WO3 Loaded High-Temperature Exhaust Denitration Catalyst
- Details
- Category: Tungsten Information
- Published on Tuesday, 10 May 2016 18:48
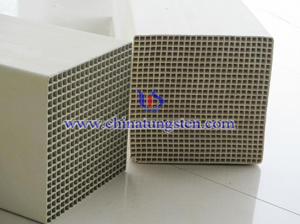
A kind of denitration catalyst is taking tungsten trioxide as the active ingredient, titanium and zirconium composite oxide as an inorganic refractory oxide carrier which can suppress the decreasing of specific surface area, and thus load the particular active metal, so that it can maintain the denitration performance at above 500°C for a long time. It is prepared as follows:
1. Sinter either of the silica or zirconium compound and titanium oxide at about 500°C to obtain titanium-zirconium or titanium-silicon composite oxide carrier;
2. Load tungsten trioxide on the generated composite oxide carrier, then sintered under the same level or 50°C higher than the using temperature (for example, 650°C) to get the tungsten trioxide denitration catalyst powder;
3. Pulverize the catalyst powder into smaller particles, sieved, and then pressed to molding (honeycomb type, flat type, etc.) to give the tungsten trioxide loaded high-temperature exhaust denitration catalyst.
The high temperature exhaust denitration catalyst sets the molecule layers of tungsten trioxide less than 5 layers, which plays the role of keeping the appropriate binding force between tungsten trioxide and carrier in the case of high temperature, thus possible to maintain high denitration activity while suppress the volatilization.
Tungsten Oxide Supplier: Chinatungsten Online www.tungsten-oxide.com | Tel.: 86 592 5129696; Fax: 86 592 5129797;Email:sales@chinatungsten.com |
Tungsten News & Prices, 3G Version: http://3g.chinatungsten.com | Molybdenum News & Molybdenum Price: http://news.molybdenum.com.cn |