WO3 Hydrodesulfurization Catalyst - Regeneration Flue Gas Treatment 1/2
- Details
- Category: Tungsten Information
- Published on Wednesday, 11 May 2016 18:02
Adsorbent of gasoline desulfurization requires roasted and regenerated after adsorption saturation, while the regeneration flue gas still has a high content of sulfur dioxide. A secondary pollution will produce when using alkali absorption method to remove the sulfur dioxide, and cause wasting of sulfur resource at the same time. Generally, the volume content of sulfur dioxide in the regeneration flue gas is up to 5.4%, oxygen is up to 3.0%, while the temperature is only 160°C. However, the prior art Claus tail gas hydrogenation catalyst requires the volume content of sulfur dioxide less than 0.5%, the oxygen less than 0.05% at a temperature of over 280°C, which can’t meet the requirements of Flue gas desulfurization regeneration adsorption gasoline hydrotreating.
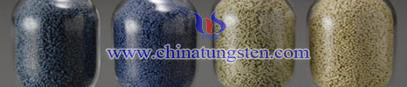
Chinese patent has referred a new method for processing sulfur-containing gas and developed a tungsten trioxide hydrodesulfurization catalyst with high activity for the hydrogenation of sulfur dioxide and lower using temperatures and, while recovering sulfur resource and avoiding environmental pollution. The catalyst is prepared as follows:
1. Preparation of carrier: Put titanium aluminum composite adhesive (the pore volume greater than 0.6mL/g, a specific surface area greater than 250m2/g, a sodium content less than 0.1%, S042- content less than 0.2%), binders (e.g. water, or nitric, acetic, oxalic and citric acid), expanding agent (such as polyvinyl alcohol, polyacrylamide, sesbania powder, citric acid, starch) into a kneader, extruded into a cloverleaf orifice (or other shape); then dry at 110~150°C for 2~4 hours, calcine at 500~600°C for 2~5 hours to obtain the catalyst carrier;
2. Preparation of semi-finished product
Add stabilizer (citric acid, acetic acid, hydrochloric acid or sulfurous acid) into the deionized water, stir to dissolve; then add the desired amount of deoxidation additives with stirring to completely dissolve to form a stable solution; and then immersing the carrier in the solution for the 0.5~1 hour, then drying at 110~150°C for 2~6 hours, calcining at 200~500°C for 2~5 hours to obtain the catalyst semi-finished product;
Tungsten Oxide Supplier: Chinatungsten Online www.tungsten-oxide.com | Tel.: 86 592 5129696; Fax: 86 592 5129797;Email:sales@chinatungsten.com |
Tungsten News & Prices, 3G Version: http://3g.chinatungsten.com | Molybdenum News & Molybdenum Price: http://news.molybdenum.com.cn |