WO3/TiO2-ZrO2 SCR Denitration Catalyst
- Details
- Category: Tungsten Information
- Published on Monday, 23 May 2016 17:13
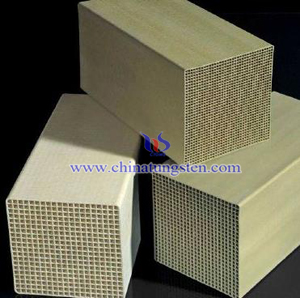
It is well known that the first step of SCR denitration reaction is ammonia adsorption, the longer residence time benefits the reaction at the catalyst surface. The doped of tungsten oxide and zirconium oxide makes catalyst having superior storage capacity of ammonia, thus to conducive to the denitration reaction. Experimental prepared tungsten trioxide denitration catalyst doped zirconium, which showed as follows:
1. Prepare titanium oxide-zirconium oxide solid-solution vector (the molar ratio of Ti and Zr is 1) by coprecipitation method
Dropwise the titanium tetrachloride into deionized water containing zirconium oxychloride under the condition of ice-cooling with stirring;
2. After completing the addition, adjust the pH value to 9~10 with concentrated aqueous ammonia, stand for 12h after the white precipitate producing, then discard the upper-layer of serum;
3. Wash the precipitate with deionized water and go through vacuum filtration, until no Cl- exists;
4. Dry the washed the precipitate in an oven at 110℃ for 12 hours, grinding, and calcined in a muffle furnace at 450℃ for 4 hours to titanium-zirconium solid solution;
5. Preparation of WO3/TiO2-ZrO2 catalyst, add ammonium tungstate into titanium-zirconium solid solution, then going through a oil bath at 25 ℃ for 4 hours and evaporating off all of the moisture at 85℃;
6. Dip the ammonium paratungstate under the condition of magnetic stirring with stirring, and then evaporated to get the dryness solid, transferred to an oven at 110℃ for 12 hours; calcined in a muffle furnace at 450 ℃ for 4 hours after milled to give the desired WO3/TiO2-ZrO2 denitration catalyst.
Tungsten Oxide Supplier: Chinatungsten Online www.tungsten-oxide.com | Tel.: 86 592 5129696; Fax: 86 592 5129797;Email:sales@chinatungsten.com |
Tungsten News & Prices, 3G Version: http://3g.chinatungsten.com | Molybdenum News & Molybdenum Price: http://news.molybdenum.com.cn |