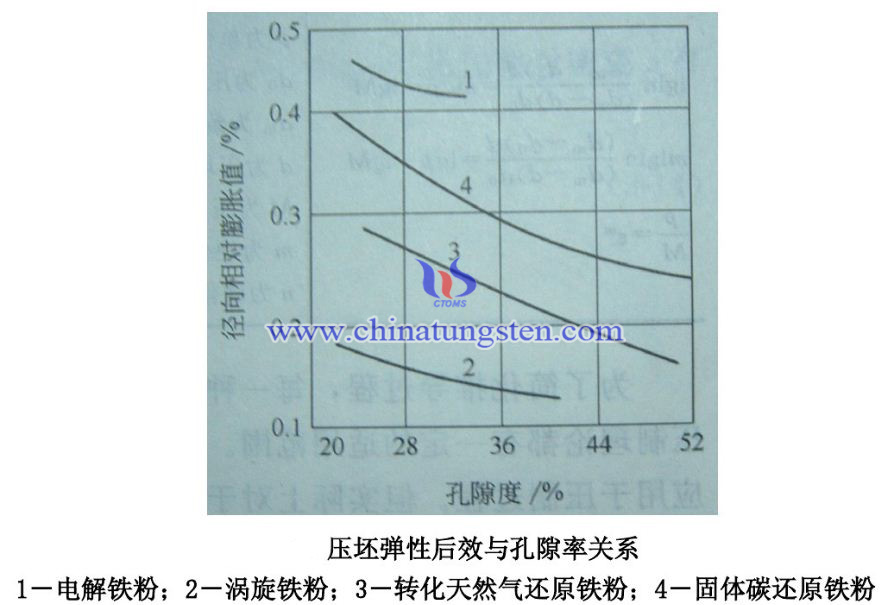
硬质合金供应商:中钨在线科技有限公司 | 产品详情: http://www.tungsten-carbide.com.cn |
电话:0592-5129696 传真:5129797 | 电子邮件:sales@chinatungsten.com |
钨钼文库:http://i.chinatungsten.com | 钨钼图片: http://image.chinatungsten.com |
钨新闻3G版:http://3g.chinatungsten.com | 钼业新闻: http://news.molybdenum.com.cn |


摩擦芯杆压制
- 詳細
- カテゴリ: 钨业知识
- 2017年4月17日(月曜)19:16に公開
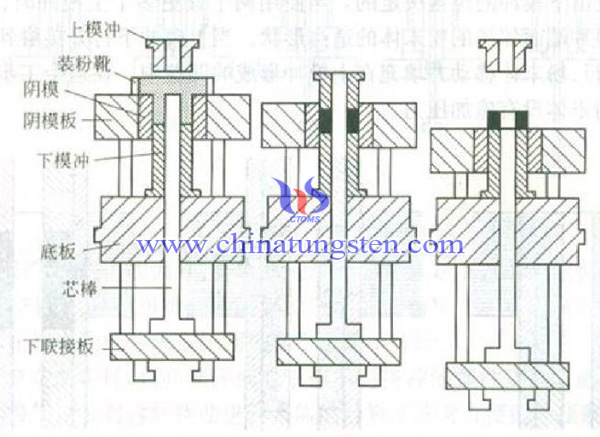
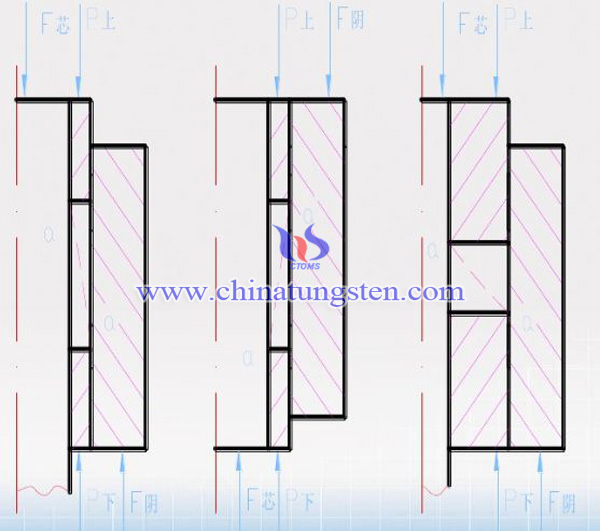
硬质合金供应商:中钨在线科技有限公司 | 产品详情: http://www.tungsten-carbide.com.cn |
电话:0592-5129696 传真:5129797 | 电子邮件:sales@chinatungsten.com |
钨钼文库:http://i.chinatungsten.com | 钨钼图片: http://image.chinatungsten.com |
钨新闻3G版:http://3g.chinatungsten.com | 钼业新闻: http://news.molybdenum.com.cn |


浮动阴模压制
- 詳細
- カテゴリ: 钨业知识
- 2017年4月17日(月曜)19:12に公開
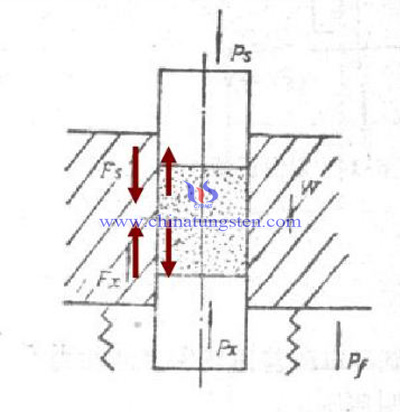
硬质合金供应商:中钨在线科技有限公司 | 产品详情: http://www.tungsten-carbide.com.cn |
电话:0592-5129696 传真:5129797 | 电子邮件:sales@chinatungsten.com |
钨钼文库:http://i.chinatungsten.com | 钨钼图片: http://image.chinatungsten.com |
钨新闻3G版:http://3g.chinatungsten.com | 钼业新闻: http://news.molybdenum.com.cn |


【知钨】钨粉
- 詳細
- カテゴリ: 钨业知识
- 2017年4月14日(金曜)16:13に公開
钨粉供应商:中钨在线科技有限公司
产品详情: http://www.tungsten-powder.com
电话:0592-5129696 传真:5129797
电子邮件:sales@chinatungsten.com
钨钼文库:http://i.chinatungsten.com
钨钼图片: http://image.chinatungsten.com
钨新闻3G版:http://3g.chinatungsten.com
钼业新闻: http://news.molybdenum.com.cn
【知钨】高比重钨合金球
- 詳細
- カテゴリ: 钨业知识
- 2017年4月14日(金曜)16:09に公開
高比重合金供应商:中钨在线科技有限公司
产品详情: http://www.tungsten-alloy.com
电话:0592-5129696 传真:5129797
电子邮件:sales@chinatungsten.com
钨钼文库:http://i.chinatungsten.com
钨钼图片: http://image.chinatungsten.com
钨新闻3G版:http://3g.chinatungsten.com
钼业新闻: http://news.molybdenum.com.cn
【知钨】高比重钨合金
- 詳細
- カテゴリ: 钨业知识
- 2017年4月14日(金曜)16:06に公開
高比重合金供应商:中钨在线科技有限公司
产品详情: http://www.tungsten-alloy.com
电话:0592-5129696 传真:5129797
电子邮件:sales@chinatungsten.com
钨钼文库:http://i.chinatungsten.com
钨钼图片: http://image.chinatungsten.com
钨新闻3G版:http://3g.chinatungsten.com
钼业新闻: http://news.molybdenum.com.cn
【知钨】钨铜电极
- 詳細
- カテゴリ: 钨业知识
- 2017年4月14日(金曜)16:00に公開
钨铜合金供应商:中钨在线科技有限公司
产品详情: http://www.tungsten-copper.com
电话:0592-5129696 传真:5129797
电子邮件:sales@chinatungsten.com
钨钼文库:http://i.chinatungsten.com
钨钼图片: http://image.chinatungsten.com
钨新闻3G版:http://3g.chinatungsten.com
钼业新闻: http://news.molybdenum.com.cn
【知钨】氧化钨
- 詳細
- カテゴリ: 钨业知识
- 2017年4月14日(金曜)15:56に公開
氧化钨供应商:中钨在线科技有限公司
产品详情: http://www.tungsten-oxide.com
电话:0592-5129696 传真:5129797
电子邮件:sales@chinatungsten.com
钨钼文库:http://i.chinatungsten.com
钨钼图片: http://image.chinatungsten.com
钨新闻3G版:http://3g.chinatungsten.com
钼业新闻: http://news.molybdenum.com.cn
【知钨】纯钨
- 詳細
- カテゴリ: 钨业知识
- 2017年4月14日(金曜)15:50に公開
纯钨产品供应商:中钨在线科技有限公司
产品详情: http://www.tungsten.com.cn
电话:0592-5129696 传真:5129797
电子邮件:sales@chinatungsten.com
钨钼文库:http://i.chinatungsten.com
钨钼图片: http://image.chinatungsten.com
钨新闻3G版:http://3g.chinatungsten.com
钼业新闻: http://news.molybdenum.com.cn