Taiwanese military conducting annual Han Kuang military exercises
- Details
- Category: Tungsten News
- Published on Thursday, 18 April 2013 13:43
- Hits: 3790
The Taiwanese armed forces are conducting the annual Han Kuang series of military exercises, in an effort to validate their joint combat readiness in the wake of increasing tensions with China.
Scheduled to conclude on 19 April, the two-stage exercise involves participation from approximately 7,682 personnel from all three military services, and also features a live-fire anti-landing drill on the island of Penghu, Taiwan.
Featuring the public debut of the recently delivered Thunderbolt-2000 multiple rocket launcher system (MLRS), the drill aims to evaluate the military's ability to counter possible amphibious landing assaults and defend an offshore island against an attack by mainland forces.
Eighty one rockets are scheduled to be fired from nine truck-mounted launchers during the drill, which marks the first time live ammunition has been included in the exercises since 2008.
The Taiwanese Navy is participating with a Chengkung-class frigate and Kuang Hua VI fast-attack boats, while the air force has deployed its F-16A/B Fighting Falcon, F-CK-1 Ching-kuo indigenous defence fighter (IDF), as well as the F-5E fighter for the exercise.
Other weapons being used include AH-1W Super Cobra attack helicopters, OH-58D Kiowa Warrior reconnaissance helicopters of the Army Aviation Task Force, in addition to 120mm mortars, M60A3 main battle tanks, and 155mm self-propelled howitzers.
Taiwan Ministry of National Defence (MND) officials were cited by Taiwan Today as saying that the drill also features anti-airborne operations and amphibious landings, as well as mechanised infantry and support manoeuvres, and live-fire manoeuvres.
The exercise represents first part of the Han Kuang drills, while the second part featuring computer-assisted war games to test and strengthen the country's information and electronic warfare capabilities is scheduled to take place from 16 to 20 July.
New Processing Method Makes Precious Matels Cheaper
- Details
- Category: Tungsten News
- Published on Wednesday, 06 March 2013 10:41
- Hits: 3728
Aluminum was once more costly than gold. Napoleon III, emperor of France, reserved cutlery made from it for his most favoured guests, and the Washington monument, in America’s capital, was capped with it not because the builders were cheapskates but because they wanted to show off. How times change. And in aluminium’s case they changed because, in the late 1880s, Charles Hall and Paul Héroult worked out how to separate the stuff from its oxide using electricity rather than chemical reducing agents. Now, the founders of Metalysis, a small British firm, hope to do much the same with tantalum, titanium and a host of other recherché and expensive metallic elements including neodymium, tungsten and vanadium.
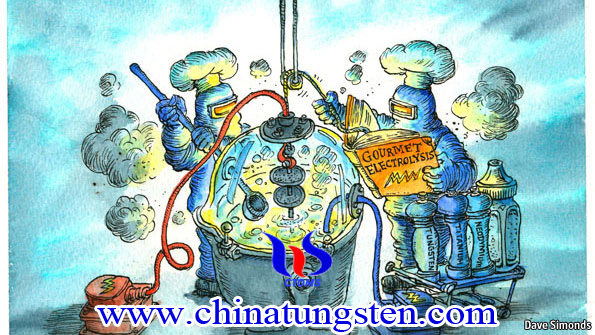
Tel.: 86 592 5129696; Fax: 86 592 5129797
Email: sales@chinatungsten.com
Tungsten News & Tungsten Prices, 3G Version: http://3g.chinatungsten.com
Tungsten News & Tungsten Prices, WML Version: http://m.chinatungsten.com