Development of High Performance Tungsten Carbide Mining Button
- Details
- Category: Tungsten Information
- Published on Saturday, 29 September 2018 22:16
Geological mining tools are a major use of tungsten carbide. The drilling volume of 60% ~ 80% in geological exploration and mining is achieved by tungsten carbide bit. In China, tungsten carbide for geological and mining purposes accounts for 27% of the total production. Chinese consumption of mining alloys in 2015 was 10978t. As the grade of mines continues to decrease and the depth of mining continues to expand, the use of tungsten carbide mining button in the next 5 years is expected to maintain an average annual growth of 30%.
Button-typed tungsten carbides are a large class of applications in mining alloys. Tungsten carbide button is made up of tungsten carbide spherical teeth brazing and alloy structural steel. It is generally used for cutting and mining coal directly by shearers, so they are also called tungsten carbide coal mining button. As a cutting tool for cutting coal and rock, it is mainly used in open channel in large water-power engineering, coal mining, diversion tunnel, excavation of large underground power plant, stone quarries for various projects (reclamation, airport, traffic roadbed) and so on. Mining buttons include roughly the driving teeth for entry-driving machine, pickaxe for coal cutter, knife-typed pick, rotary excavating teeth for rotary drilling rig, milling gear for milling machine and bucket tooth for excavator.
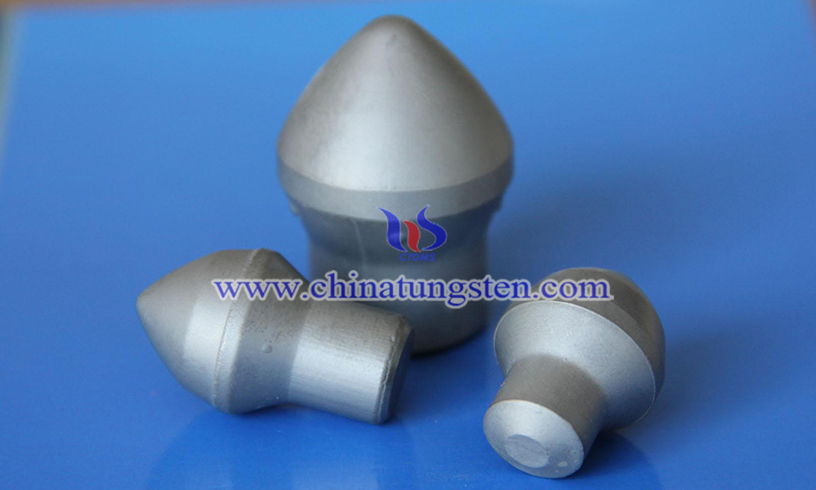
Some scholars dissected the products of two foreign advanced mining alloy enterprises. And advanced products were successfully developed and manufactured through a series of techniques including classification of WC powder, wet milling process of alternate addition of raw material powder and wax, press pellet pelleting and controlling of mixture powder particle size via vibration sieve. A gradient layer with 1.5 mm thickness was formed on the surface of the carbide tip after functionally graded treatment, thus the surface hardness was increased up to 87.5 HRA while maintaining the core toughness, which increased the wear resistance of the tungsten carbide. Its applicability are verified by site tests, of which the results are as follows.
(1)Tungsten carbide with the brand of JCK1 has good wear resistance, and its physical properties are consistent with the similar products abroad.
(2)After gradient treatment, an external hard and internal tough structure are formed on the surface of the tungsten carbide, which not only improved the wear resistance of the alloy surface, but also maintained the overall toughness of the alloy. In a word, effectively solving the contradiction between wear resistance and toughness of conventional tungsten carbide.
(3)By force of application contrast, gradient tungsten carbide mining button have obvious advantages in wear resistance and impact toughness. The replacement amount of brazing tools has been reduced by about 32%, and the ideal application effect has been achieved, which has been approved by customers.
- Tungsten Carbide Manufacturer & Supplier, Chinatungsten Online: tungsten-carbide.com.cn
- Tungsten News & Prices of China Tungsten Industry Association: www.ctia.com.cn
- Molybdenum News & Price: news.molybdenum.com.cn
- Tel.: 86 592 5129696; Fax: 86 592 5129797; Email: sales@chinatungsten.com