Performance of the Coated Cemented Carbide Tools
- Details
- Category: Tungsten Information
- Published on Thursday, 29 April 2021 21:50
- Written by Hong
- Hits: 1582
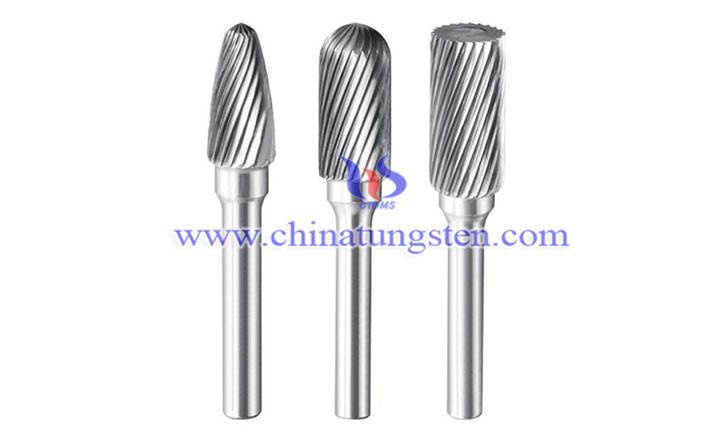
The ratio of coated cemented carbide tools in metal processing industry is increasing steadily. In recent 10 years, its quality and performance have been significantly improved. On the one hand, due to the quality improvement of the coating , it will be better to control porosity and thickness; on the other hand, the metallurgical technology between the coating and the substrate interface has also been improved, therefore can increase the adhesion of the coating and prevent the interfacial reaction that reduces the strength. Increasing cutting speed can significantly improve productivity, and the use of coated tools is the most effective way to reduce costs.
Ultra-fine Integrated Circuit Board Micro Drill Made by Ultra-fine Grained Cemented Carbide
- Details
- Category: Tungsten Information
- Published on Thursday, 29 April 2021 18:08
- Written by Hong
- Hits: 1571
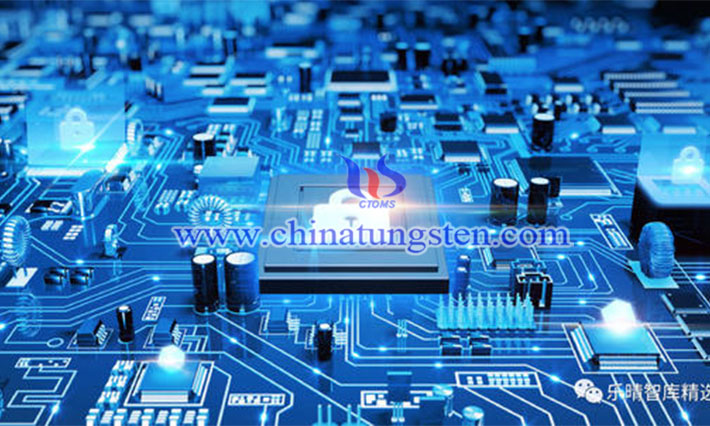
Integrated circuit board (PCB) is the key component of electronic information industry chain, as a key tool of PCB micro hole processing and printing, ultra-fine integrated circuit board micro drillcan only be made by ultra-fine grained cemented carbide.
3D Printing Technology of the Cemented Carbide
- Details
- Category: Tungsten Information
- Published on Thursday, 29 April 2021 17:27
- Written by Hong
- Hits: 1484
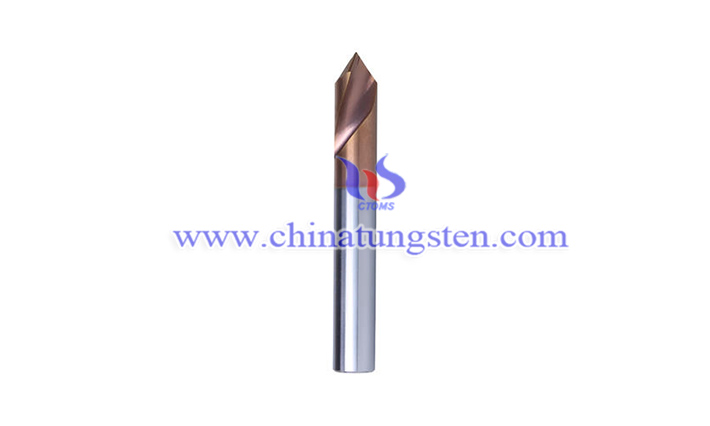
Using the principle of discrete-stacking, 3D printing technology is the manufacturing method to produce molded solid parts by layer-by-layer accumulation way based on three-dimensional model. For the rapid proto typing advantage of complex part, it provides the solution for the preparation of cemented carbide parts to a certain extent. After recent years of development, printing technology has played an increasingly important role in the preparation of precision parts.
Production of Ce-W-Ti Catalyst Using APT with Enhanced NH3-SCR Performance
- Details
- Category: Tungsten Information
- Published on Wednesday, 28 April 2021 20:18
- Written by yuntao
- Hits: 1606
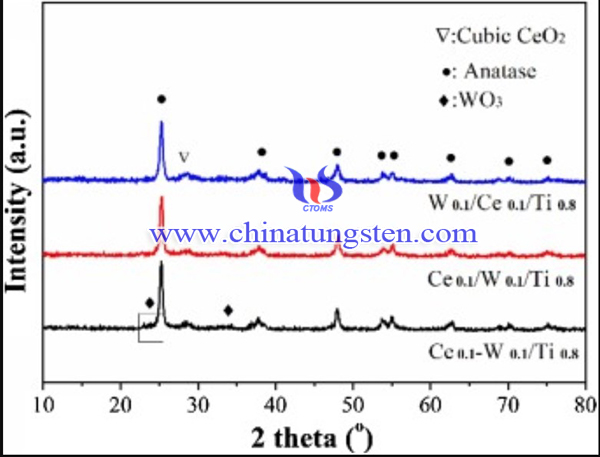
Nitrogen Oxides are a family of poisonous, highly reactive gases. These gases form when fuel is burned at high temperatures. It is major source is from vehicles, trucks, industry facilities and so on.
Iridium-Tungsten Oxide Composite Using APT as Precursor for Electrochemical Water Splitting
- Details
- Category: Tungsten Information
- Published on Wednesday, 28 April 2021 19:21
- Written by yuntao
- Hits: 1681
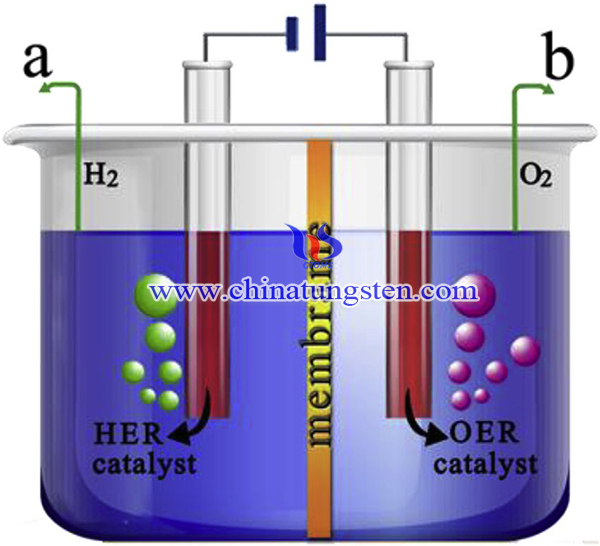
Hydrogen energy is a renewable clean energy that has been believed to be promising substitute to current energy source of fossil fuels. Electrochemical water splitting is a feasible approach to produce hydrogen gas in which hydrogen evolution reaction (HER) and oxygen evolution reaction (OER) taking place at cathode and anode electrodes respectively.
Preparation of Ce-W/Ti Catalyst with APT for Mercury Oxidation Application
- Details
- Category: Tungsten Information
- Published on Wednesday, 28 April 2021 18:34
- Written by yuntao
- Hits: 1584
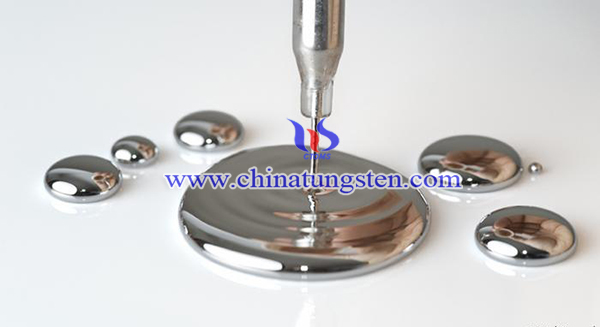
Mercury, serving as a persistent, toxic, bioaccumulative heavy metal, can be transported globally in the atmosphere, therefore mercury pollution is an important public health and environmental concern. Annual mercury emissions of China increased from 147 t in 1978 to 530 t in 2014, in which the contribution rate of coal field was 34%–50%.
V2O5-WO3/Tio2 Catalyst for NO Reduction Using APT
- Details
- Category: Tungsten Information
- Published on Wednesday, 28 April 2021 03:33
- Written by yuntao
- Hits: 1625
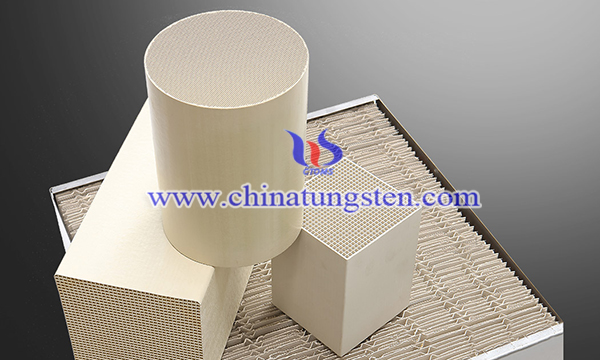
Fossil fuels as the major energy source had contributed to the rapid development of human society. At the same time, the green house gases such as CO2 and NH4 had brought the global warning, climate change, and many other issues. Combustion of most fuels, such as coal, oil, natural gas and biomass etc, results in emission of NOx, which is harmful to our environment creating acid rain and photochemical smog.
Synthesis of WO3 Thin Films with Ammonium Paratungstate for PEC Applications
- Details
- Category: Tungsten Information
- Published on Wednesday, 28 April 2021 03:16
- Written by yuntao
- Hits: 1640
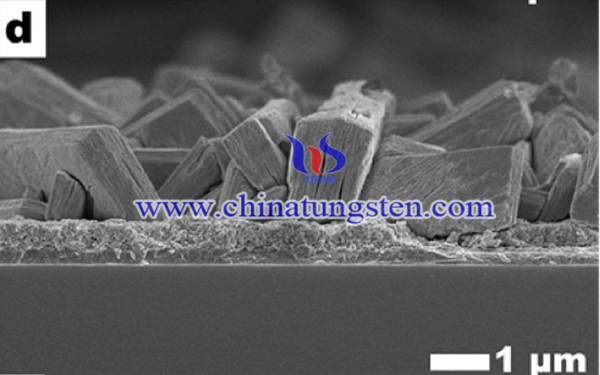
Photoelectrochemical (PEC) water splitting is considered as one of the cleanest, most efficient, and sustainable routes for the production of hydrogen (H2) and an ideal solution for future energy demands. Metal oxide semiconductors are known to be suitable materials for PEC water splitting as they are inexpensive and very stable in aqueous solutions. Moreover, reaching high PEC water splitting efficiency via metal oxide semiconductors is not easy.
Production Method of Molybdenum-Based Catalyst
- Details
- Category: Tungsten Information
- Published on Sunday, 25 April 2021 10:53
- Written by Hong
- Hits: 1551
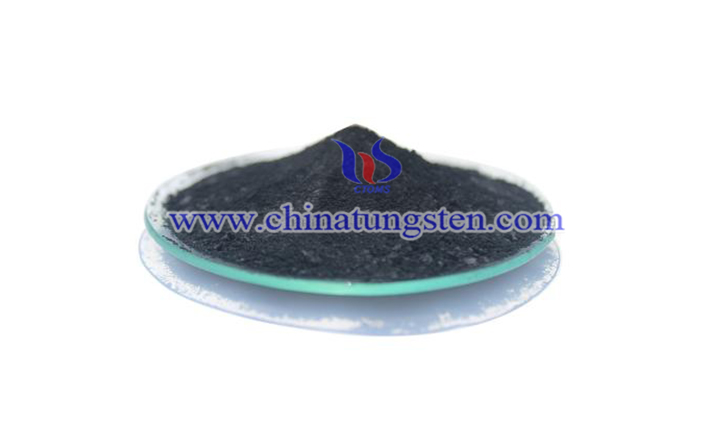
Currently the increasing haze weather in China has attracted high attention on environmental pollution. To control environmental pollution, it is necessary to control the emission of pollutants from motor vehicles. The key is to reduce the content of sulfur and make the desulfurization. At present, more than 95% of refineries in the world use molybdenum-based catalysts for desulfurization, which has the characteristic of high direct desulfurization activity and low hydrogen consumption. The common catalysts are cobalt-molybdenum catalysts and nickel-molybdenum catalysts.
The shape of molybdenum-based catalyst is flake or small ball with the size of 1.2~2.5mm, the color is dark blue, the density is 0.86~1.0g/cm3. It has high activity, good stability, high strength, long life and good sulfur resistance. The producer does not need to spend a lot of money to make deep desulfurization process, so the catalyst will have good economic prospects.
The production method of the catalyst is as follows:
1.0 First puts the required materials including active aluminum oxide powder, deionized water, nitric acid and extruding aid into the kneading machine, fully kneads them, and then extrudes them into the extruding machine.
2.0 Dry and calcine the above mentioned molding materials, the strip shaped alumina carrier is prepared.
3.0 Add cocatalyst, start to prepare Co Mo or Ni Mo aqueous solution according to the formula, and then impregnate or spray the added strip alumina.
4.0 Drain, dry and clacine the product mentioned in 3.0, and then Co Mo hydrodesulfurization catalyst is prepared..
The The catalyst is widely used and has various types, which plays an important role in the field. It is quite suitable for petrochemical and chemical industries. It is often used in petroleum hydrorefining, hydrodenitrogenation or the preparation of acrylic acid and crotonic acid. The catalyst is used in low-carbon industry and falls in green technology. The catalyst market in developing countries such as China will grow rapidly in future and occupy the main position in the catalyst market.
Molybdenum Supplier: Chinatungsten Online www.molybdenum.com.cn | Tel.: 86 592 5129696; Fax: 86 592 5129797;Email:sales@chinatungsten.com |
Tungsten News & Prices, 3G Version: http://3g.chinatungsten.com | Molybdenum News & Molybdenum Price: http://news.molybdenum.com.cn |
Molybdenum Disulfide Used in the Lubrication Field
- Details
- Category: Tungsten Information
- Published on Sunday, 25 April 2021 10:44
- Written by Hong
- Hits: 1486
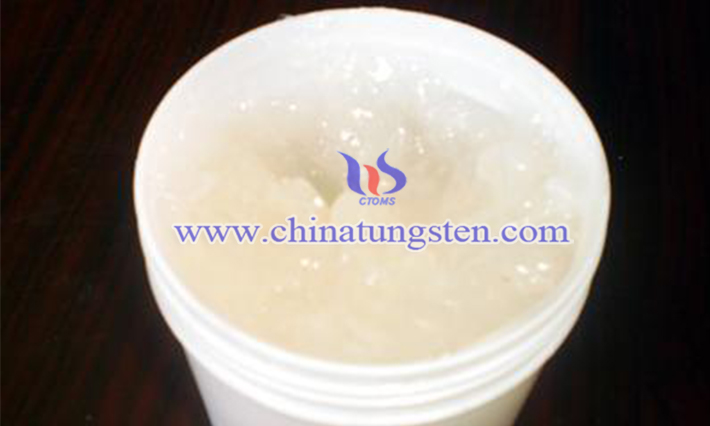
Molybdenum disulfide (MoS2) is known as the "king of lubrication" and has unique advantages in the lubrication field. It has a layered structure and still keeps good lubrication property under severe conditions such as high temperature, high pressure, high rotation, and ultra-low temperature. MoS2 is a kind of natural excellent solid lubricant because of its low friction coefficient with only 0.05. It also has excellent properties such as natural weak alkalinity and excellent anti-oxidation ability, which is used in the aviation field and can extend the mileage of engine oil.
What’s the property of MoS2? It is a kind of black solid powder with metallic luster and the melting point is as high as 1185℃. The chemical and thermal stability are good and the Mohs hardness ranges from 1.0 to 1.5. The initial decomposition temperature is 1370℃when it reaches 1600℃, it decomposes into metal molybdenum and sulfur. MoS2 is insoluble in water, dilute acid and concentrated sulfuric acid, generally insoluble in other acids, alkalis, and organic solvents, but soluble in aqua regia and boiling concentrated sulfuric acid.
The basic material of molybdenum disulfide lubricant is made of ultra-fine MoS2. When the lubricant is used on the metal surface, a dry film will be shaped quickly on the surface to make the protective film on the surface of metal parts, which can resist high temperature, strong pressure, tenacity, and parts are not easy to wear, burn and bite.
MoS2 can be used for lubrication in many situations, some examples are as follows:
1.0 As the parts such as slide rails for cabinets or drawers, guide rails for elevators and bearings for motors etc. bear high pressure under high load, they need lubricant to reduce friction and prolong service life.
2.0 In the process of material machining, the material needs to be punched, stamped, etc., and lubricant needs to be applied to minimize the friction between the mold and the plate, then produce finished product meeting the requirements, which can prevent rust on the surface of the material.
3.0 In some extreme environments, it is easy for fasteners and threads to slip or bite during assembly. It is necessary to use lubricant to reduce friction, avoid parts sticking and prevent rust.
Molybdenum Supplier: Chinatungsten Online www.molybdenum.com.cn | Tel.: 86 592 5129696; Fax: 86 592 5129797;Email:sales@chinatungsten.com |
Tungsten News & Prices, 3G Version: http://3g.chinatungsten.com | Molybdenum News & Molybdenum Price: http://news.molybdenum.com.cn |