Brief Introduction of The Tungsten Carbide Drawing Die (2)
- Details
- Category: Tungsten Information
- Published on Thursday, 12 July 2018 16:52
Drawing method is mainly used in copper pipe production at present. In the process of drawing, due to the high temperature and large friction, high temperature resistance and high hardness of the die are required. Therefore, most of the drawing dies are tungsten carbide drawing die.
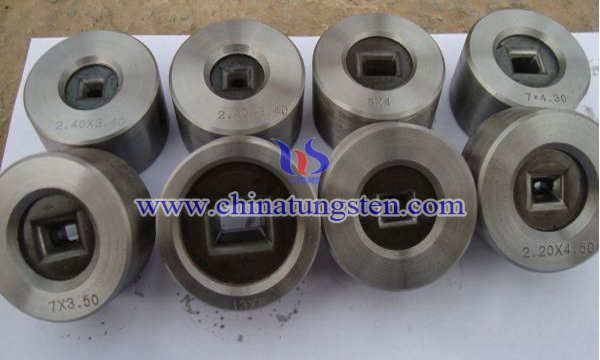
It is an ancient process to produce seamless metal pipes by drawing. After the success of hot extrusion of copper tube in 1894, the drawing process of tube has been developed rapidly. In the early 1920s, with the rise of European capitalism, the length of pipe produced by fixed core production could no longer meet the demand. Against this background, in 1929, L Bethell was first successful in the production of copper pipes by pulling the floating core, and was patented in France, and obtained the patent right in the United States in 1939.
The third stage (1950-1969) is the mature stage of tungsten carbide mold industry. With the recovery and development of post-war world economy, the demand and application fields of tungsten carbide drawing die have expanded significantly. Main features of this stage are as follows.
First, in the development of production, some new production equipment has been developed, further improving the production technology. Two, the field of application was further expanded, which are almost develop to all industrial sectors. Three, a series of new materials and new grades have been developed, laying a good foundation for the development of modern tungsten carbide die industry. Four, the production extends to the deep processing and tool matching, thus marking the world tungsten carbide mold industry has entered the mature stage.
The fourth stage (1970 to present) is the precision stage of the world tungsten carbide mold industry. In 70s, the requirements for the geometric design and precision of the tungsten carbide products for cutting tools were greatly improved by the modern mechanical processing technology. The manufacturers constantly improved the precision of their products and introduced the high efficiency groove structure. Therefore, the requirements for dimensional accuracy of tungsten carbide die are more stringent, of which the sizes mostly have reached micron level or even super micro meter level.
Main characteristics of this stage are as follows. First, in order to adapt to the development of science and technology, tungsten carbide is developing towards precision. Two. In order to adapt to the production of high performance products, the production process and equipment are constantly improved, and some new tungsten carbide, especially superfine tungsten carbide, coating alloys, and recently developed nanostructure alloys have been developed. Three, it further developed towards deep processing and tool matching. Four, in order to improve processing efficiency and adapt to the needs of automatic processing, tungsten carbide mold industry is extending to the new field of ceramics and superhard materials.
Due to the high wear resistance and hardness, high modulus of elasticity, high compression resistance and small thermal expansion coefficient, tungsten carbide is widely used in various moulds
- Tungsten Carbide Manufacturer & Supplier, Chinatungsten Online: tungsten-carbide.com.cn
- Tungsten News & Prices of China Tungsten Industry Association: www.ctia.com.cn
- Molybdenum News & Price: news.molybdenum.com.cn
- Tel.: 86 592 5129696; Fax: 86 592 5129797; Email: sales@chinatungsten.com